Mythos Sondermüll: Batterie-Recycling funktioniert!
Als rollender Sondermüll wird die Batterie eines Elektroautos gern am Verbrenner-Stammtisch verunglimpft. Wir konnten uns bei der Spezialfirma Duesenfeld vom Gegenteil überzeugen und räumen nun mit diesem Mythos auf. Batterie-Recycling funktioniert bis tief in die Zelle hinein. Die Politik muss nur den Rahmen für einen Recycling-Kreislauf definieren.
* * *
Metalle, überall Metalle: Ein Batteriesystem besteht aus Stahl und Aluminium, aus Lithium, Kupfer, Kobalt und Nickel. Dazu kommen andere Materialien wie Kunststoffe für die Isolierung oder der flüssige Elektrolyt. Ein pro Fahrzeug mehrere hundert Kilogramm schwerer Mix. Und der könnte irgendwann wertvoll sein – ein industriell funktionierendes Recyclingnetzwerk muss also aufgebaut werden: Wegen des Umweltschutzes, wegen der Ressourcenschonung und perspektivisch auch aus Kostensicht.
Bis die Traktionsbatterie eines Elektroautos nach dem Refurbishment und dem Second Use – zum Beispiel als stationärer Speicher – endgültig kaputt ist, werden viele Jahre vergehen. Irgendwann wird die Verwertung des wichtigsten Bauteils eines Elektroautos aber massenwirksam sein. Das Ziel des Recyclings muss die höchstmögliche Rückgewinnung und Wiederverwendung sein.
Wer sich für Elektromobilität interessiert, kennt die Polemiken und kruden Thesen über Lithium-Ionen-Batterien. Richtig ist: Der Umgang damit ist keineswegs trivial oder risikofrei. Wer mit großen Energiemengen hantiert, sollte grundsätzlich vorsichtig sein. Das weiß auch Christian Hanisch, Geschäftsführer, Gesellschafter und Vordenker von Duesenfeld. Die Redaktion von electrive.net hat das Recyclingunternehmen vor Ort besucht, nur 13 Kilometer von Volkswagens Batteriefertigungshalle in Braunschweig entfernt.
