Batterietechnologie für E-Fahrzeuge: Basis des Fortschritts
Die Entwicklung der Batterietechnologie hat den aktuellen E-Auto-Boom erst möglich gemacht. Die Weiterentwicklung läuft immer noch auf Hochtouren, zugleich wird im Eiltempo die Produktion ausgebaut. Doch wohin führen Skalierung, Markt und Technologie? Bei der 14. Ausgabe unserer Online-Konferenz „electrive.net LIVE“ haben wir vor über 400 digitalen Gästen über die Batterien der Zukunft und ihre Produktion diskutiert. Hier ist der Konferenzbericht.
* * *
Besser. Billiger. Und in Massen. Kein Bauteil ist fürs Elektroauto so elementar wie die Traktionsbatterie. Überall auf der Welt werden zurzeit Fabriken errichtet. Eine neue Wertschöpfungskette von der Förderung der Rohmaterialien über die Zellproduktion und dem Second Use bis zum Recycling entsteht.
Wir haben auf der 14. Konferenz „electrive.net LIVE“ mit sechs hochkarätigen Fachleuten aus Wirtschaft und Forschung diskutiert, um zu erfahren, welche neuen Lösungen es für den radikalen Hochlauf gibt und natürlich wie die Batteriezelle der (nahen) Zukunft aussieht.
Der internationale Markt, der hier wächst, ist gigantisch. Zugleich gibt es eine hohe Dynamik, deren Treiber oft der Zwang zur Kostenreduktion bei zeitgleich wachsender Leistungsfähigkeit der Batterie ist. Es bleibt im Wortsinn spannend.
Webasto Battery Systems
Webasto, ursprünglich bekannt für Autodächer und Standheizungen, produziert in der Sparte Battery Systems wie es der englische Name sagt Batteriesysteme. Noch entfallen lediglich zwei Prozent des Umsatzes auf diesen Bereich – Tendenz stark steigend. Robert Gantner von Webasto erklärt den Weg von der Blaupause zum Hochskalieren der Produktion: „Wir machen für unsere Kunden alles außer der Zelle“, so Gantner.
Die Kunden aus der Industrie wollten zuerst die üblichen Rahmendaten wie die Kosten des Batteriesystems in Euro pro Kilowattstunde, die gravimetrische und die volumetrische Energiedichte und andere Parameter definieren. Zugleich ist die Sicherheit ein wichtiger Aspekt. Wegen des hohen Zeitdrucks im Markt wäre aber die Geschwindigkeit bei der Umsetzung eine wesentliche Anforderung, so Gantner. Time to market, das ist das Ziel.
Am Standort in Schierling werden zurzeit rund 20.000 Systeme pro Jahr gefertigt. Auf einer Linie entstehen zwei unterschiedliche Systeme („Multi-Product Line“). Ungleich größer ist ein Werk in Südkorea, das in der ersten Phase 100.000 Batterien pro Jahr ausstoßen soll – alle drei Minuten eine. Mehr ist machbar. Im Februar 2022 geht es richtig los. „Alles was wir hier lernen, lassen wir selbstverständlich in kommende Werke auf anderen Kontinenten einfließen.“
Blackstone Technology GmbH
Holger Gritzka, nach Maßstäben der Elektromobilität fast ein Urgestein, berichtet als CEO von der Blackstone Technology GmbH aus Döbeln in Sachsen. Fokus der Arbeit ist der 3D-Druck von Elektroden: „Wir stellen Grundsätze der Batterieproduktion in Frage.“ Zukünftig, so Gritzka, könnten Batteriezellen wie Halbleiter gefertigt werden – im Druck. Ende des Jahres soll die Pilotfertigung beginnen.
Nicht nur NMC- und LFP-Zellen, sondern auch Solid State-Zellen könnten mit Hilfe des 3D-Druck Gestalt annehmen. Eine Stärke des Verfahrens ist die Flexibilität in der Anwendung. Ein weiteres Ziel ist wie die Kostensenkung. Die Druckmaschinen können darüber hinaus leicht hochskaliert und international aufgebaut werden.
„Unser Plan ist, auf Basis der Drucktechnologie Festkörperzellen zu bauen“, sagt Holger Gritzka. Eine Lizenzierung dieses Verfahrens sei vorgesehen. Die Motivation, so Gritzka, sei „allerhand Raum für Verbesserung“ bei heutigen Zellen. Dieses Potenzial wolle man über den 3D-Druck heben: Energiedichte erhöhen, Flexibilität beim Formfaktor erhöhen, Energieverbrauch senken. In der Folge sind auch die negativen Umweltauswirkungen geringer – und die Kosten.
Gritzka reklamiert zum Beispiel, dass ein Trockner für Lösungsmittel von 50 und mehr Metern auf 40 Zentimeter (!) schrumpfen könnte. Sogar der Flächenbedarf für eine Fabrik sinkt also. Ja, das ist nur ein plakatives Detail in der Kette, aber über den Gesamtprozess wird zum Beispiel der Energiebedarf um ein Viertel reduziert. Die Kosten für eine Zelle hätten das Potenzial, um 20 Euro pro Kilowattstunden gesenkt zu werden, so Blackstone-CEO Gritzka. Und bei allem haben Solid State-Batterien langfristig das mit Abstand größte Entwicklungspotenzial.
