Volkswagen Group Components nimmt Pilot-Recyclinganlage in Betrieb
In Salzgitter hat die VW-Sparte Group Components eine Pilot-Anlage zum Recycling von Batterien in Betrieb genommen. Mit der Anlage, die auf höhere Kapazitäten skalierbar sein soll, will Volkswagen wertvolle Rohstoffe zurückgewinnen und in neuen Batterien verbauen.
Wie VWGC mitteilt, realisiere der Konzern mit dem Start des Pilotbetriebs „einen weiteren konsequenten Schritt der nachhaltigen End-to-End-Verantwortung für die gesamte Wertschöpfungskette der E- Fahrzeug-Batterie“. Trotz derartiger PR-Sätze wird der Konzern auch konkret: Wertvolle Rohstoffe wie Lithium, Nickel, Mangan und Kobalt sollen in einem geschlossenen Kreislauf mit einer „wiederverwertungs-Quote von perspektivisch mehr als 90 Prozent“ wieder gewonnen werden. Zudem sollen auch Aluminium, Kupfer und Kunststoffe recycelt werden.
Die Pilotanlage ist laut VW derzeit auf eine Kapazität von 3.600 Batteriesystemen pro Jahr (oder rund 1.500 Tonnen) ausgelegt, weil es einfach noch nicht genügend recyclingwürdige Batterien gibt. Dort sollen nur Batterien recycelt werden, die nicht mehr für Second-Life-Anwendungen geeignet sind – VWGC nennt hier etwa seine flexiblen Schnellladesäulen oder mobilen Laderoboter. „Größere Mengen Batterie-Rückläufer werden frühestens Ende der 2020er Jahre erwartet“, so Volkswagen in