Mobile Verwertungstechnik spart hohe Transportkosten
Duesenfeld steht einerseits exemplarisch für den aktuellen Stand des Recyclings, weil einige Arbeitsschritte ähnlich wie etwa beim Branchenriesen Umicore aus Belgien ablaufen. Andererseits hat Hanisch das Verfahren entscheidend weiterentwickelt: Das Ergebnis der Innovation ist ein erheblich reduzierter Energieeinsatz, darum eine verbesserte CO2-Bilanz, eine hohe Recyclingeffizienz sowie die Möglichkeit der Mobilität der Verwertungstechnik – das dezentrale Recycling ist unter anderem nützlich, weil damit die wegen der Gefährlichkeit hohen Transportkosten gespart werden.
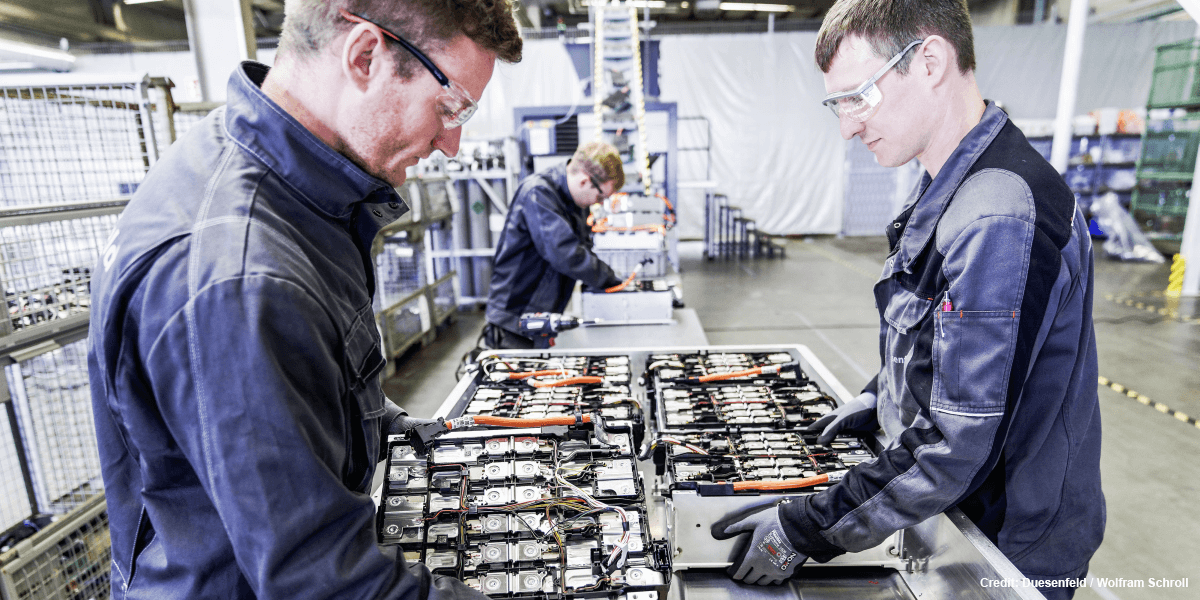
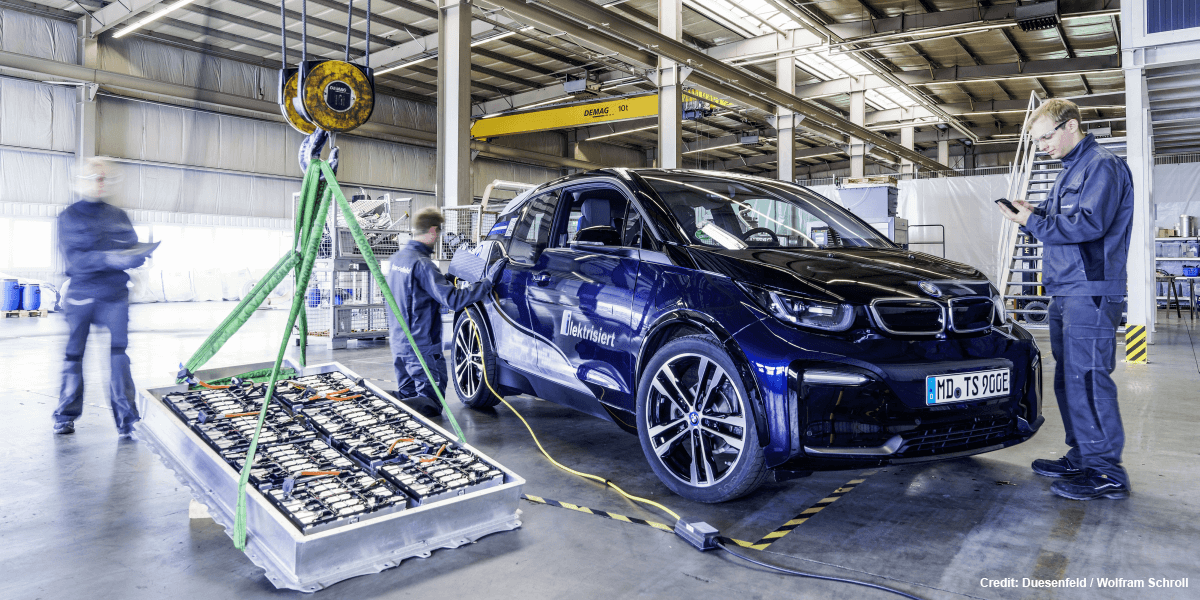
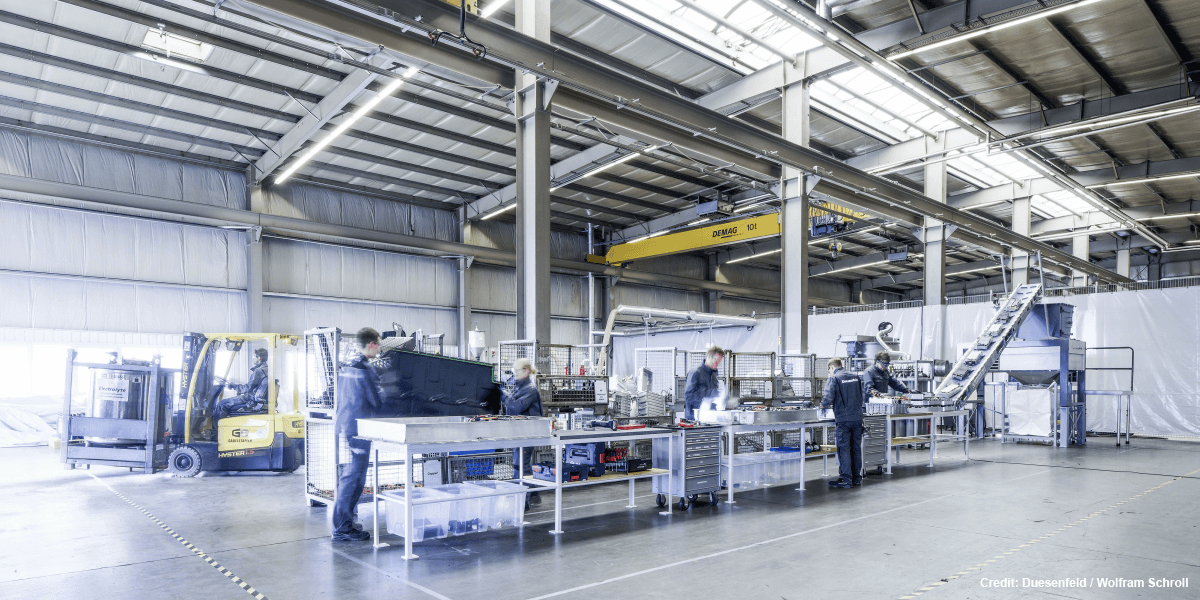
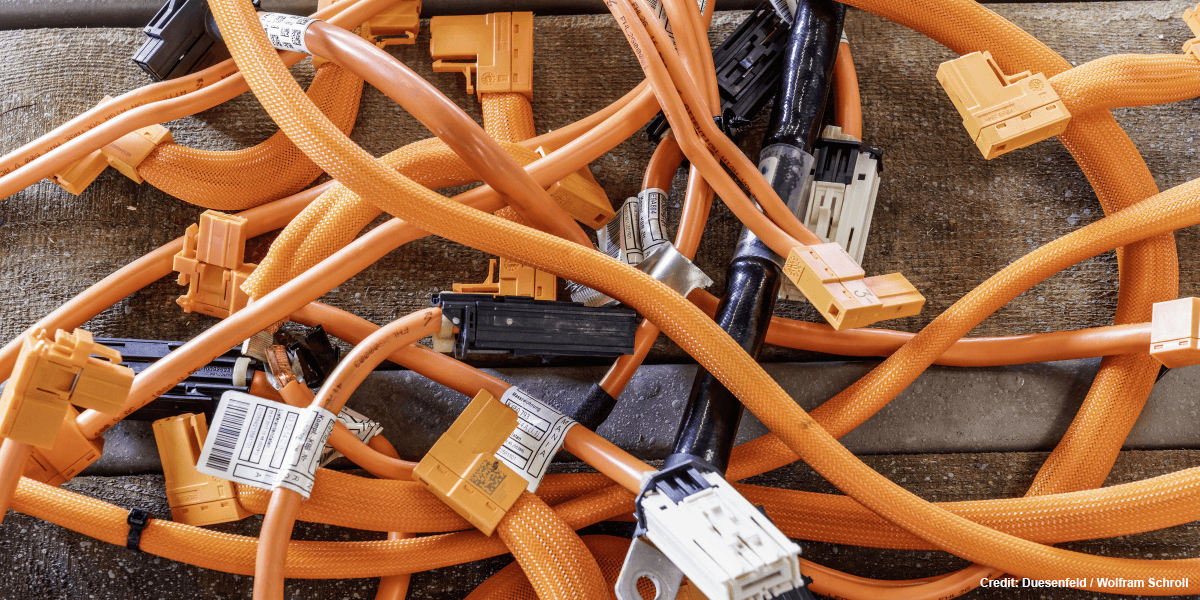
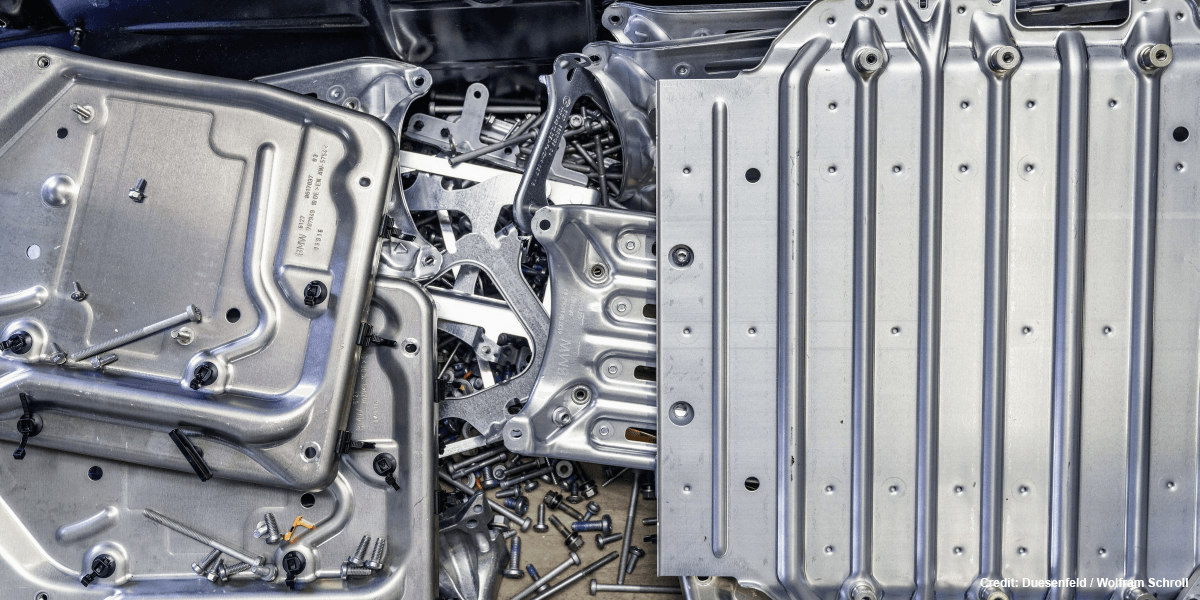
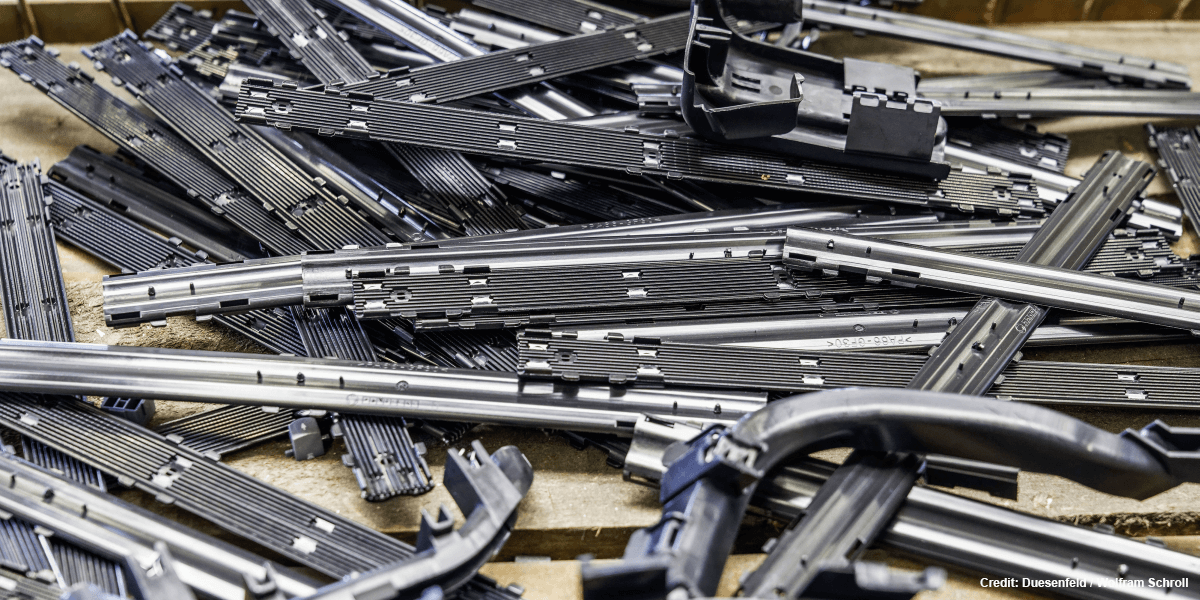
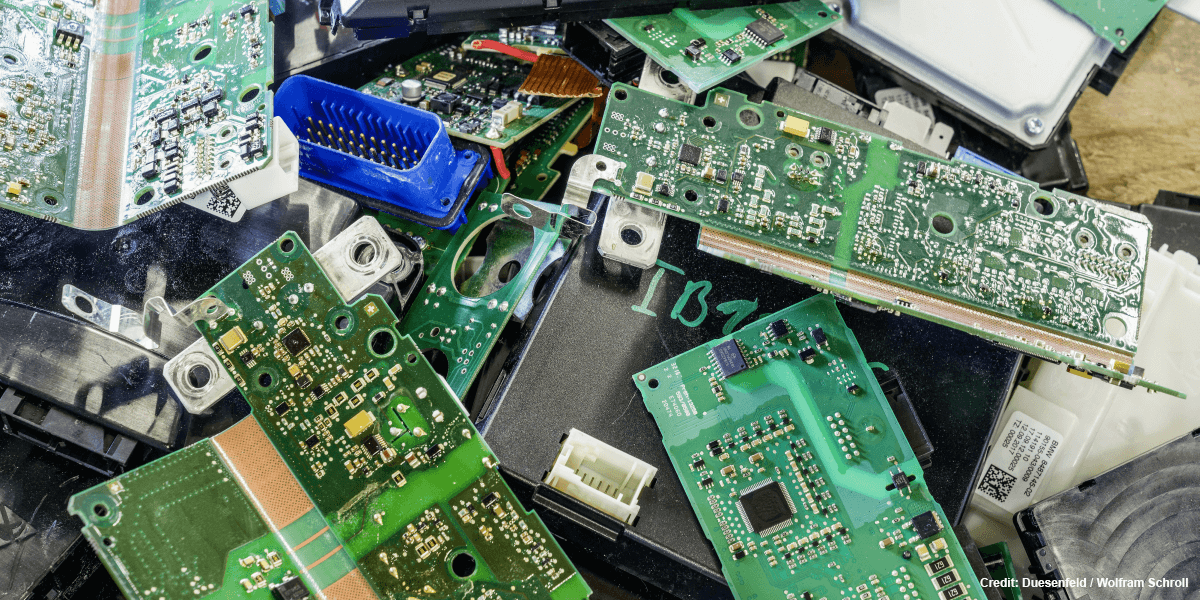
Der Branchendienst electrive.net konnte bei der Zerlegung mehrerer BMW i3-Batterien zuschauen. Sie müssen zuerst tiefentladen werden. Dazu wird das Batteriemanagementsystem ausgeschaltet. Der Reststrom wird übrigens genutzt, um die Anlage zu unterstützen. Nach der Entladung, und hierin gleichen die Arbeitsschritte noch denen bei anderen Recyclingfirmen, werden die Batterien händisch zerlegt. Die crashsichere Außenhülle mit weiteren Haltestrukturen, Kabeln, dem Kühlkreislauf und den Modulen kann mit einfachem Werkzeug demontiert werden und landet sortenrein in Gitterboxen.
Hier beginnen die Unterschiede bei Duesenfeld: Bei vielen Unternehmen kommt nun die so genannte thermische Zerlegung in einem stark gesicherten Ofen. Bei 450 bis 500 Grad öffnen sich die Ventile der Zellen, und der kritische Elektrolyt verbrennt schlagartig; eine perfekte Trennung der verbliebenen Materialien ist jetzt schwieriger.