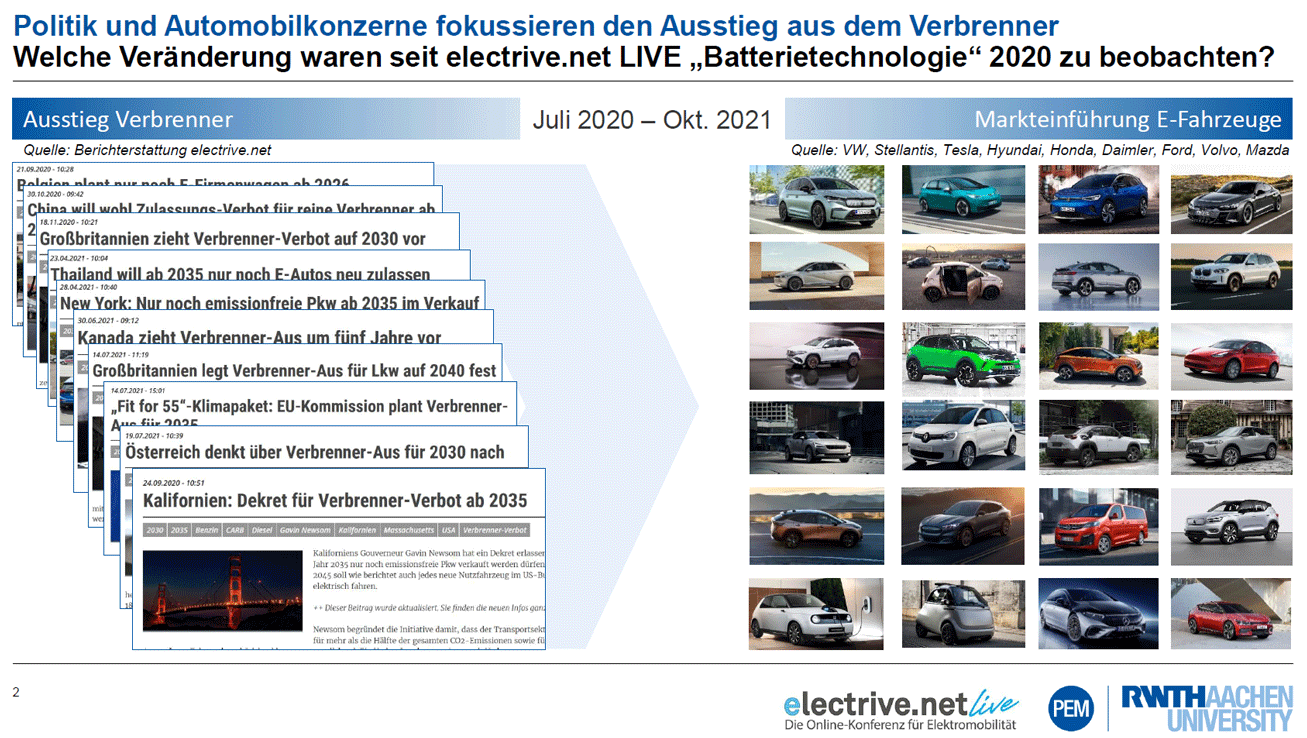
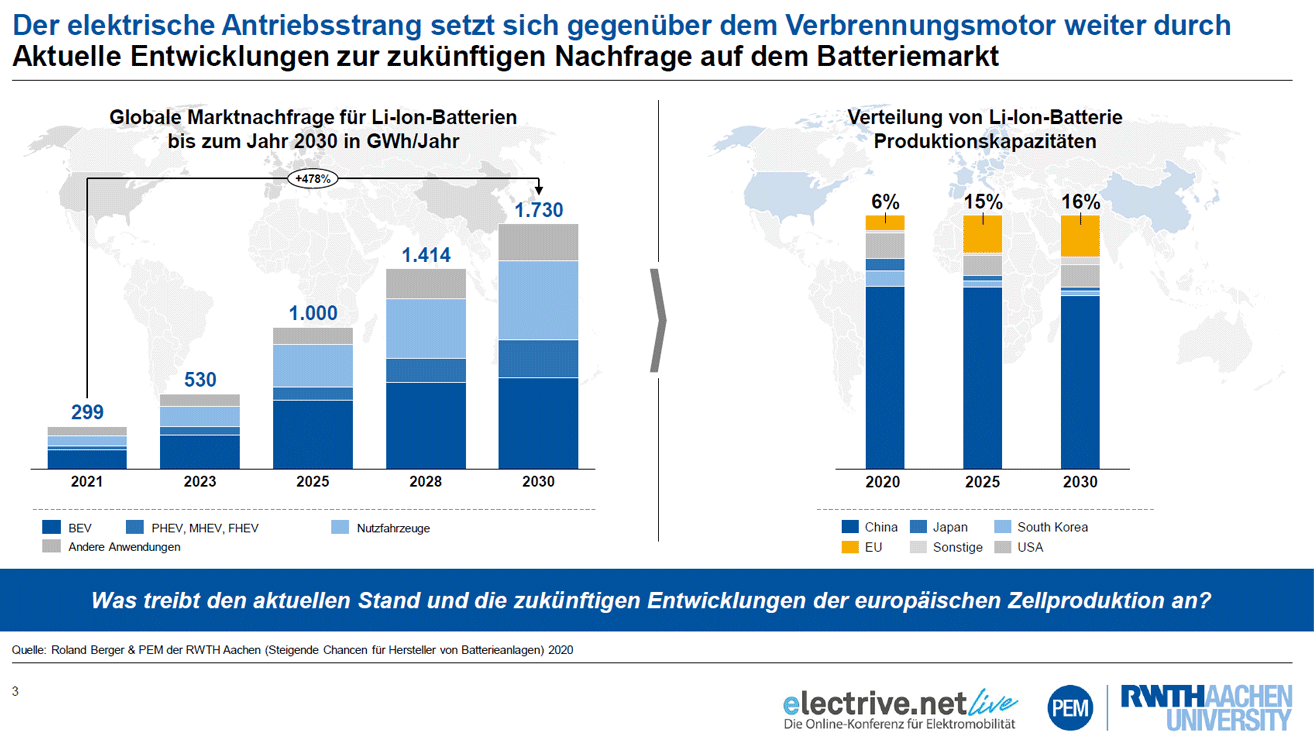
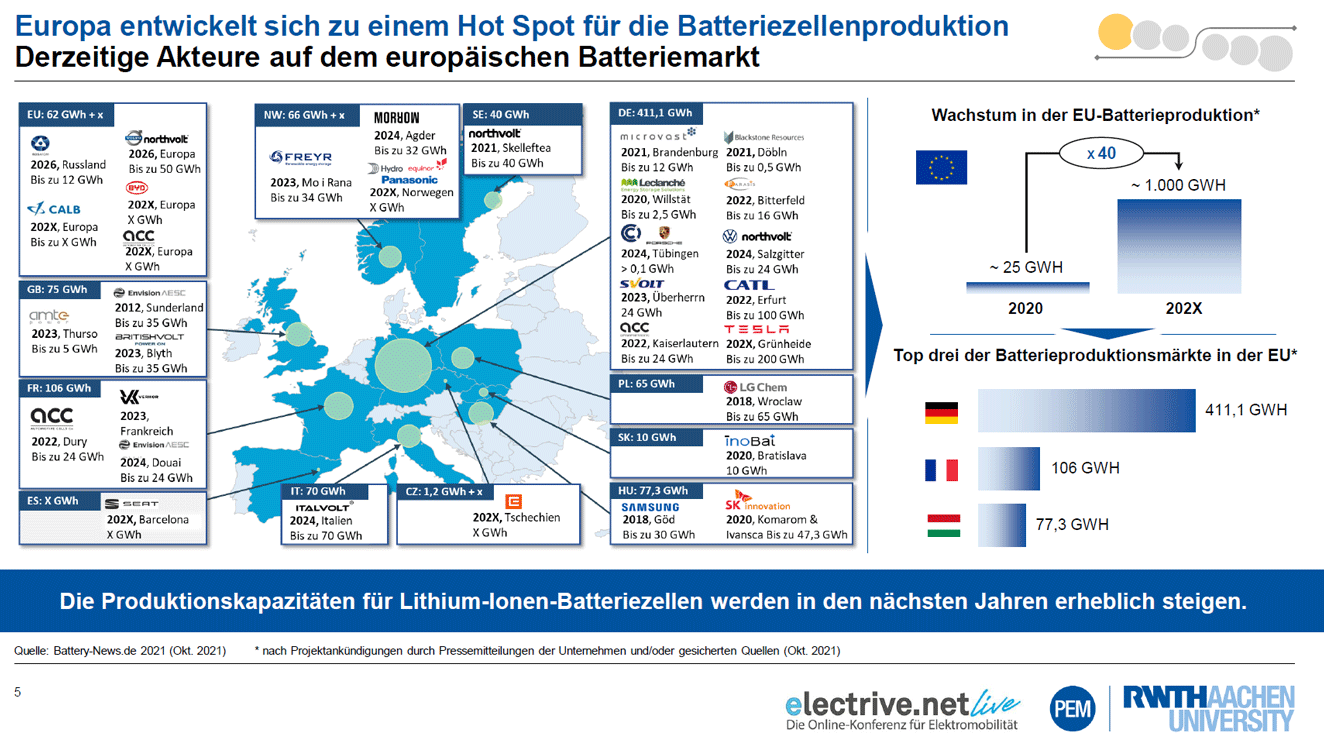
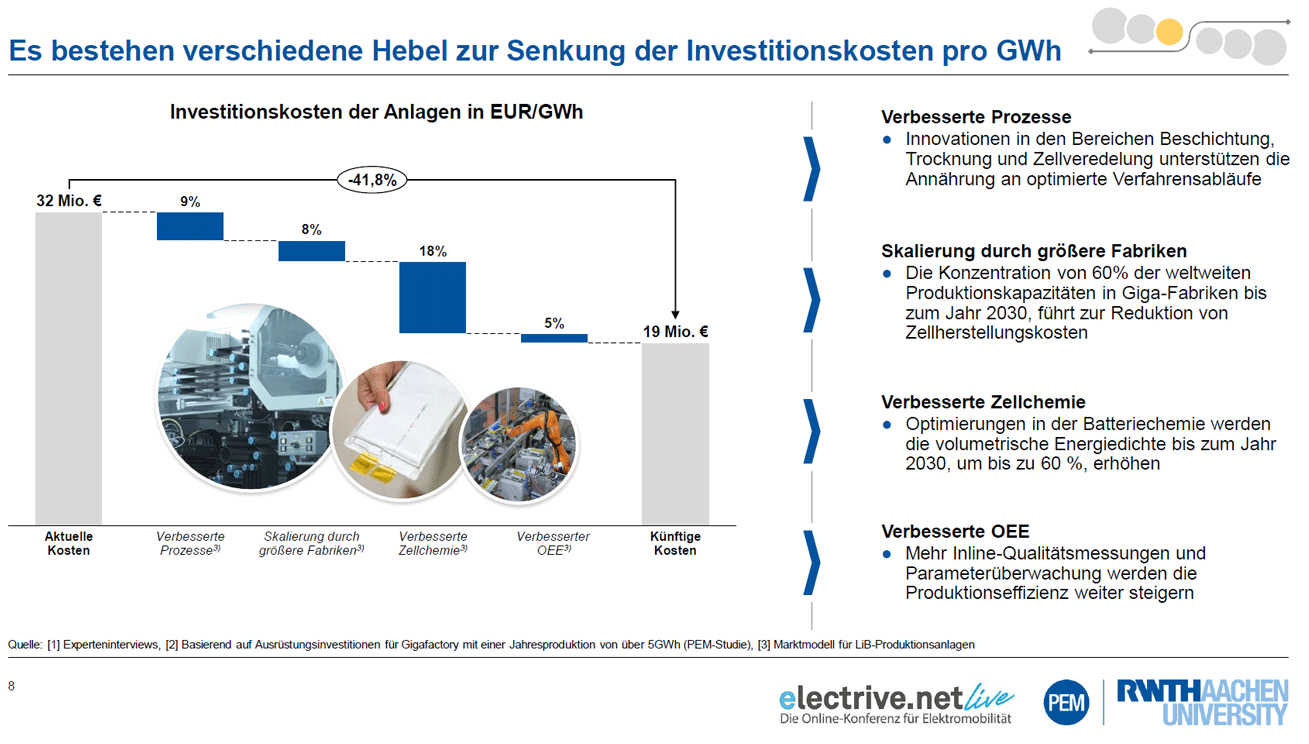
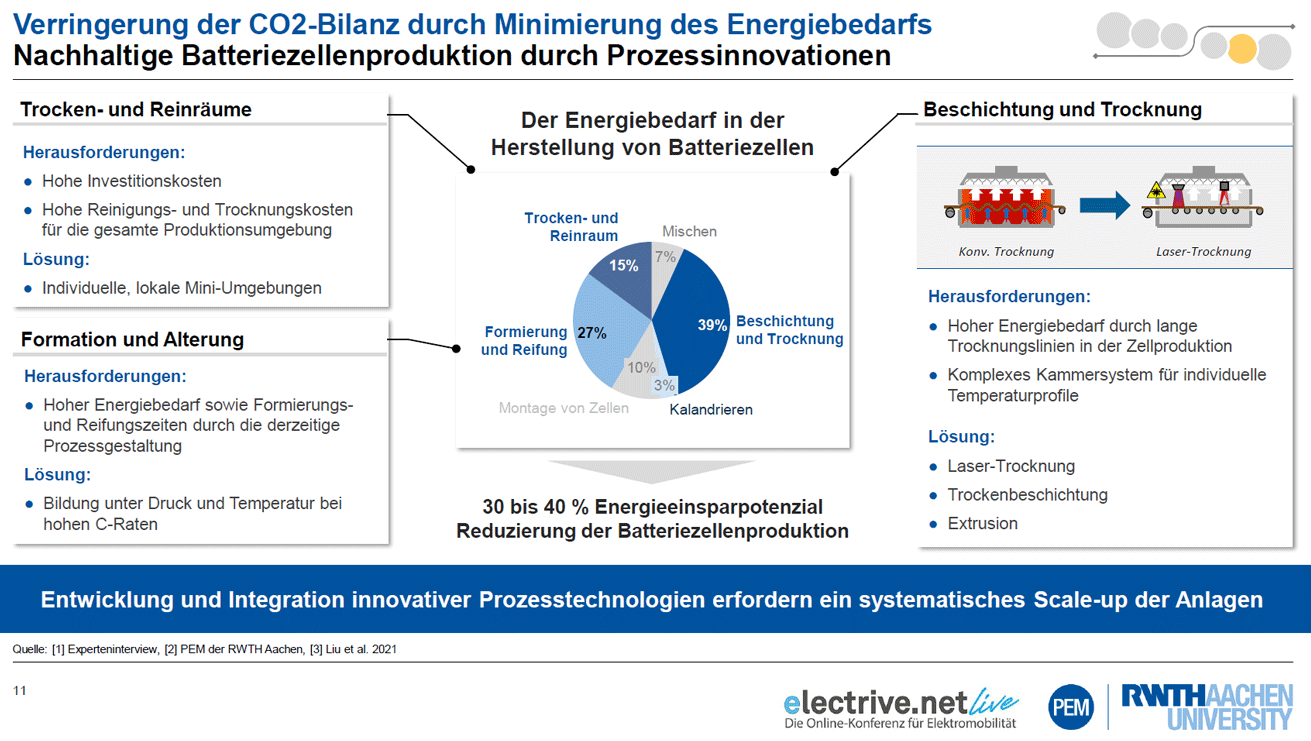
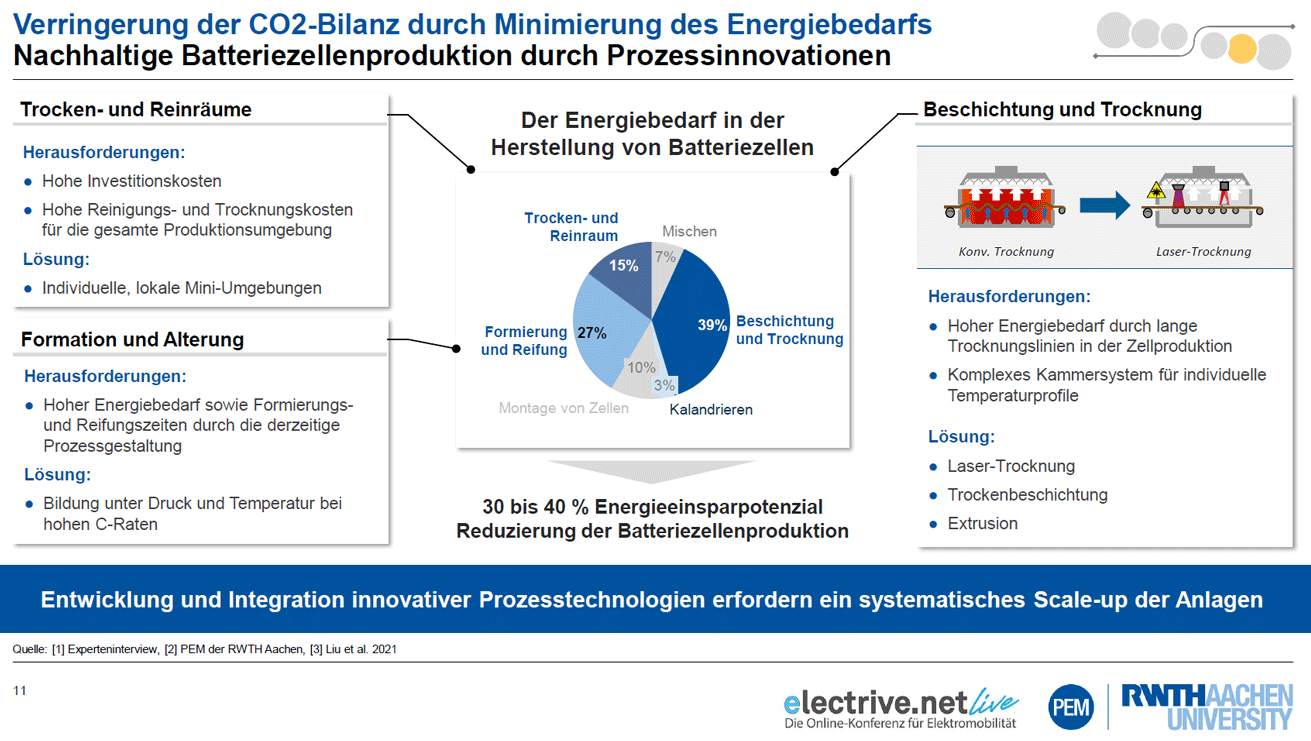
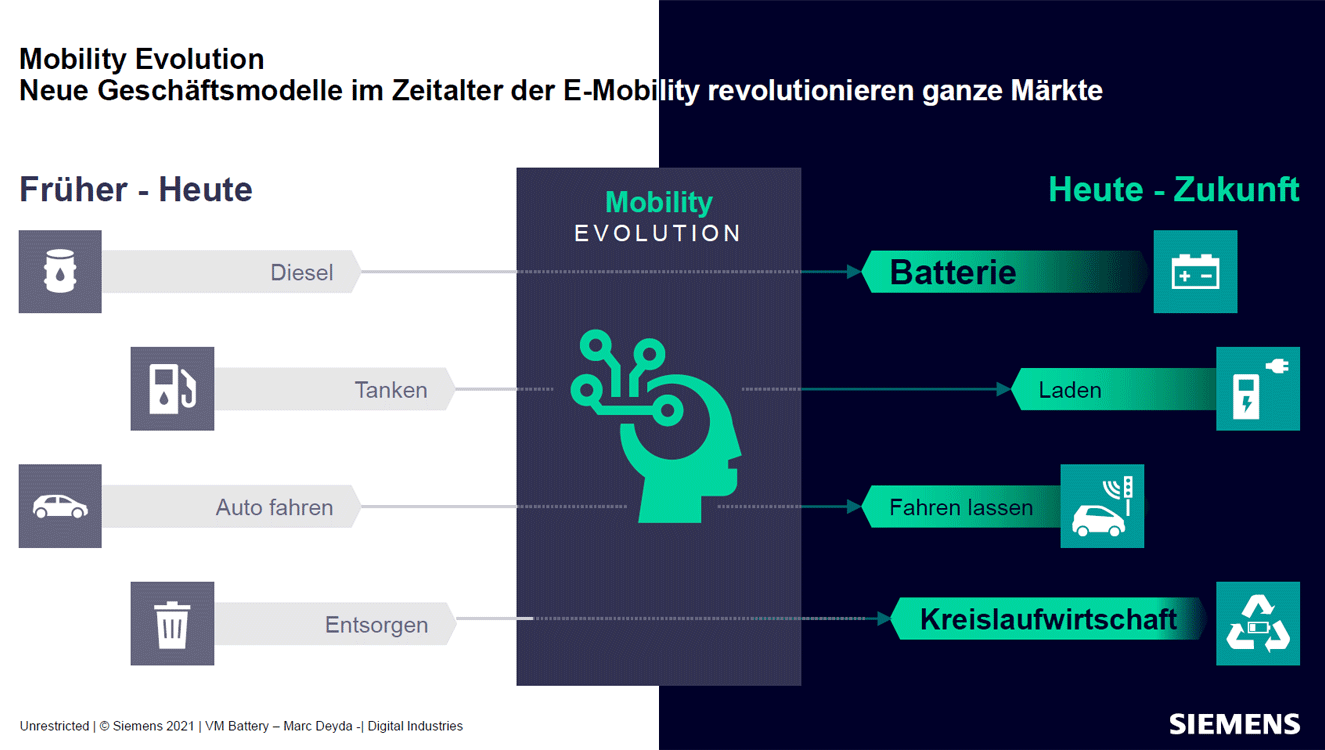
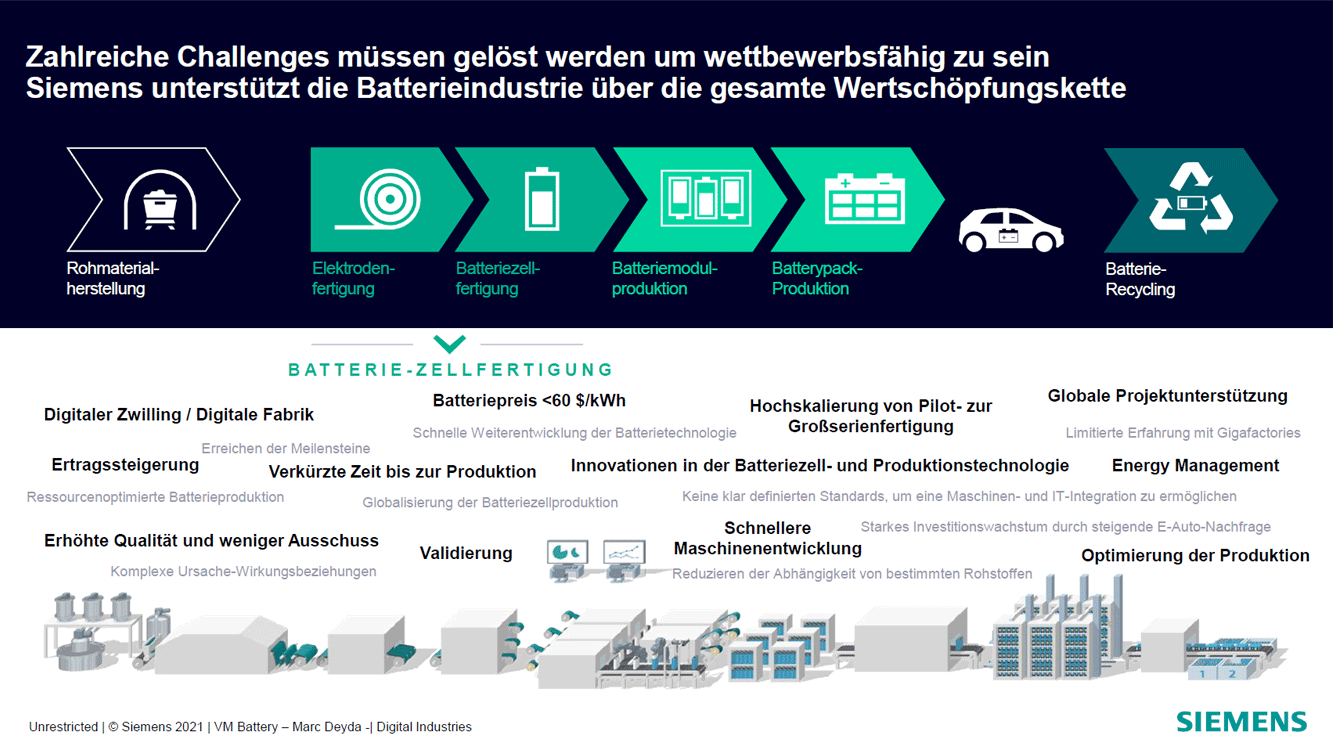
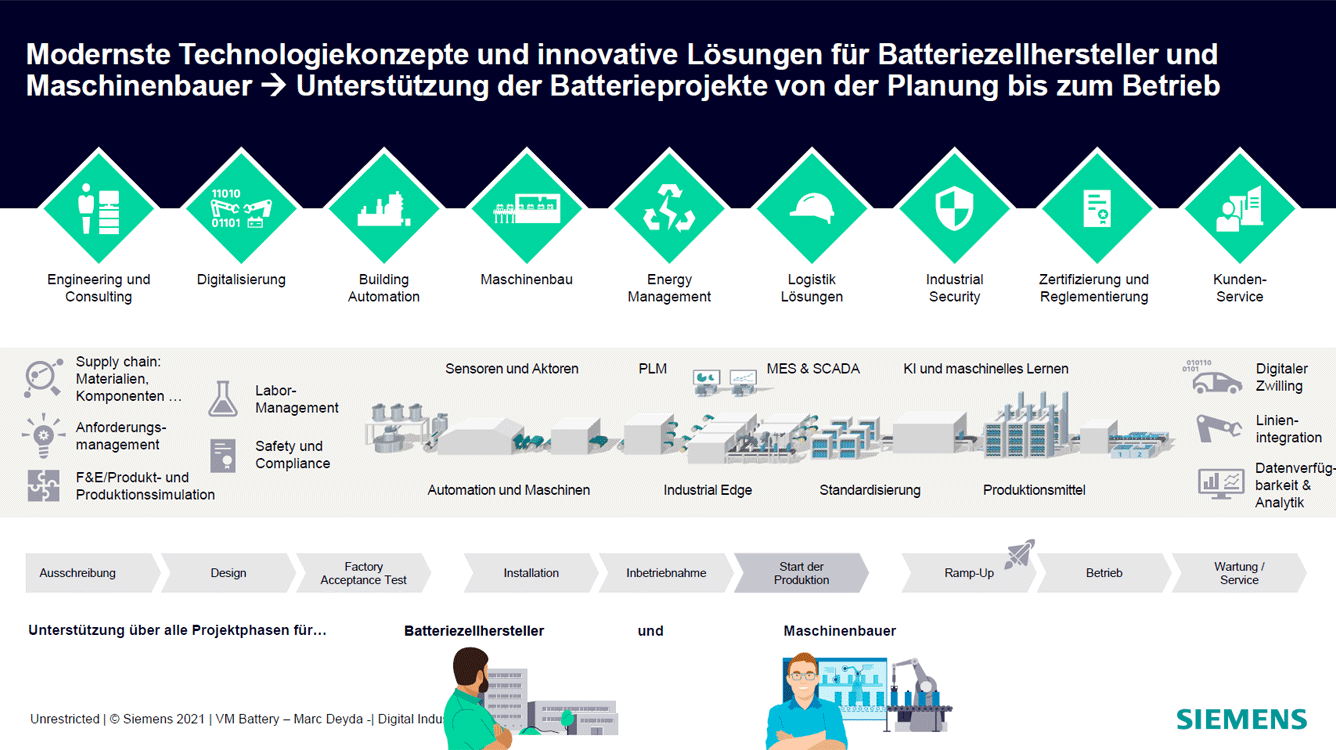
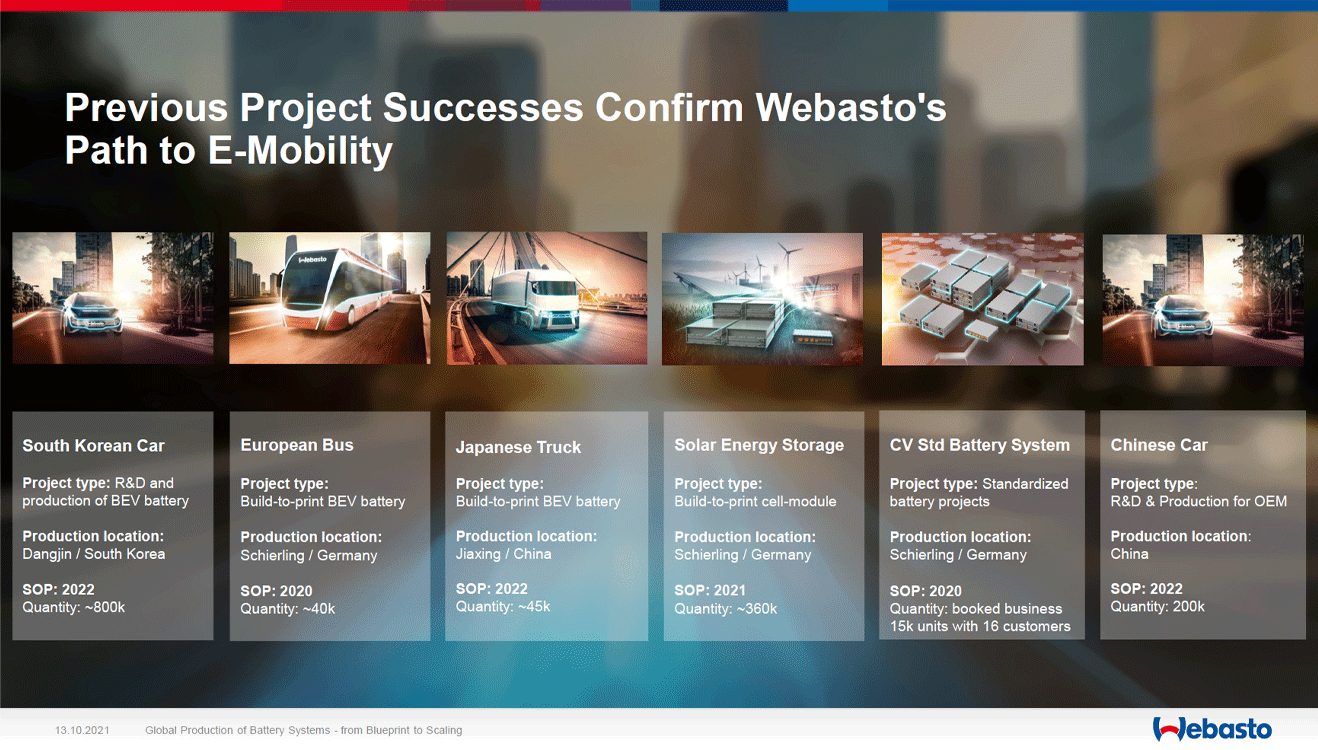
PEM RWTH Aachen
Heiner Heimes, geschäftsführender und promovierter Oberingenieur beim PEM (Production Engineering of E-Mobility