Blackstone startet Serienproduktion von 3D-gedruckten Batteriezellen
Blackstone Resources hat bei einer Veranstaltung in seinem Werk im sächsischen Döbeln sein Herstellungsverfahren für Lithium-Ionen-Batterien aus dem 3D-Drucker vorgestellt. In diesem Rahmen wurde auch die Anlage für die Serienproduktion angefahren.
Die Veranstaltung und Fertigung findet bei Blackstone Technology statt, der deutschen Tochter der Schweizer Holdinggesellschaft Blackstone Resources AG. Aufgrund der Corona-Lage musste die Pressekonferenz allerdings online übertragen werden.
Dabei stellte Blackstone seine im Februar angekündigten LFP-Zellen im Detail vor. Mit dem Kathodenmaterial von IBU-Tec aus Weimar werden nun in Döbeln im Landreis Mittelsachsen die LFP-Zellen in einem neuen 3D-Druck-Verfahren hergestellt. Damit können laut dem Unternehmen die Stromspeichernden schichten der Batteriezellen dicker werden, die Energiedichte soll so um 20 Prozent höher sein – Blackstone nennt das „Thick Layer Technology“. Konkret kündigte Blackstone hier 220 Wh/kg an. Zum Vergleich: Die Blade-Batterien des chinesischen Herstellers BYD, die als technologisch fortgeschrittene LFP-Zellen angesehen werden, sollen auf Zell-Ebene auf 166 Wh/kg kommen.
Blackstone gibt weiter an, dass die Größe der Zellen mit dem Verfahren flexibel auf die Kundenwünsche zugeschnitten werden können – ein Autobauer mit einem im Unterboden verbauten Batteriepack hat hier andere Anforderungen als der Hersteller eines E-Busses, der die Batterien auf dem Fahrzeugdach montiert. Die Platzersparnis beziffert Blackstone mit 15 Prozent, die Materialersparnis mit 20 Euro/kWh. Und der Energieverbrauch in der Produktion sei um 23 Prozent niedriger. Blackstone beginnt zwar mit LFP- und NMC-Zellen, die Technologie soll aber für alle Zellchemien einsetzbar sein. So will Blackstone auch Festkörper-Akkus drucken können – mit der Solid-State-Technologie soll die Enerigedichte dann nochmals um 70 Prozent steigen.