Testrecycling mit Reststoffanalyse
„Wir arbeiten mit Mechanik statt Temperatur und zerkleinern das komplette Modul in einer inerten Atmosphäre“, erklärt Christian Hanisch von Duesenfeld. Im Schredder befindet sich Stickstoffgas, das weitere chemische Reaktionen verhindert. Anschließend wird der Druck stark reduziert, wodurch der flüssige Elektrolyt erst verdampft und danach durch Kondensation zurückgewonnen wird. Neben dem mahlenden Schredder läuft der Elektrolyt in einen Behälter.
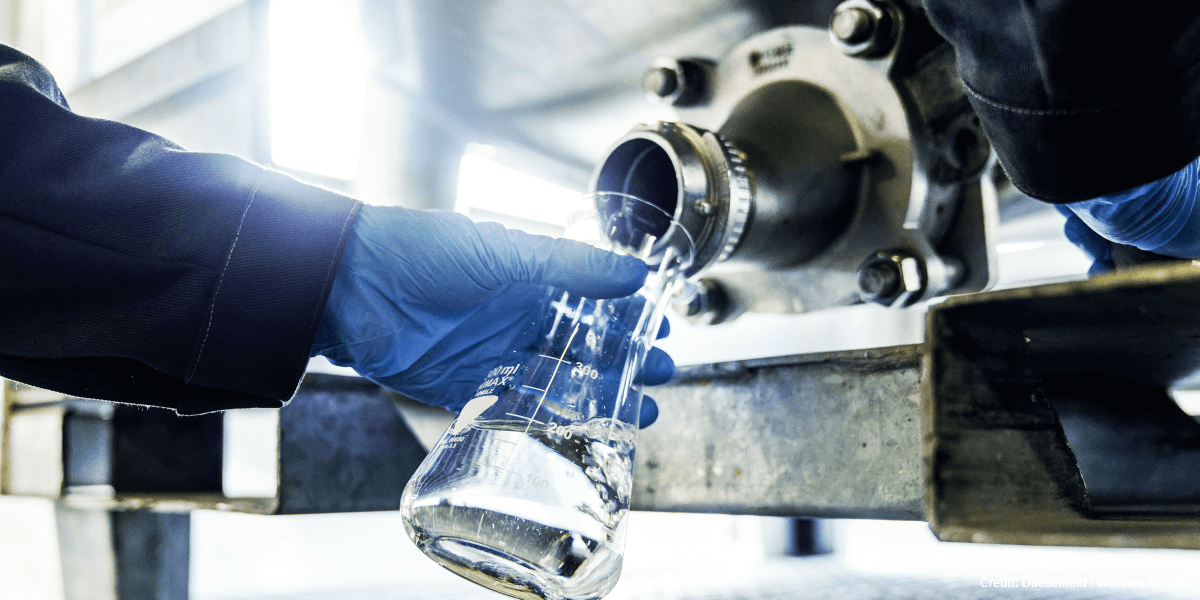
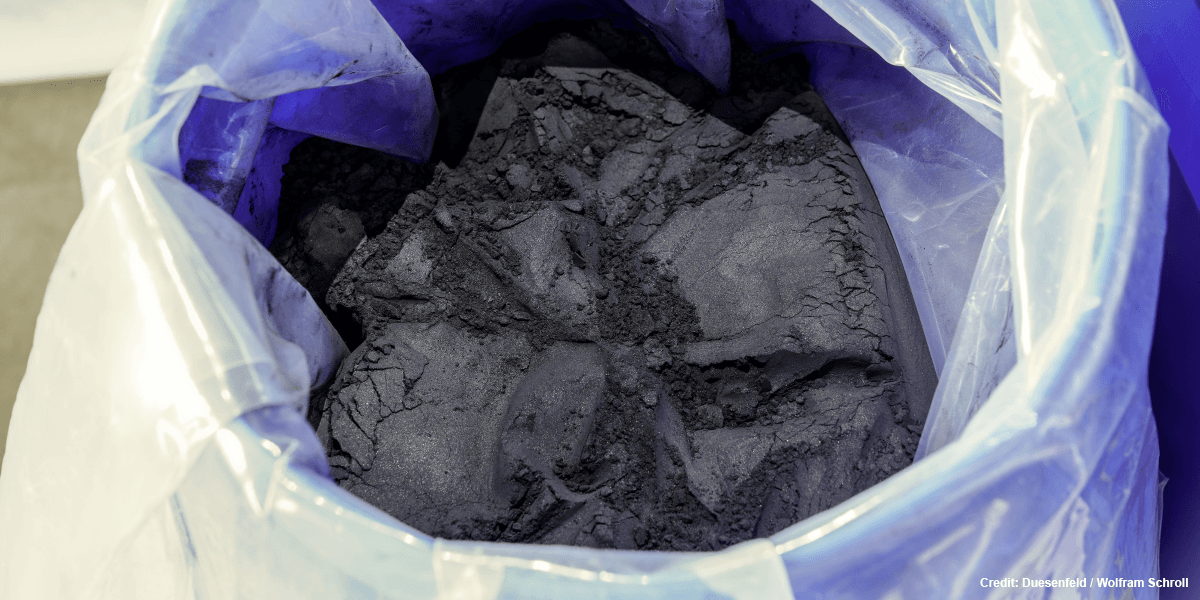
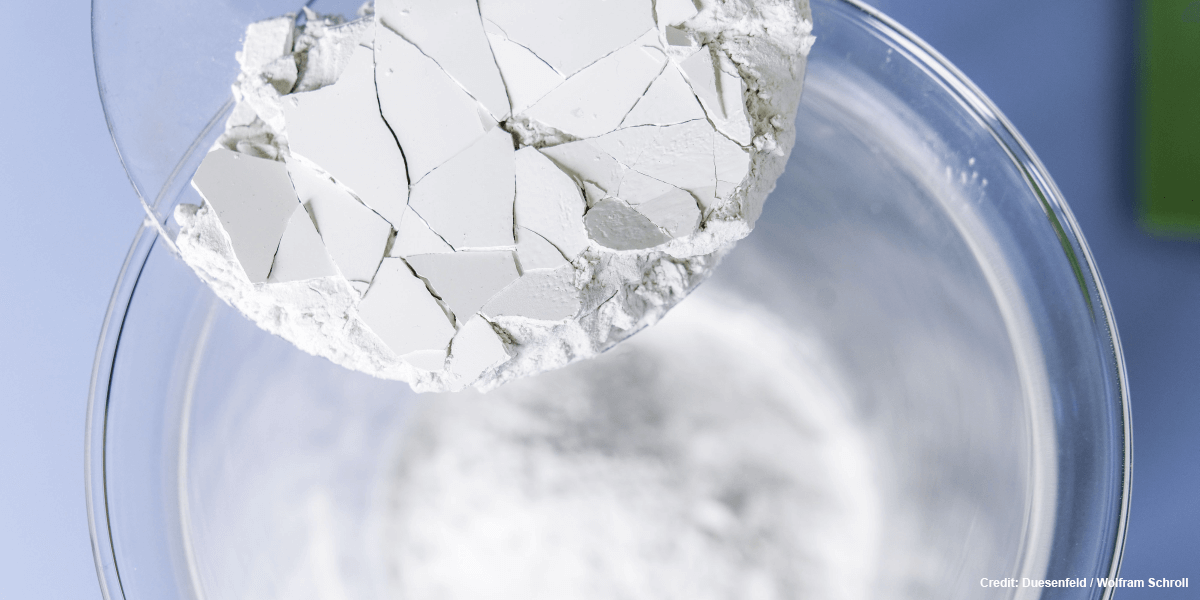
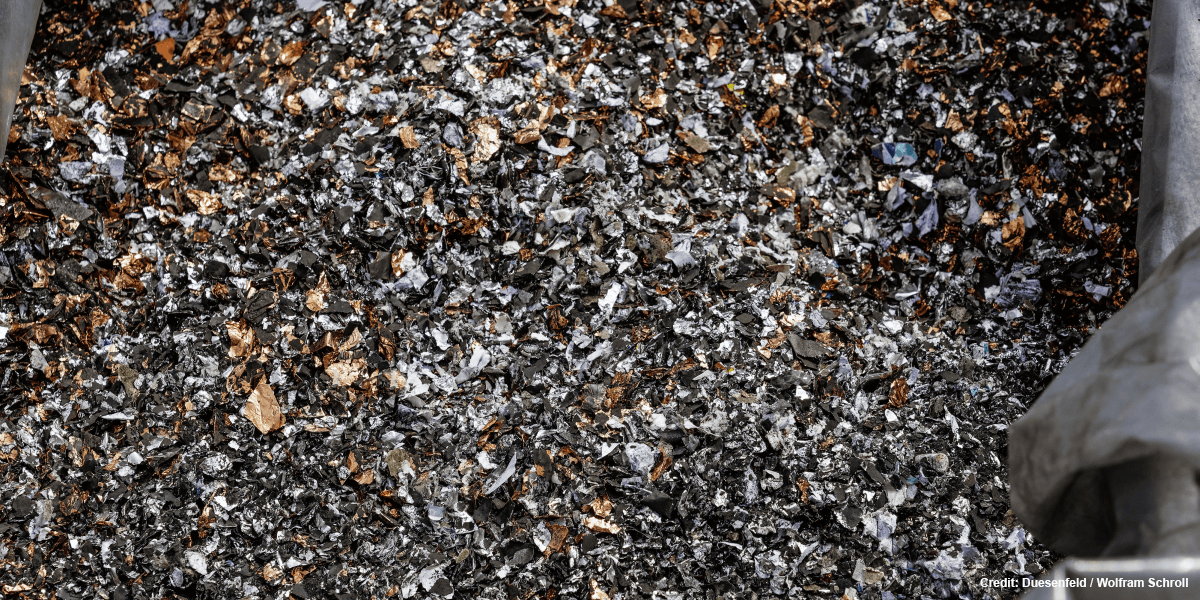
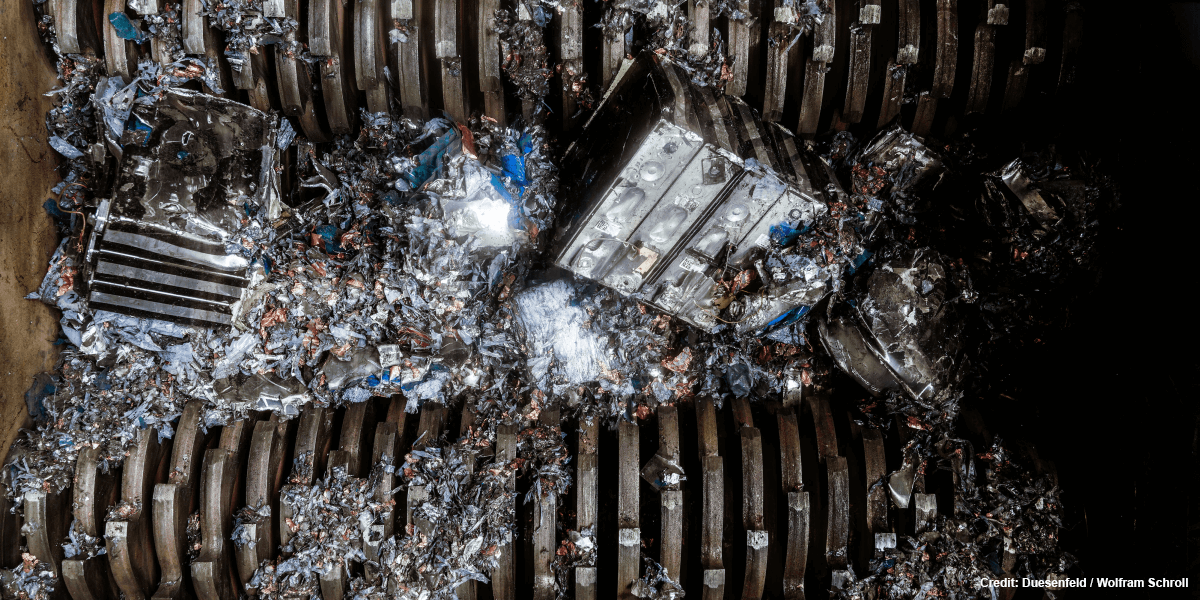
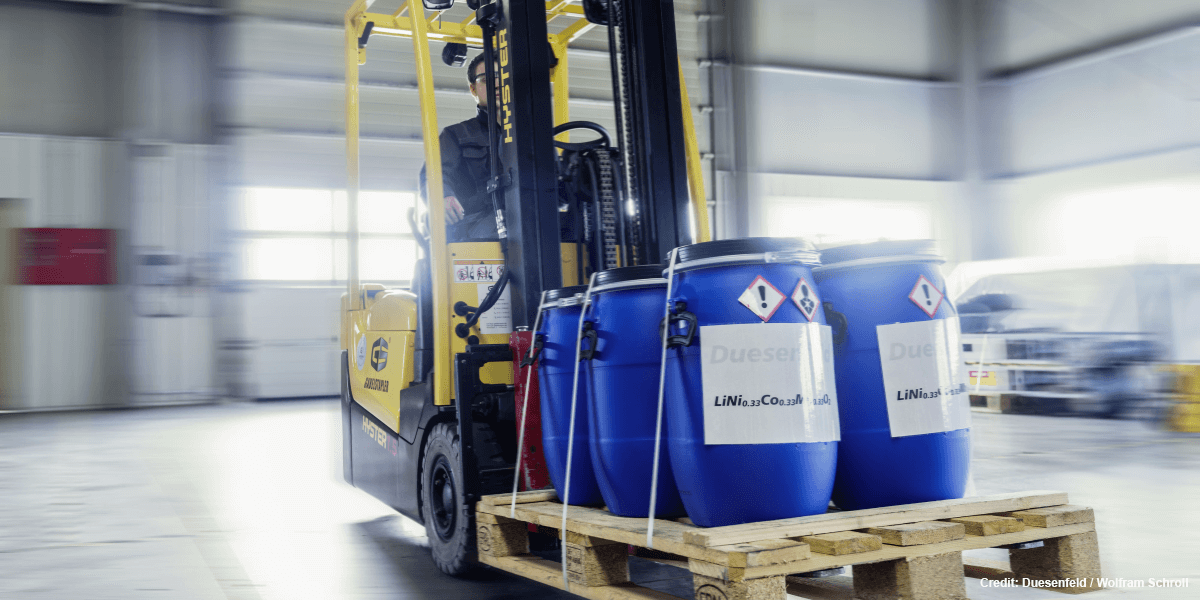
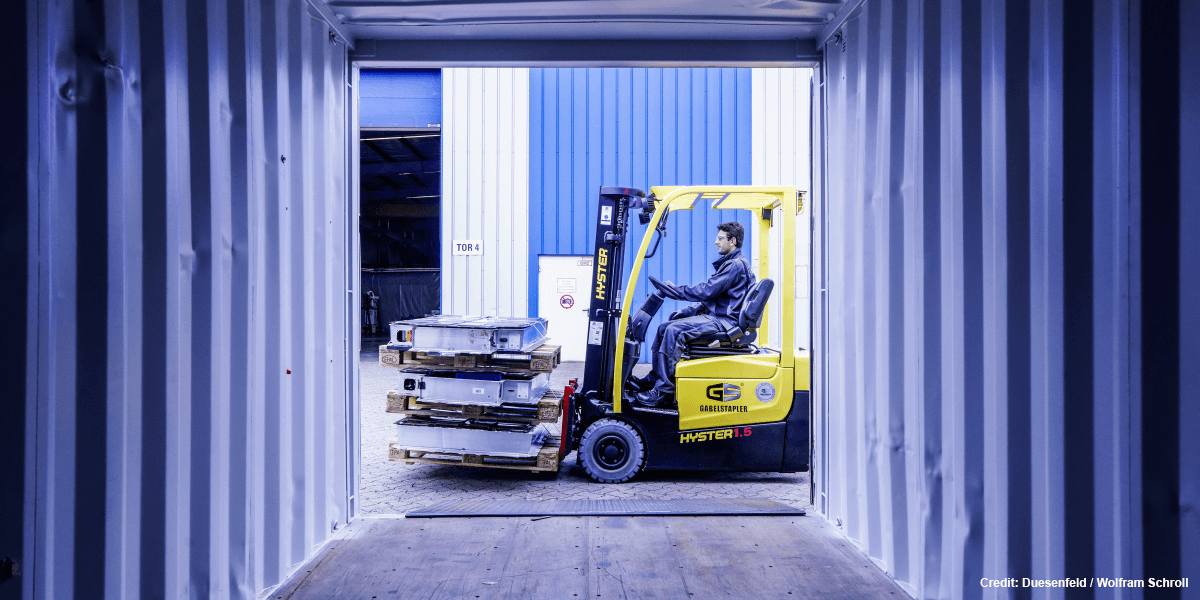