Components) der RWTH Aachen berichtet aus dem Wachstum der Batterieproduktion. Um die Ankündigungen der Autoindustrie für den Umschwung zur Elektromobilität einzuhalten, werden sehr viele Batterien benötigt. Heute werden nur sechs Prozent davon in Europa produziert, so Heimes.
Deutschland wird nach der Einschätzung von Heimes bald zum bedeutendsten Standort in Europa werden. 2020 wurden in der EU 25 GWh Batteriakapazität gebaut. Glaubt man den Ankündigungen der Hersteller, sollen daraus in diesem Jahrzehnt 500 GWh werden. Auf Deutschland entfallen mehr als 400 GWh – „Wir werden zum Hotspot in Europa“, so Heimes über die Pläne. Dem Maschinen- und Anlagenbau kommt dabei eine besondere Bedeutung zu.
Genau dieser Maschinen- und Anlagenbau steht beim Hochlauf der heimischen Produktion unter großem Druck bei Kosten, Lieferzeiten und Technologie. So arbeitet die Industrie derzeit an einer Kostensenkung von über 40 Prozent bei den Ausgangsinvestitionen pro GWh, erklärt Heimes. Ein ehrgeiziges Ziel, das zum Beispiel über die Trockenbeschichtung erreicht werden kann.