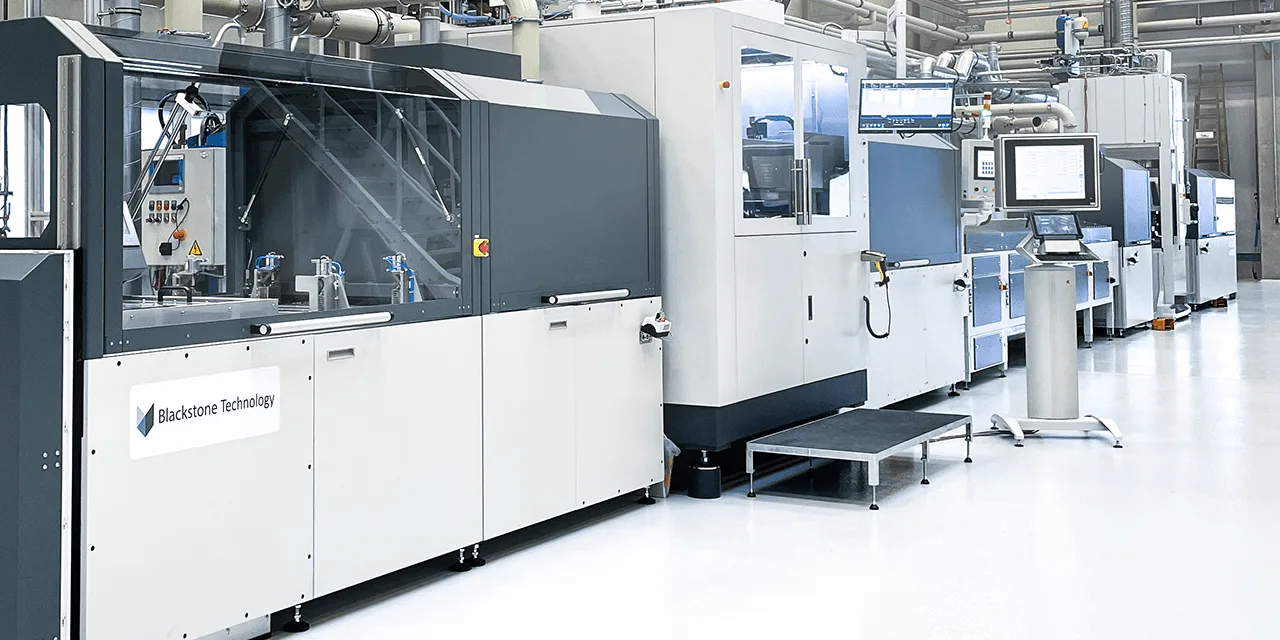
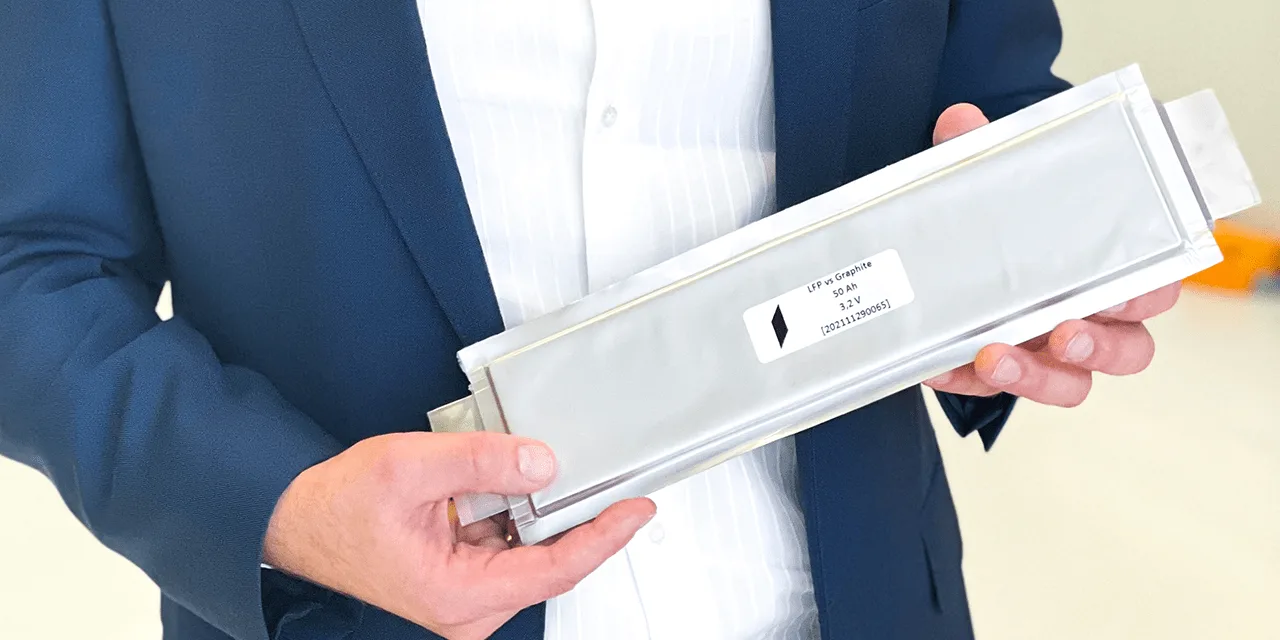
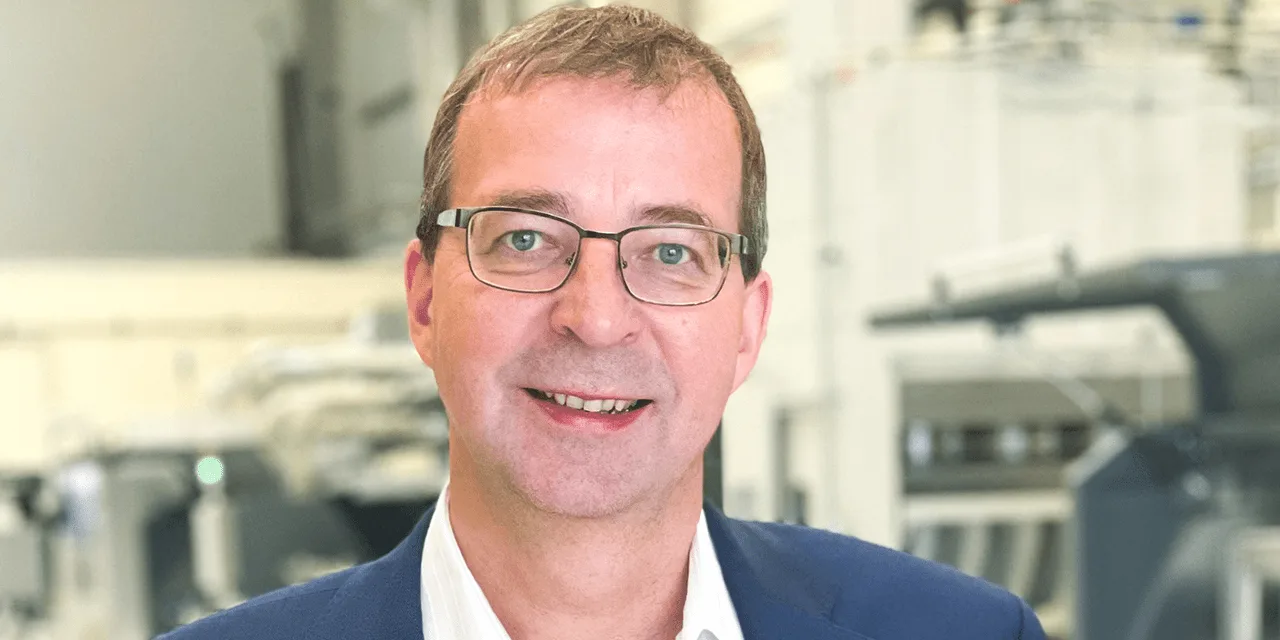
Batteriezellen im Sekundentakt
Ulrich Ernst, Gründer und CEO von Blackstone Resources, bezeichnet die im 3D-Druck produzierten Batterien als „Game Changer“. „Wir erreichen damit eine um 20 Prozent erhöhte Energiedichte unserer Ladungsträger bei gleichzeitig drastischer Reduktion umweltrelevanter Einflüsse“, sagt Ernst. „Das patentierte Verfahren setzt auf einen umweltverträglichen, rein wasserbasierten Prozess und reduziert Abfallstoffe um 50 Prozent. Damit leisten wir einen wichtigen und nachhaltigen Beitrag zur Verkehrswende und im Kampf gegen den Klimawandel.“
Im Rahmen der Veranstaltung wurde nicht nur die Zelle vorgestellt, sondern auch die Serienfertigung der Elektrode angefahren. Bereits im kommenden Jahr soll die angestrebte Produktionskapazität von 500 MWh am Standort erreicht werden. Das langfristige Ziel sei die Produktion von Batteriezellen im Sekundentakt, so Holger Gritzka, Geschäftsführer von Blackstone Technology. Die Vision: „Mit einem einzigen Maschinenpark drucken wir schnell und kostengünstig Zellen in verschiedenen Formen, verschiedenen Elektroden und Elektrolytmaterialien in großem Maßstab.“
Aktuell sind 14 Mitarbeiter in Döbeln beschäftigt, im kommenden Jahr soll auf 38 Angestellte ausgebaut werden. Die Produktionsanlage hat die deutsche Tochter Blackstone Technology in einem bestehenden Gebäude errichtet, um Zeit zu sparen. Die Immobilie hatte Gritzka nach eigenen Angaben nicht nur mit der passenden Größe und ihrem neuwertigen Zustand überzeugt, sondern auch mit der Lage: Städte wie Leipzig, Chemnitz und Dresden sind alle recht ähnlich entfernt, was die Suche nach qualifizierten Mitarbeitern vereinfachen soll.