der Mitteilung. Daher soll die Anlage „bei permanent weiter optimierten Verfahren auf größere Mengen skaliert werden“.
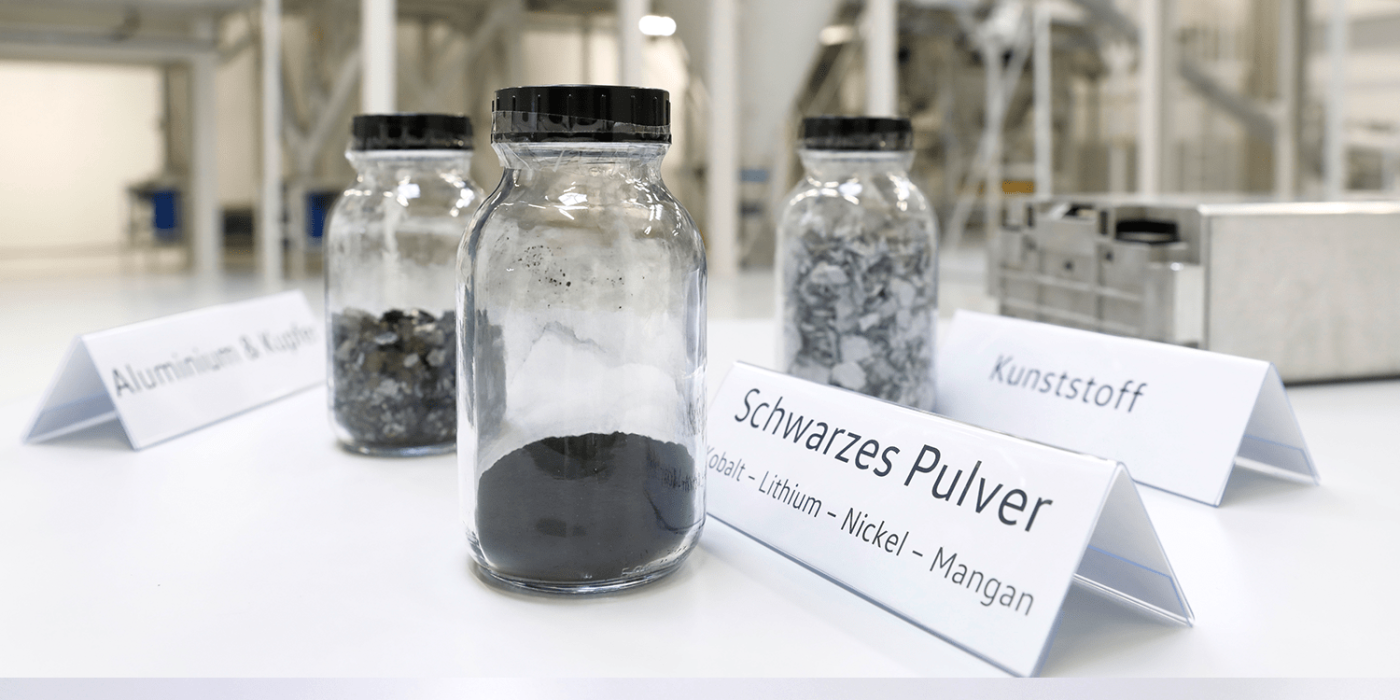

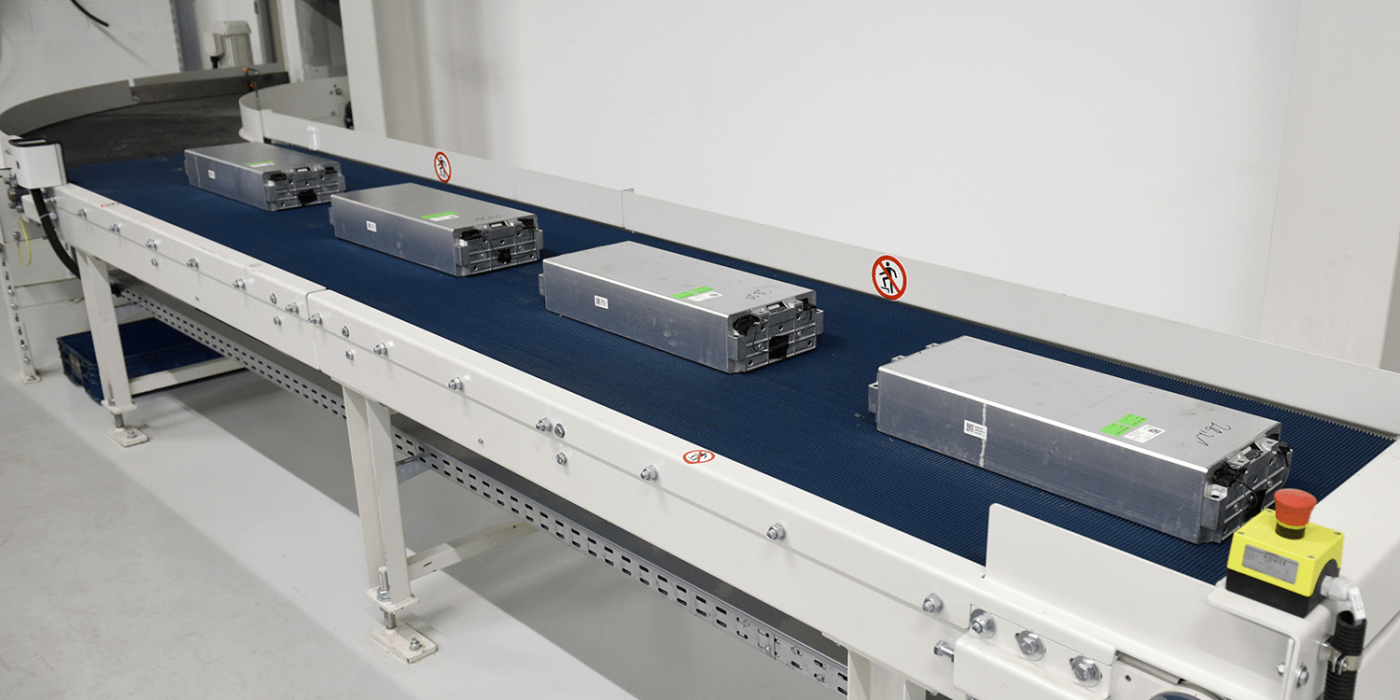
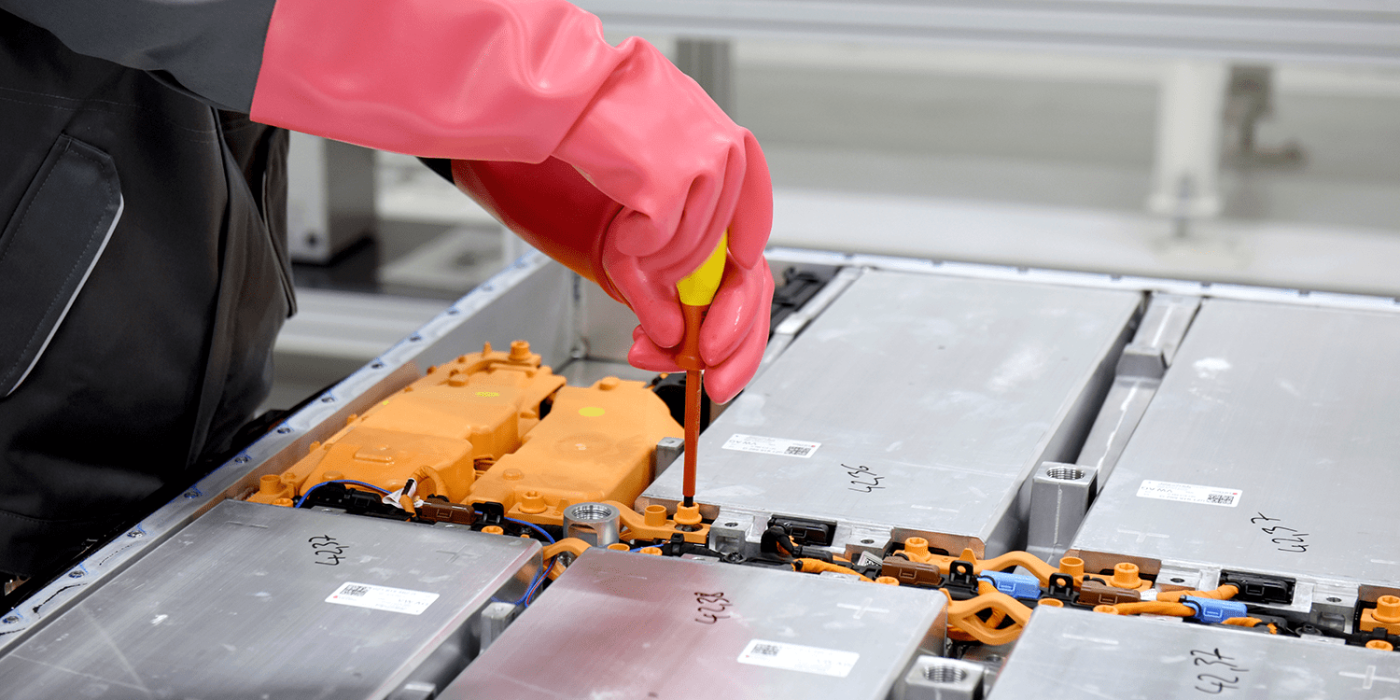
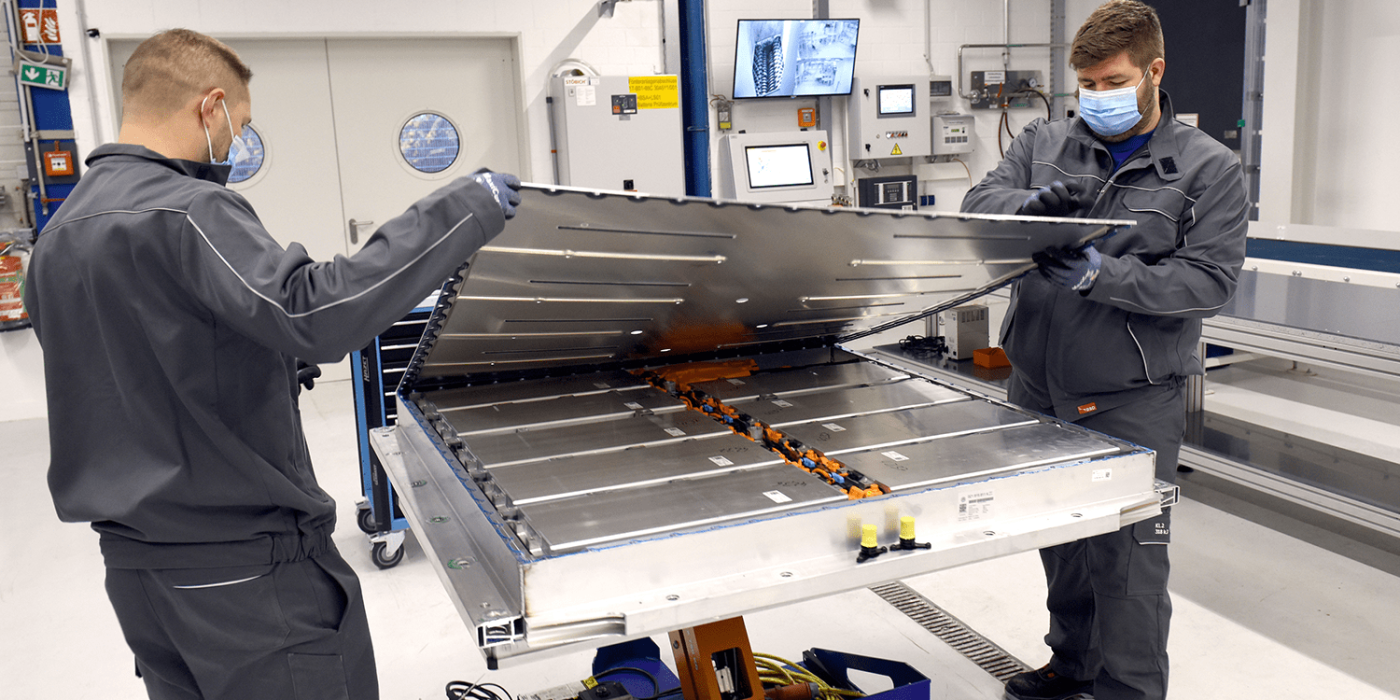
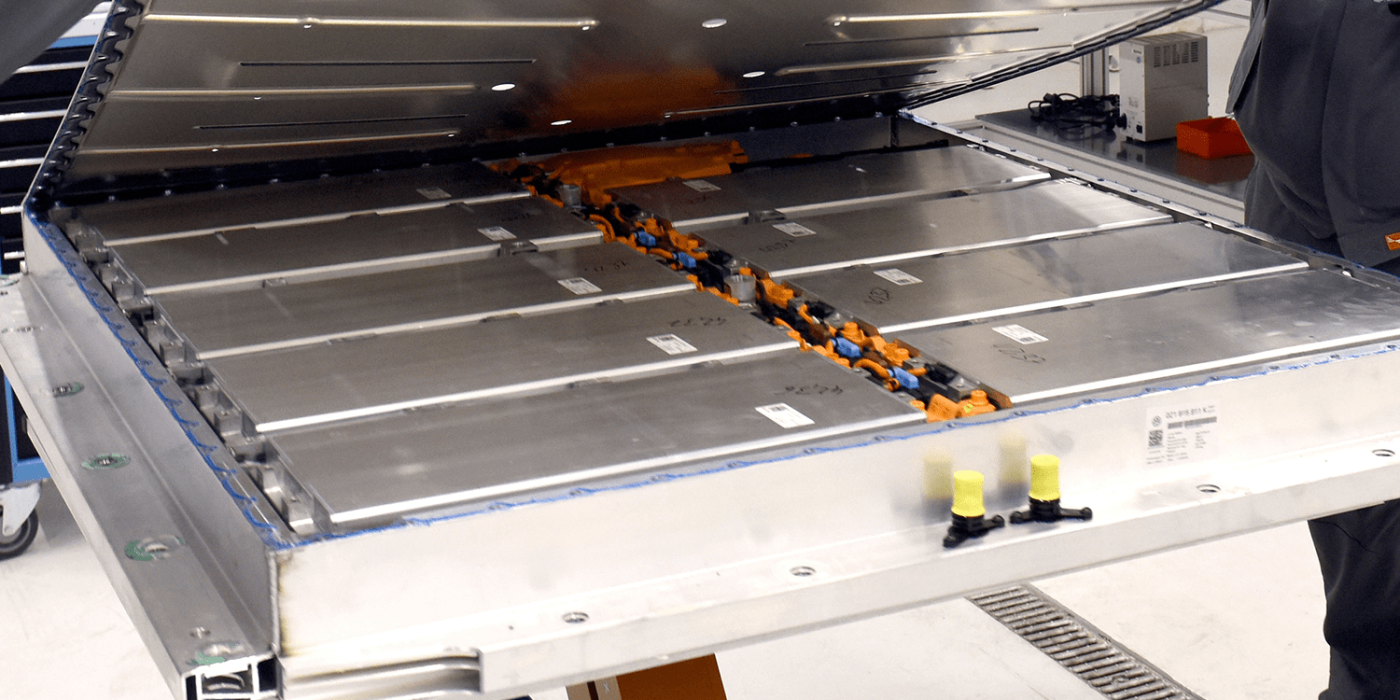
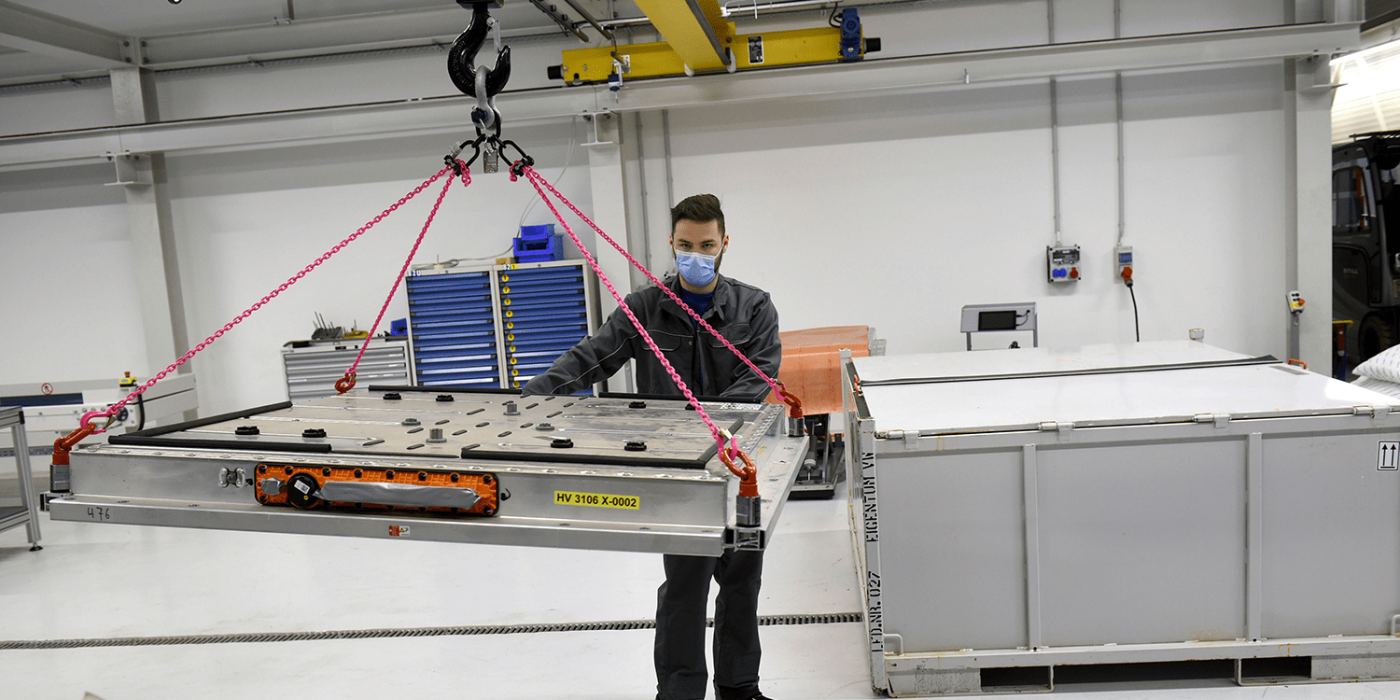
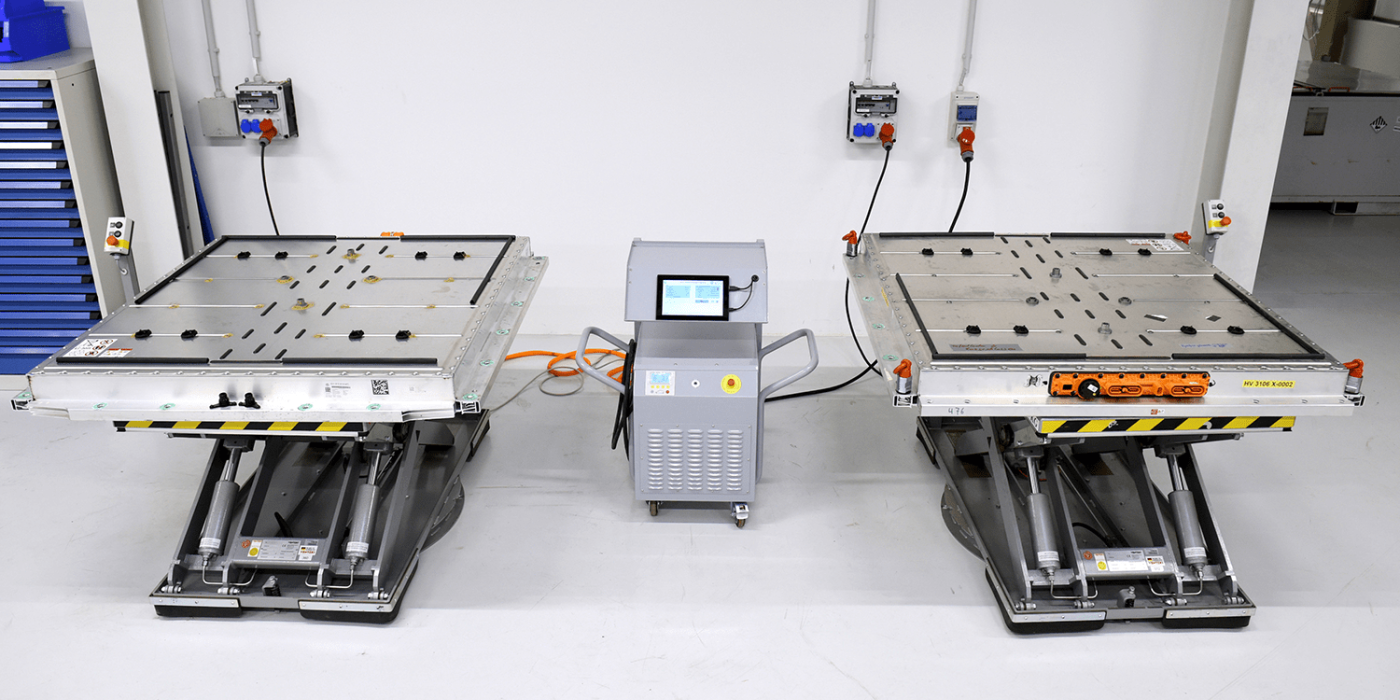
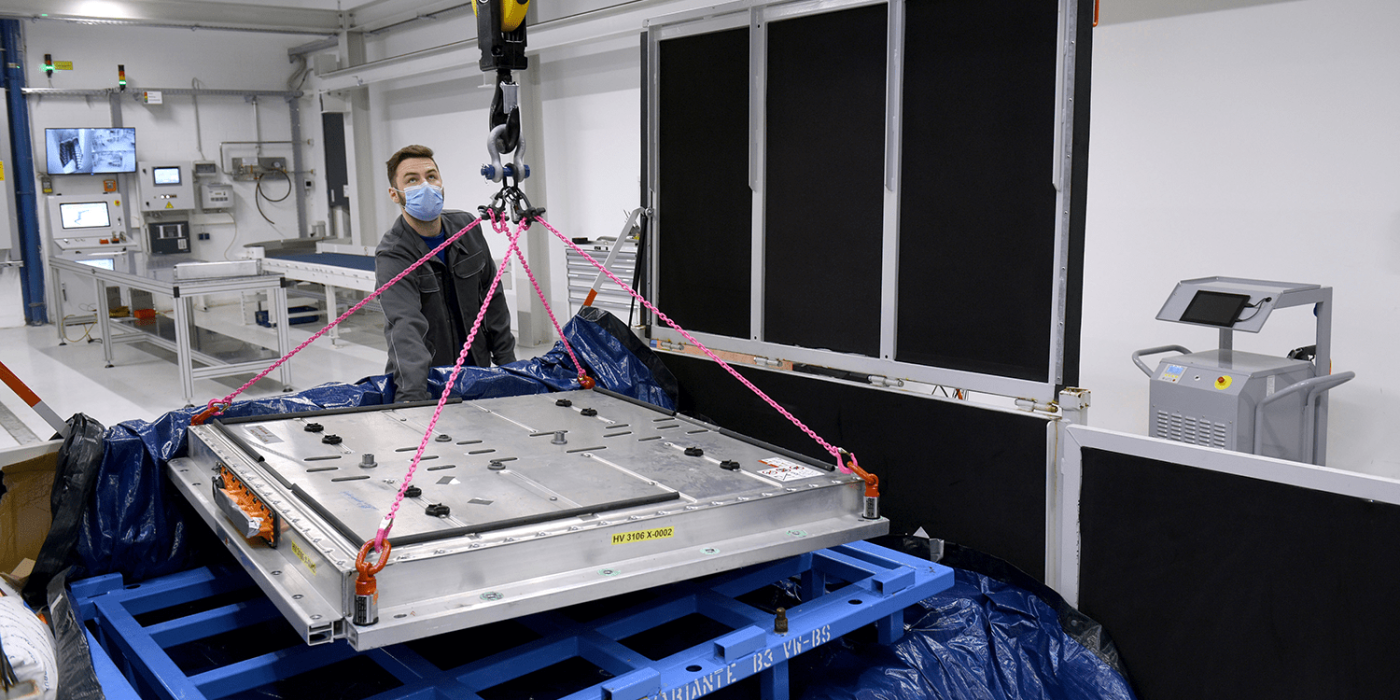
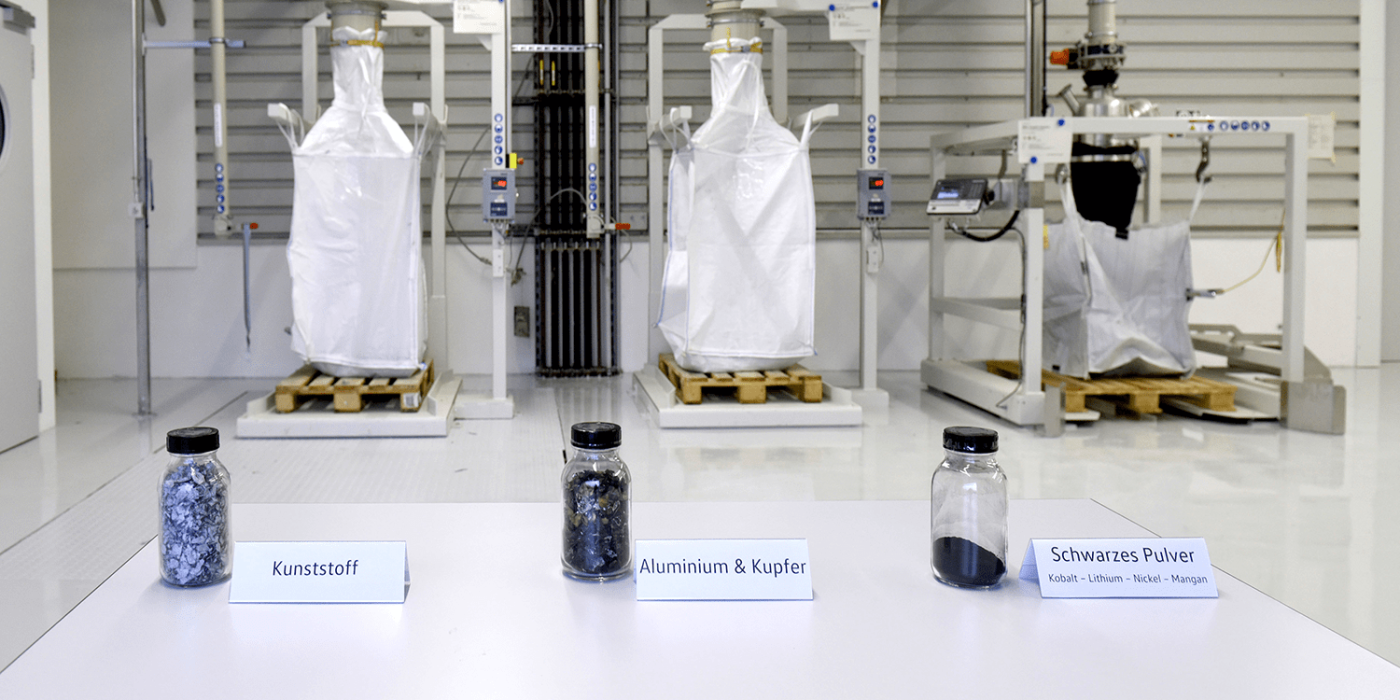
„Es wird sich erst mittelfristig oder langfristig ergeben, dass wir die Materialen wieder in die Fertigung neuer Produkte einschleusen“, sagt Thomas Schmall, Mitglied des Konzernvorstands