Wie muss die Zukunft aktiv gestaltet werden? Aus Sicht von Heiner Heimes muss zuerst eine eindeutige strategische Ausrichtung festgelegt werden. Mehr Entschlossenheit und Geradlinigkeit, bitte. Ein Hin und Her, ob man selbst Zellen baue oder lieber bauen lasse, koste zu viel Geld und Zeit, sagt Heimes.
Dass Batteriezellen in den nächsten Jahren nachhaltig und CO2-neutral hergestellt werden müssen, scheint selbstverständlich, ist es aber nicht. Die Wege dorthin sind unterschiedlich und gehen weit über die Bereitstellung der Energie durch erneuerbare Quellen hinaus. „Die Batteriehersteller haben die Zeichen der Zeit erkannt“, erklärt Heimes. Ein geringer ökologischer Fußabdruck sei extrem wichtig.
Last but not least weist Heiner Heimes auf die Notwendigkeit der Qualifikation von Fachkräften hin. Die Belegschaft müsse fit gemacht werden für eine Welt ohne Verbrennungsmotoren: „Wir beobachten ein sehr starkes Interesse bei der Weiterbildung“, sagt Heimes, „es herrscht Aufbruchsstimmung“.
P3 Automotive GmbH
Markus Hackmann, Diplom-Ingenieur und Managing Director bei der P3 Automotive GmbH, ist einer der profundesten Kenner der Batteriezelle sowie der Zellchemie an sich und lädt zum Parforceritt durchs Themenfeld ein. Wo steht die Industrie, und wo geht die Reise hin?
Die Nachfrage nach Batteriekapazitäten steige enorm, so Hackmann. „Wir sind immer noch im Hochlauf des Marktes. Der Boom wird anhalten und weitergehen“, prognostiziert er. In China sei der Markt derzeit gesättigt, in der EU und in den USA sei das nicht der Fall. Das Gleichgewicht zwischen Fabrikaufbau und Nachfrage ist nicht permanent vorhanden.