Die Überreste des Batteriemoduls und der Zellen sind jetzt getrocknet und damit unkritisch. Die verbliebene Mischung kann nun durch bewährte Prozesse, also zum Beispiel mit Magneten oder durch Luft, getrennt werden. Die Schnipsel der Separatorfolie, die Eisenmetalle, die Nichteisenmetalle wie Aluminium sowie ein Pulver aus Lithium und den Kathodenresten mit Nickel, Mangan und Kobalt bleiben übrig. Dieses schwarze Pulver könne, so Christian Hanisch von Duesenfeld, bald „durch ein hydrometallurgisches Verfahren in Lithiumcarbonat sowie Sulfate von Nickel, Mangan und Kobalt“ aufbereitet werden. Der größte Anteil der ursprünglichen Batterie kann also weitergenutzt werden. Wer aus der Autoindustrie alles bei dem Unternehmen nachgefragt hat, um testweise zehn Tonnen Batterie zerlegen zu lassen und später die Auswertung vorgelegt zu bekommen, verrät man bei Duesenfeld nicht. Man lässt aber durchblicken, dass es internationale und große Namen sind.
Gesetzliche Recyclingquote sollte drastisch erhöht werden
Es gehört zur enttäuschenden Lebenswirklichkeit, dass sich das Recycling trotz steigender Ressourcenpreise noch nicht lohnt. Es ist weiterhin billiger, Lithium oder Kobalt neu zu fördern. Weil die Nachfrage aber radikal ansteigen wird und die Herkunftsländer ihre Marktmacht zunehmend nutzen, sollten die EU die Mindestrecyclingquote von nur 50 Gewichtsprozent drastisch erhöhen. Im Reich der Mitte ist man hier schon einen Schritt weiter: China will Hersteller von elektrifizierten Fahrzeugen bei der Rücknahme und dem Recycling gebrauchter Batterien in die Pflicht nehmen. Im Sommer 2018 hatte China zudem 17 Städte und Regionen ausgewählt, um ein Pilotprogramm zum Recycling gebrauchter Elektrofahrzeug-Batterien zu starten. Mit BMW, Northvolt und Umicore wurde in Europa zumindest bereits ein erstes Technologiekonsortium zur gemeinsamen Entwicklung einer kompletten Wertschöpfungskette für E-Auto-Batteriezellen gegründet. Und auch Audi und Umicore entwickeln einen geschlossenen Kreislauf für das Recycling von Hochvoltbatterien aus Elektroautos.
Fazit
Der hohe Ressourceneinsatz bei Traktionsbatterien ist als Problem längst erkannt. Ein Weg zur Verbesserung ist die ständige Fortentwicklung der Zellchemie und der Batteriesysteme hin zu immer höherer volumetrischer und gravimetrischer Energiedichte. Das geschieht wegen der hohen Rohstoffkosten quasi automatisch. Gleichzeitig muss ein im industriellen Maßstab funktionierendes Recyclingnetzwerk errichtet werden. Der gesetzliche Rahmen dazu sollte verschärft werden – das schont nicht nur die Umwelt, es entlastet letztlich auch die Autoindustrie und die Besitzer.
13 Kommentare