und Chef der VWGC, bei einer Online-Veranstaltung zur Eröffnung der Pilotanlage. „Dennoch ist es wichtig, dass wir früh in diese Themen einsteigen. Hätten wir nicht vor zehn Jahren in die Produktion von Elektromaschinen in Kassel investiert, könnten wir heute nicht in diesem Umfang und der Qualität E-Motoren für den MEB bauen.“
Die Batterien, die zum Start der rund sechs Millionen Euro teuren Anlage recycelt werden sollen, stammen aus dem Konzern selbst. „Wir sprechen seit anderthalb Jahren mit allen Konzernmarken und haben die Batterien aus ihren Erprobungs- und Vorserienfahrzeugen eingesammelt und gelagert“, so Schmall. „Zudem verwerten wir Prototypen-Zellen aus unserer Pilot-Zellproduktion in Salzgitter. Damit können wir die Anlage in diesem Jahr gut auslasten.“
VWGC deckt dabei am Standort Salzgitter nicht alle Schritte selbst ab, einige Verfahren werden bei Partnerunternehmen durchgeführt. Nach der Eingangsprüfung zur Second-Life-Nutzung werden die Batterien tiefenentladen und demontiert. Im Anschluss werden die Einzelteile zu einem Granulat zerrieben und nicht energieintensiv eingeschmolzen. Aus dem getrockneten Granulat (um den Elektrolyt zurückzugewinnen) können dann Aluminium, Kupfer, Kunststoffe und das „Schwarze Pulver“ gewonnen werden. Dieses Pulver enthält unter anderem das Lithium, Nickel, Mangan und Kobalt sowie Graphit.