Was dagegen immer gleich bleibt, sind die Zielparameter der Batteriezelle: Kosten, Energiedichte, Schnell-Ladefähigkeit (also Leistung), Sicherheit, Lebensdauer und Nachhaltigkeit.
Bei den Zellformaten Pouch, zylindrisch und rund sieht P3 im Lauf des Jahrzehnts eine Angleichung. Es wird nicht mehr entscheidend sein, welches Format eingesetzt wird, wobei in Zukunft auch alle gängigen Zellchemien in jedem Format eingeführt werden.
In seinem Vortrag geht Hackmann unter anderem auf Natrium-Ionen-Zellen (SIB) ein, die zurzeit als Alternative zu Lithium-Ionen-Zellen diskutiert werden. Ist das die nächste Generation? Abgesehen von der schlechten Energiedichte haben SIB etliche Vorteile gegenüber NCM-Zellen, vor allem bei den Kosten. Der Hauptkonkurrent von SIB ist wegen der schlechten Energiedichte allerdings eher LFP statt NCM. Eigentlich waren SIB eher als Heimspeicher und nicht als Traktionsbatterien vorgesehen. Die Technologiereife ist noch nicht vorhanden – könnte jedoch über CATL ab 2023 bewiesen werden. Insofern kann CATL an der Realität gemessen werden. Die Skepsis bleibt.
Aktuell, so analysiert P3, haben alle Zellformate die Marke von 100 US-Dollar pro kWh nach unten durchbrochen. „Der größte Hype sind Solid State Batterien“, ist sich Markus Hackmann sicher. „Es wird sehr viel und weltweit daran gearbeitet.“ Aber bis zur Serienproduktion und einer guten Leistungsfähigkeit sei es noch ein weiter Weg.
Beim Batteriesystem sei Cell-to-Pack der Megatrend; die direkte Integration von Zellen ins Pack oder sogar in die Karosserie (Cell-to-Vehicle). Dadurch wird das Verhältnis von aktivem Material zu Verpackung deutlich verbessert. Allerdings müssen die Hersteller auf die Sicherheit achten. Los geht’s mit der eher unkritischen LFP-Zellchemie. Aber denkbar sind auch andere Zellchemien, so P3.
Twaice
Stephan Rohr von Twaice analysiert mit einem digitalen Zwilling Batterien: Twaice bietet Softwarelösungen zur Prognose und Simulation des Lebenszyklus an.
Worum geht’s? Co-CEO Rohr: „Die Batterie macht bis zu 40 Prozent des Fahrzeugwerts aus. Darum müssen wir uns mit Software kümmern.“ Die Herausforderung ist, dieses wertvolle Verschleißteil per Software gut zu managen und zu überwachen. Das betrifft nicht nur das Leben im Elektroauto als Traktionsbatterie, sondern auch die vorausgegangene Entwicklung sowie das anschließende Second Life.
Der Hersteller kann alle Parameter der Batterie überwachen – aber nicht durchgehend bestimmen. Wie ein Fahrer das Elektroauto bewegt oder wie das Wetter ist, ist nicht kontrollierbar. „Wir ermöglichen die Simulation des Realbetriebs durch unsere Software“, sagt Stephan Rohr. Das gilt wie beschrieben für Forschung, Betrieb und After Life.
Welches Potenzial das Monitoring per Software hat, ist zum Beispiel bei der Degradation der Batterie ablesbar. Wie wirkt sich das Ladeverhalten aus? Welche Verschleißspanne bewirken unterschiedliche Fahrweisen? Wie soll die Ladekurve verlaufen? Die Software von Twaice soll das im Voraus prognostizieren können.
Simulationen haben den Vorteil, schneller zu sein als die Wirklichkeit. Es kann eine Vielzahl von Nutzungsmöglichkeiten durchgespielt werden – und so letztlich Geld der Hersteller und der Kunden sparen.
Siemens
Marc Deyda, Global Business Delevoper bei Battery@Siemens, berichtet über die Chancen von Digitalisierung und Automatisierung bei der Batterieproduktion. Siemens bietet die gesamte Produktionskette von der Zelle bis zum System an. Kern des Beitrags von Deyda ist die Automatisierung der Zellfertigung und deren Vorabplanung. So kann etwa die Zusammensetzung der Kathodenmaterialien im Voraus per Software optimiert und definiert werden – das senkt den Rohstoffbedarf.
Das gleiche Prinzip der Digitalisierung gilt auch für die Konstruktion und Validierung des Batteriesystems. Viele Prozesse bei der Produktion sind miteinander vernetzt; alle werden vorab simuliert und nicht etwa auf einen Bierdeckel gezeichnet, erklärt Deyda. „Wir wollen dem Endkunden die Möglichkeit geben, das komplexe Konstrukt einer Batteriefertigung im Vorfeld zu verstehen und zu simulieren.“
Zelldesign, Engineeringfluss, Maschinenbau, alles wird digital und virtuell in Ruhe durchdacht und reduziert so das finanzielle Risiko. Hierfür stellt Battery@Siemens diverse Tools bereit. „Das Business wächst in Europa sehr schnell“, sagt Deyda mit Blick auf die vielen Batteriefabriken, die in Vorbereitung sind.
Fazit
Es ist faszinierend, die Geschwindigkeit der Entwicklung bei Batterie-Zellen und -Systemen sowie den Fabriken zu beobachten. Das Wachstum in allen Bereichen ist rasant. Deutschland könnte zu einem Hotspot der Batteriefertigung werden – und dafür werden etliche Fachkräfte gebraucht. Der Hochlauf ist in vollem Gang und wird sich in diesem Jahrzehnt fortsetzen.
0 Kommentare