TÜV Rheinland eröffnet Prüflabor für E-Auto-Batterien
Der TÜV Rheinland hat sein Batterie Test Center in Aachen eröffnet. Die Anlage soll das modernste unabhängige Prüfzentrum in Europa sein. Dort können nicht nur elektrische Tests und Simulationen der Haltbarkeit durchgeführt werden, sondern auch Sicherheitstests bis hin zur Zerstörung der Batterie.
Wie zur Ankündigung des Projekts im Oktober 2020 berichtet, ist das Prüfzentrum im niederländisch-deutschen Innovationspark Avantis entstanden. In das rund 2.200 Quadratmeter große Labor haben der TÜV Rheinland und seine Partner laut der Mitteilung 24 Millionen Euro investiert. Im Vollbetrieb werden 25 Mitarbeitende beschäftigt sein.
In der Anlage können Traktionsbatterien bis zu einem Gewicht von 800 Kilogramm geprüft werden. Die maximalen Abmessungen liegen bei einer Länge von 2,30 Metern, einer Breite von 1,60 Metern und einer Höhe von 40 Zentimetern. Der Energiegehalt der zu prüfenden Batterien kann laut dem TÜV bei bis zu 150 kWh liegen. Damit sieht sich die Prüfgesellschaft für die kommenden Fahrzeuggenerationen gut aufgestellt – in den meisten Fahrzeugen wiegen die Batterien zwischen 300 und 600 Kilogramm.
Dabei geht es nicht um eine unabhängige Überprüfung von Batterien in gebrauchten Elektroautos, sondern um