Das „Schwarze Pulver“ wird dann bei „spezialisierten Partnern“ in einem sogenannten hydrometallurgischen Verfahren – also mit Einsatz von Wasser und Chemikalien – bearbeitet, um die einzelnen Rohstoffe aufzubereiten.
Neun Kilo Kobalt, acht Kilo Lithium
Mit den bisherigen pyrometallischen Verfahren, bei dem die Batteriematerialien eingeschmolzen wurden, konnten bisher nur rund 50 Prozent der Materialien zurück gewonnen werden – der Fokus lag hier bei Nickel und Kobalt.
Die Liste an Materialien, die bei dem hydrometallurgischen Verfahren zurückgewonnen werden könne, ist ungleich länger. Bei der Präsentation nennt VW auch die einzelnen Mengen der eingesetzten Materialien. In der 62-kWh-Batterie des MEB (Gesamtgewicht 400 Kilogramm) sind rund 126 Kilo Aluminium (vor allem im Gehäuse), 71 Kilo Graphit und 22 Kilogramm Kupfer enthalten. Die verbauten Gewichte der wichtigen Kathodenmaterialen geben die Wolfsburger mit 12 Kilogramm Mangan, 9 Kilogramm Kobalt und 8 Kilogramm Lithium an.
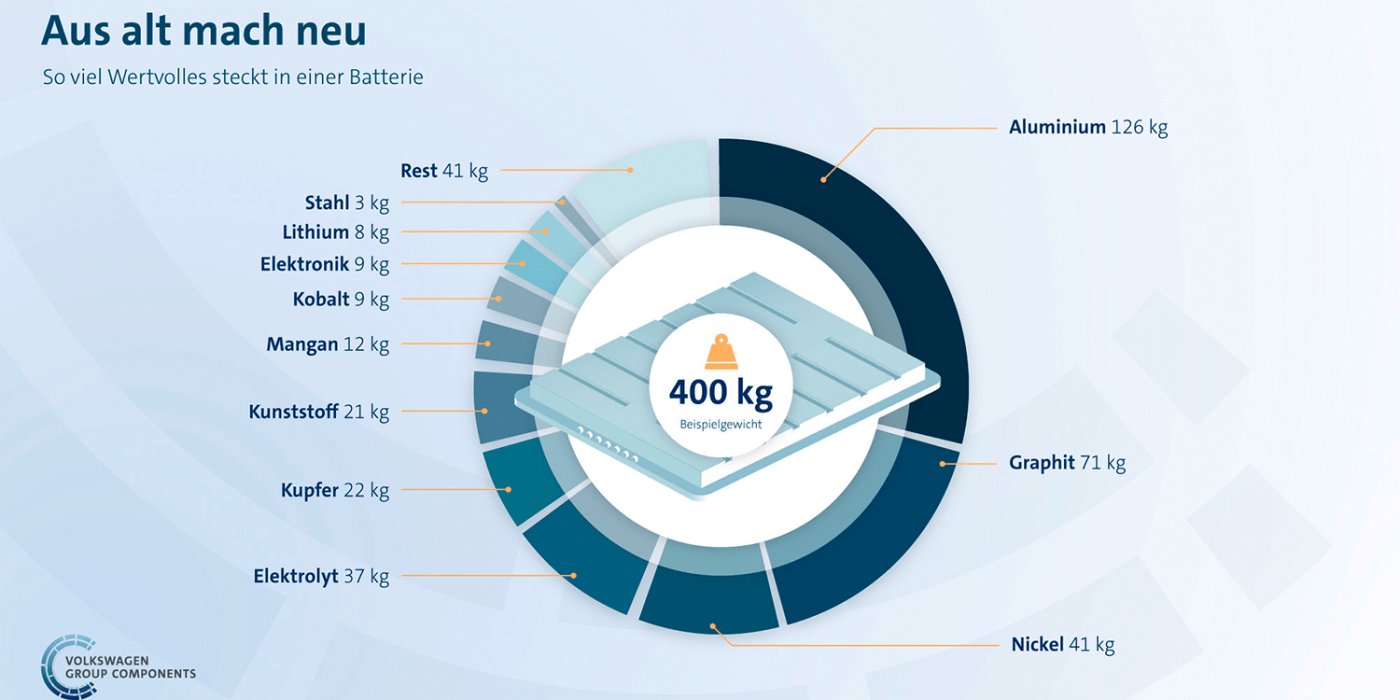
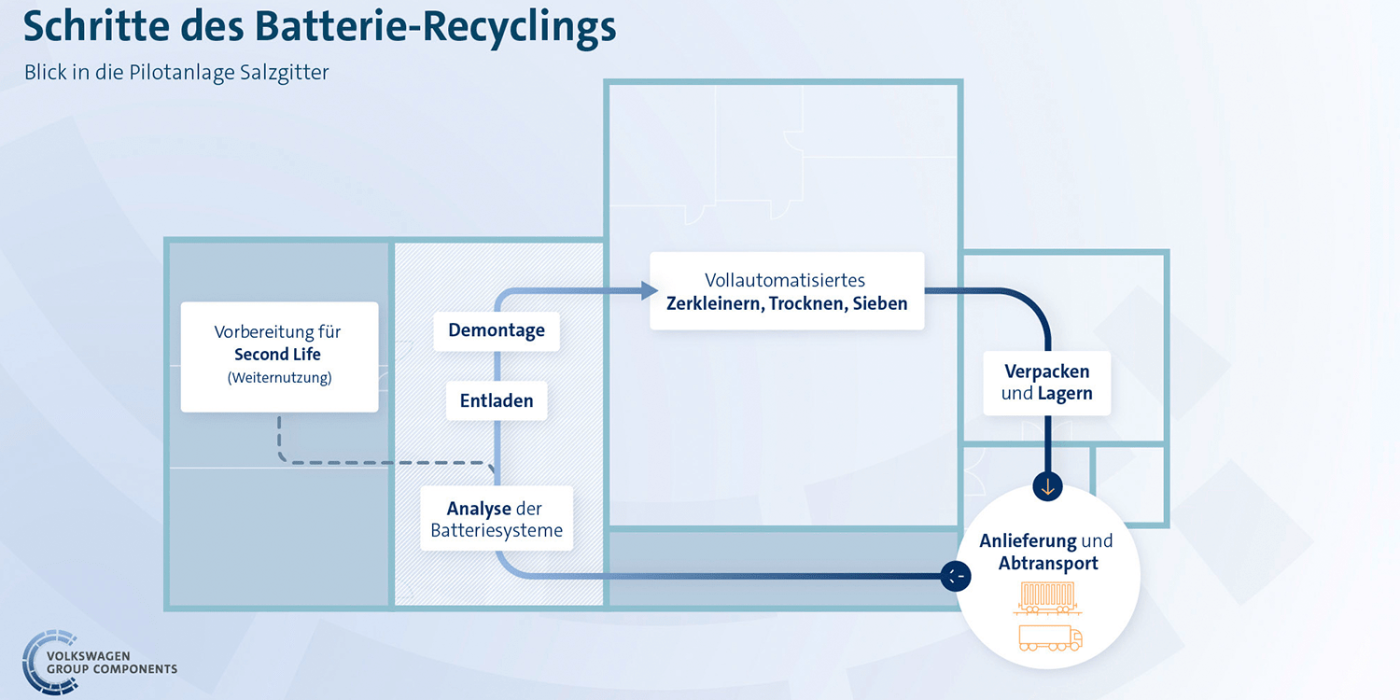
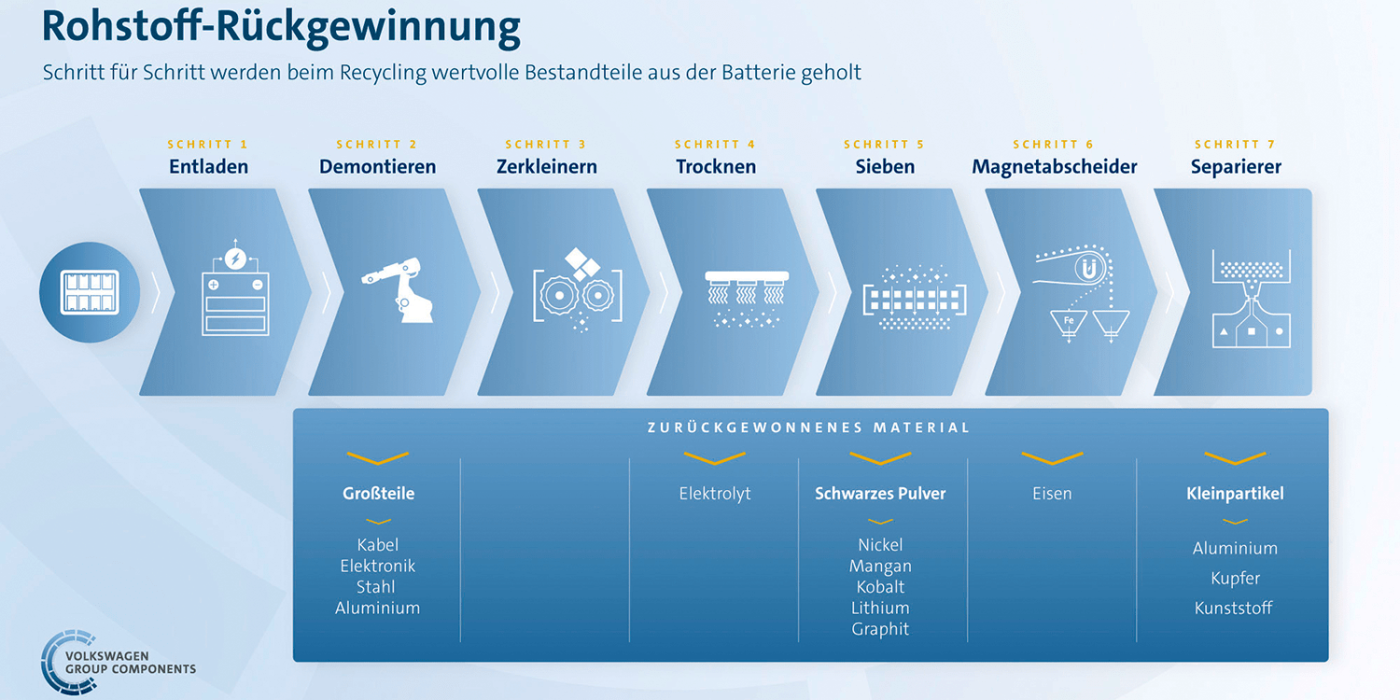
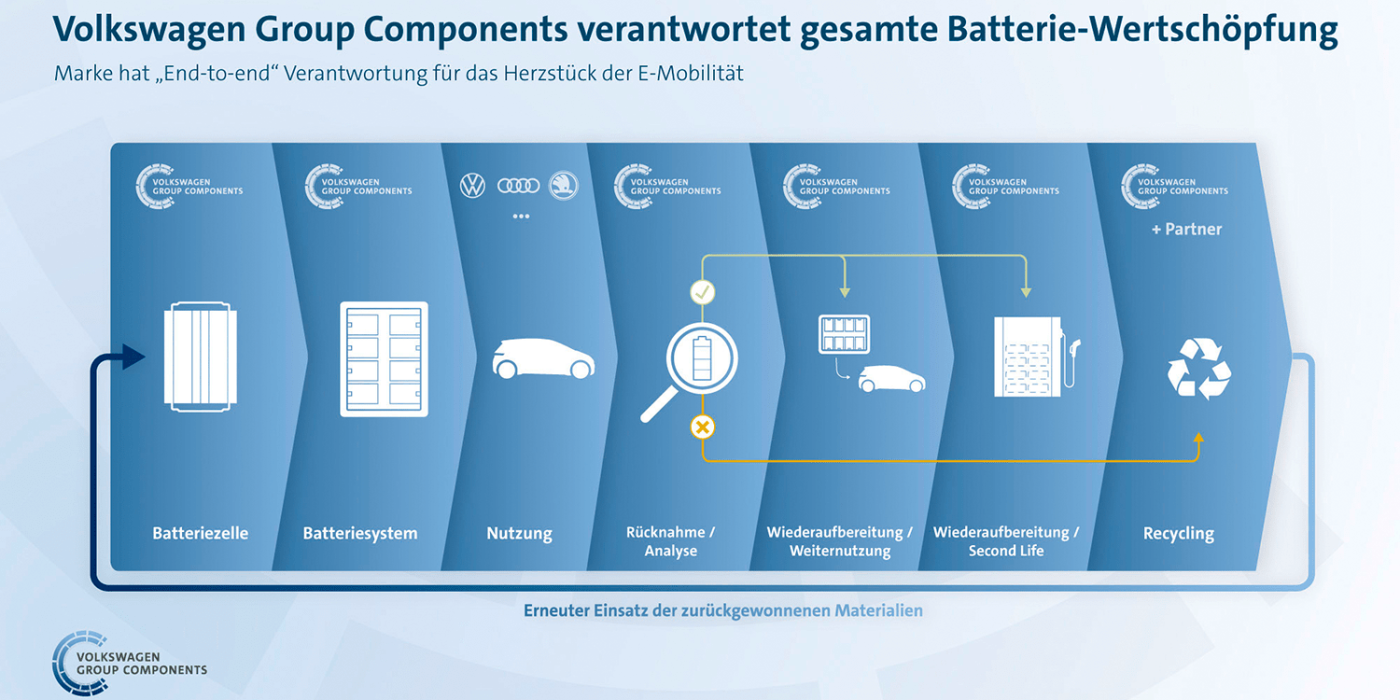
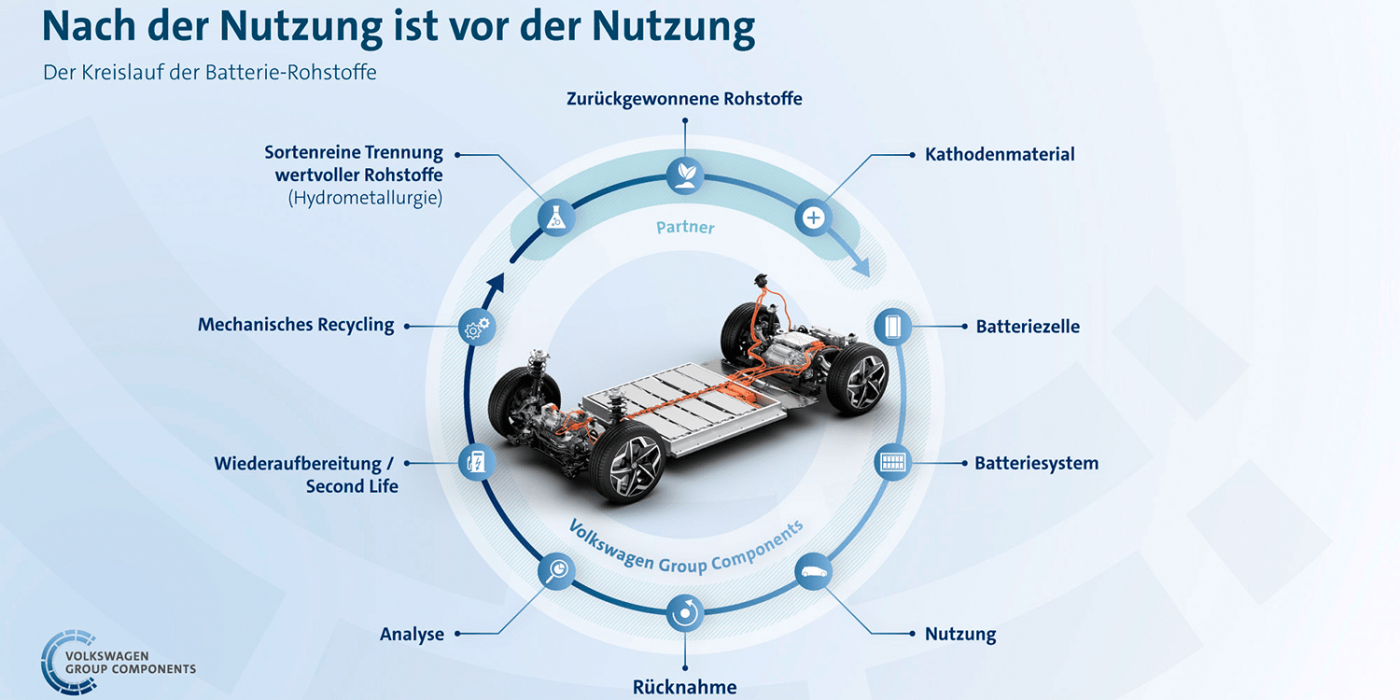
„Wesentliche Bestandteile alter Batteriezellen können so bei der Herstellung von neuem Kathodenmaterial genutzt werden“, sagt Mark Möller, Leiter Geschäftsbereich Technische Entwicklung & E-Mobilität: „Wir wissen aus der Forschung, dass recycelte Batterie-Rohstoffe genauso leistungsfähig sind wie neue. Mit dem zurückgewonnenen Material können wir perspektivisch die Versorgung unserer Zellfertigung unterstützen. Da die Nachfrage nach Batterien und damit nach E-Rohstoffen stark steigen wird, können wir jedes Gramm zurückgewonnenes Material gut gebrauchen.“
1,3 Tonnen weniger CO2 mit Recycling-Material
Aber noch nicht alle Materialien können direkt in neue Batterien verbaut werden. Das gewonnene Graphit habe nicht die Qualität, die für neue Batterien benötigt werde, so VW. Und Komponenten wie das getrocknete Elektrolyt können nicht wieder als Elektrolyt verwendet werden, aber für andere Einsätze in der Chemie-Industrie.
Bei einer Batterie mit 62 kWh (im ID.3 mit ihrem Netto-Wert 58 kWh vermarktet) gibt Volkswagen Group Components die CO2-Einsparung mit rund 1,3 Tonnen an, wenn die Kathoden aus recyceltem Material und mit Grünstrom hergestellt werden.
Neben der eigenen Anlage prüfe man auch die Zusammenarbeit mit anderen Recycling-Unternehmen, so Möller. „Wir haben nicht vor, jede einzelne Batterie der Welt selbst zu recyceln. Wichtig ist aber, dass Partner ähnliche Verfahren verfolgen wie wir.“
volkswagen-newsroom.com
0 Kommentare