Übrigens: Dass der im Februar angekündigte Produktionsstart im Sommer nicht gehalten werden konnte, lag nicht an den Mitarbeitern – sondern wenig überraschend an der Corona-Pandemie: Die Produktionsanlage konnte aufgrund von Lieferschwierigkeiten und Beschränkungen erst mit dreimonatiger Verzögerung fertiggestellt werden.
Bei dem virtuellen Event traten nicht nur Blackstone-Vertreter auf, sondern auch Partner wie Robert Orten von Orten Electric Trucks, Thomas Sautter von Voith, Benjamin Friedirch von Ecovolta und Michael Roscher von Liovolt. „Als nächster Schritt steht nun die Entwicklung eines Batteriesystems mit unserem Partner ecovolta an, mit Voith SE und Orten Electric Trucks streben wir ein Projekt zur Ausstattung elektrifizierter E-Busse mit unserer Batterietechnik an“, sagt Serhat Yilmaz, CMO bei Blackstone Resources.
Expansionspläne für Deutschland und weltweit
Zudem arbeitet Blackstone gemeinsam mit seinem Partner Liovolt bereits an einer Weiterentwicklung, einer bipolaren Batterie. Dabei handelt es sich um Lithium-Ionen-Batterien, die aus gestapelten und in Reihe geschalteten Elektroden bestehen, die bipolar ausgelegt sind. „Das heißt, dass die aktiven Materialien für die Kathode und auf der anderen Seite die aktiven Materialien für die Anode auf einen gemeinsamen Elektrodenträger aufgebracht sind“, erklärt Yilmaz.
Perspektivisch soll die Produktion über die 500 MWh der Phase I erweitert werden: In seiner Präsentation sprach Gritzka auch von einer Kleinserienproduktion. Die zweite Phase soll eine Kapazität von fünf GWh pro Jahr umfassen und ebenfalls in Deutschland gebaut werden. Die Phase III, eine Automotive-Zelle mit „10+ GWh/Jahr“, soll durch eine Erweiterung in Deutschland und eine weltweite Expansion umgesetzt werden. Einen Zeitplan für die Phasen II und III nannte Gritzka aber nicht.
Quelle: Info per E-Mail
0 Kommentare