die Homologation – also den Typprüfung neuer Kraftfahrzeuge oder in diesem Fall neuer Kraftfahrzeugkomponenten. Die in neuen Fahrzeugmodellen verbauten Batterien müssen unterschiedliche Sicherheitsstandards erfüllen. Genau das will der TÜV Rheinland in der Anlage abprüfen können. Konkret geht es um die internationalen Normen GTR 20, UN 38.3 sowie LV 124, die US-amerikanischen Normen SAE J 2224 sowie SAE J 2029, die für die EU und Japan wesentliche ECE R100, für China GB 38031, Südkorea KMVSS sowie Indien AIS-048. Die erwähnte UN 38.3 stellt zum Beispiel Anforderungen zum Transport von Antriebsbatterien.
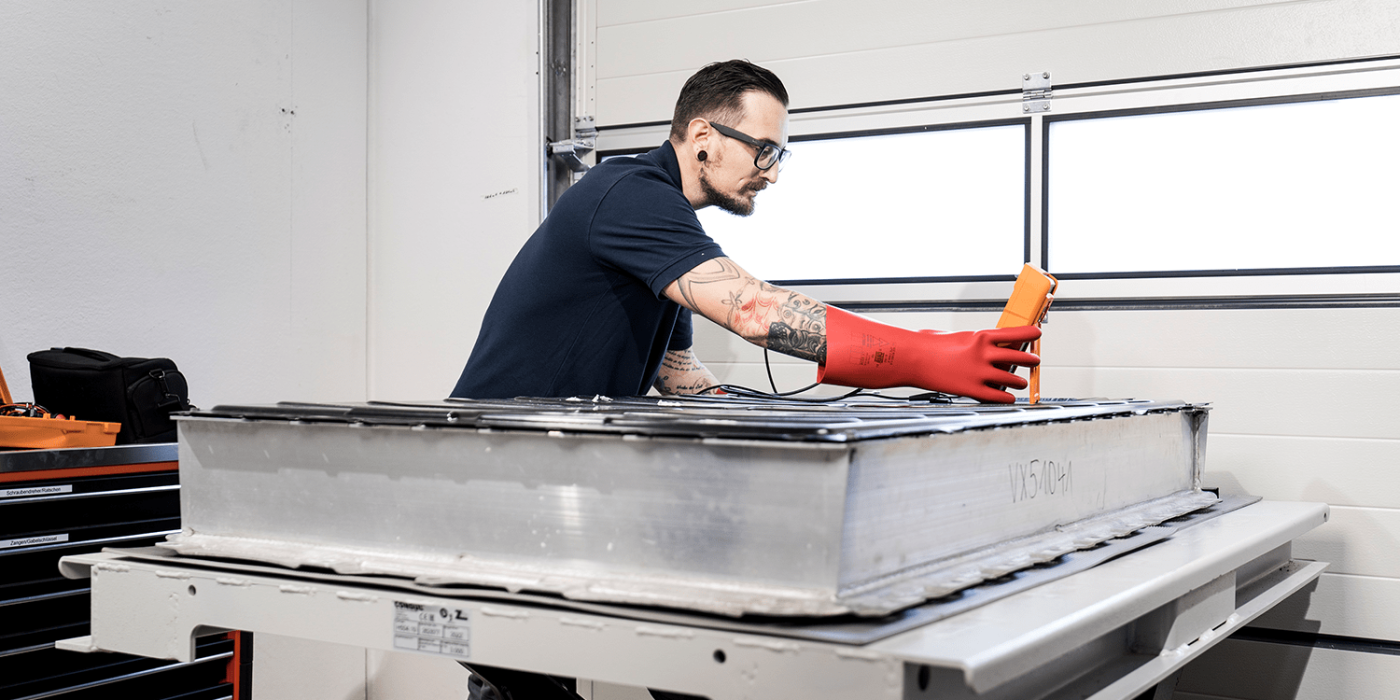
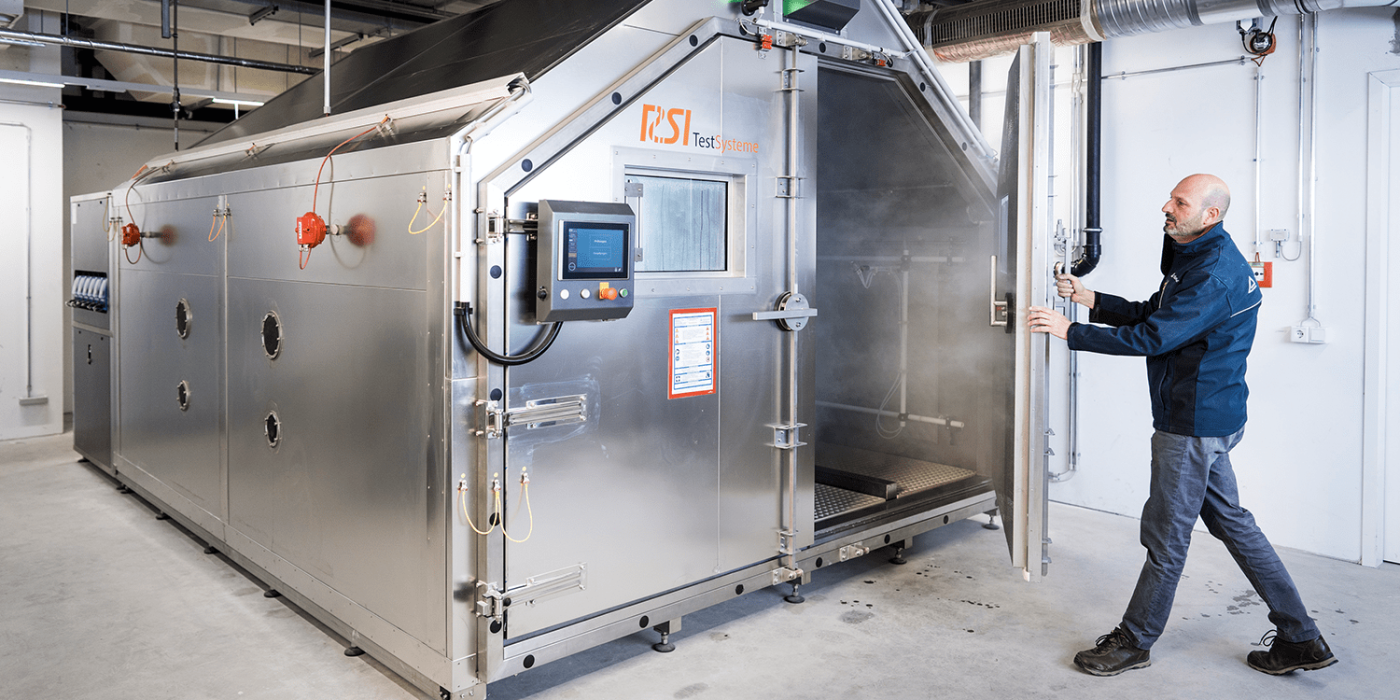
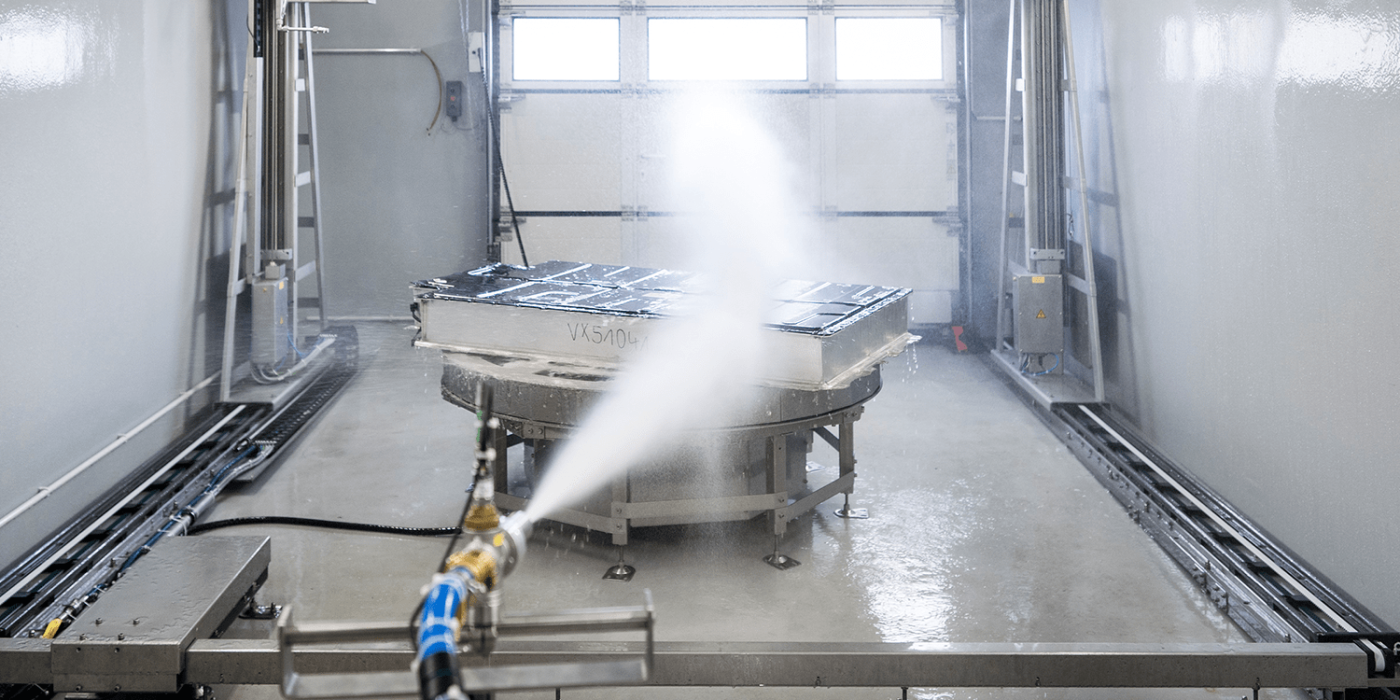
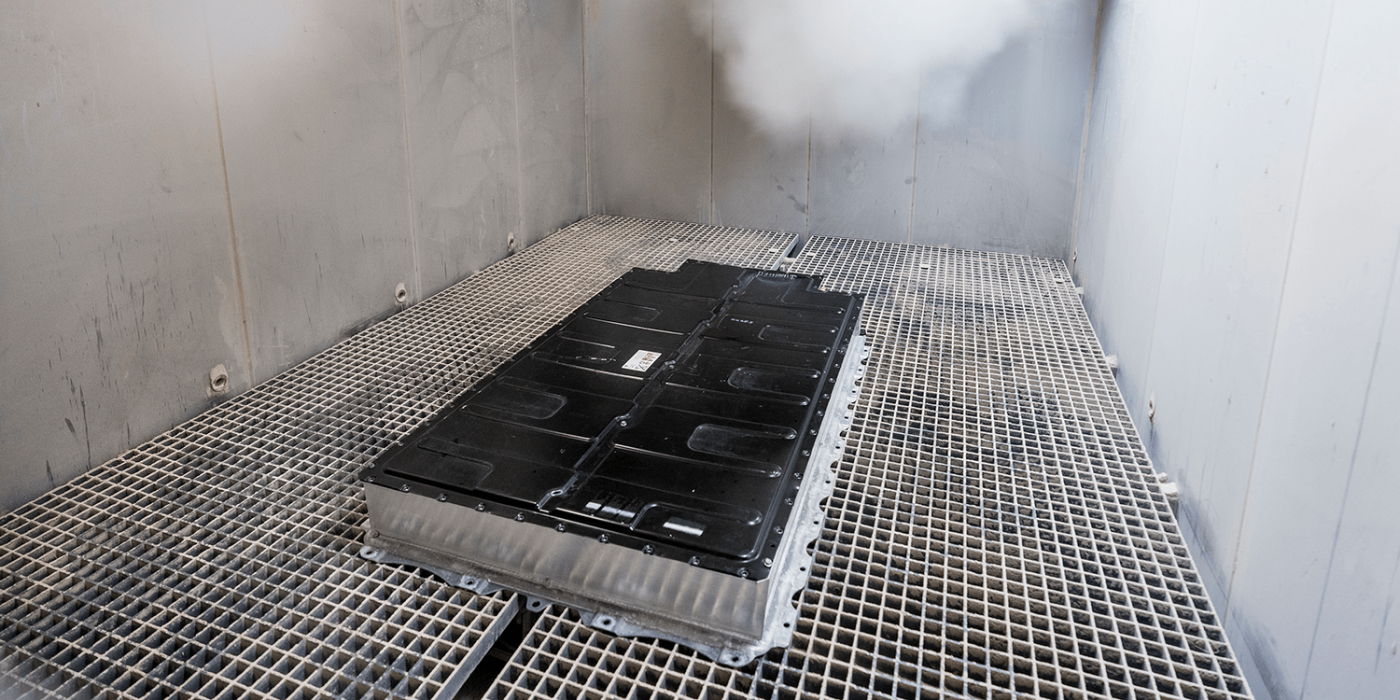
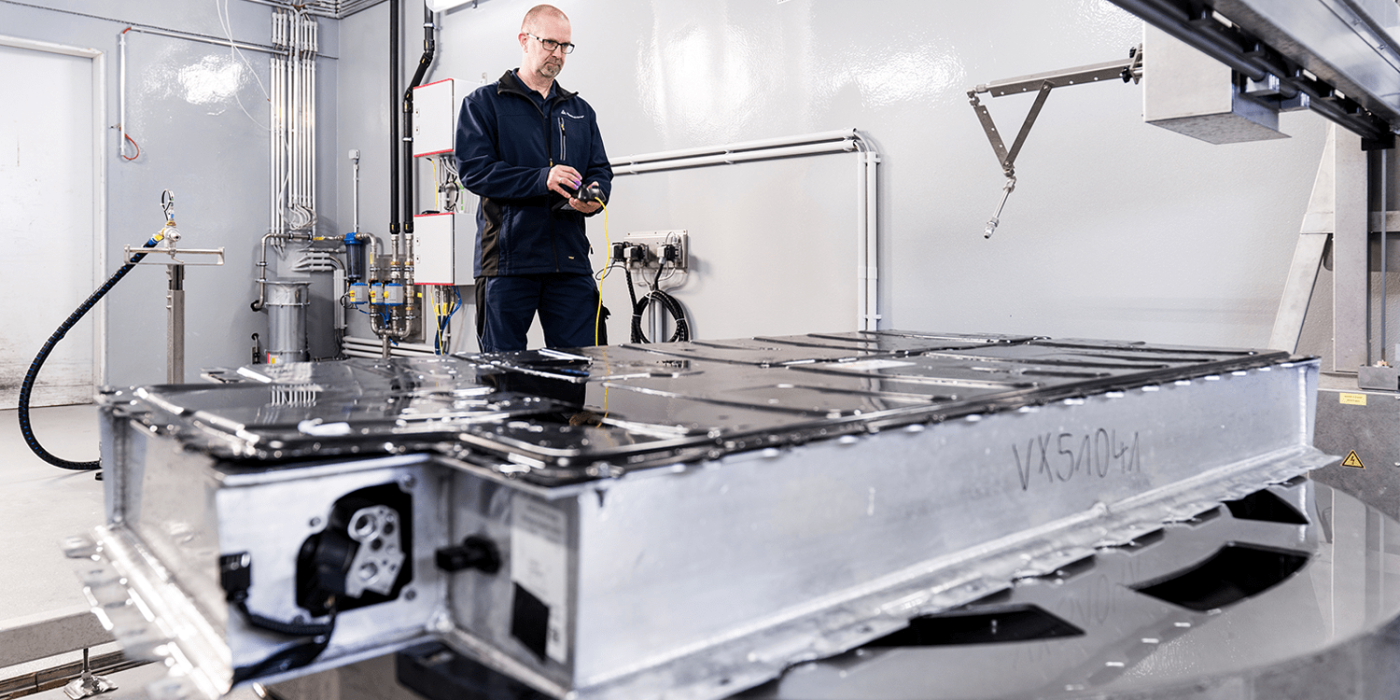
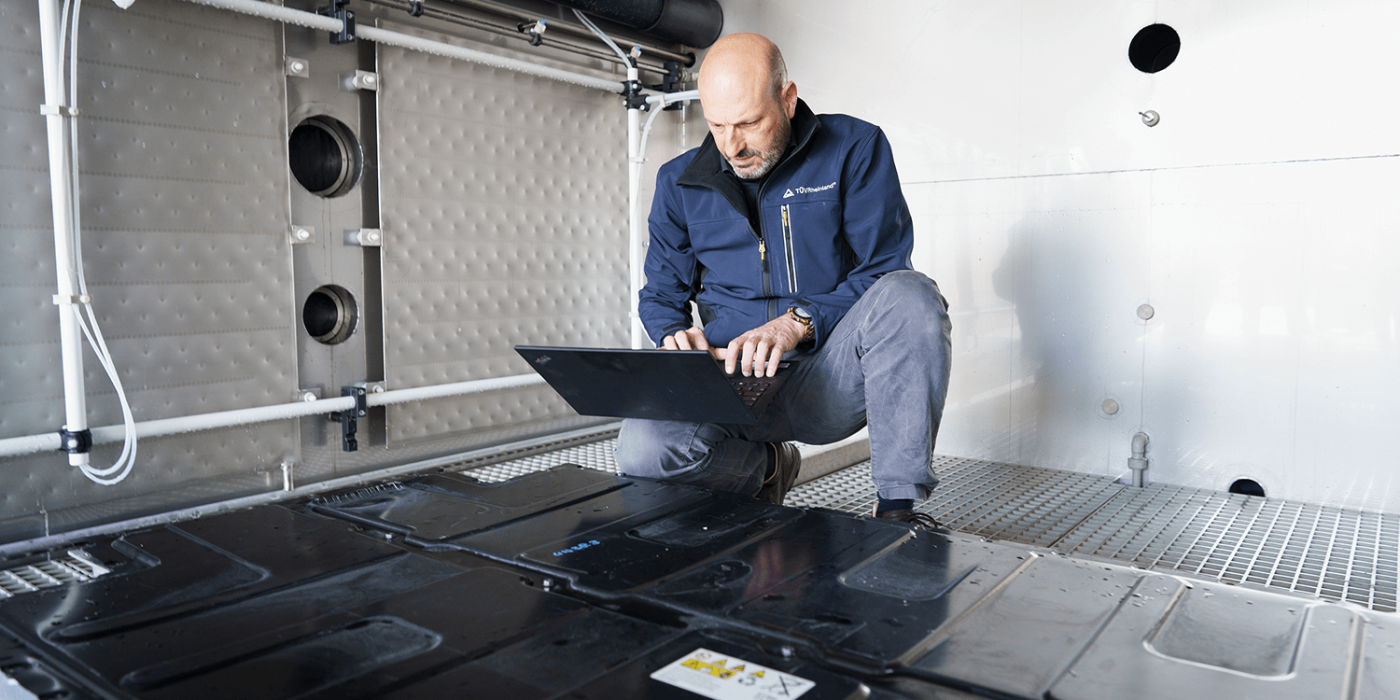
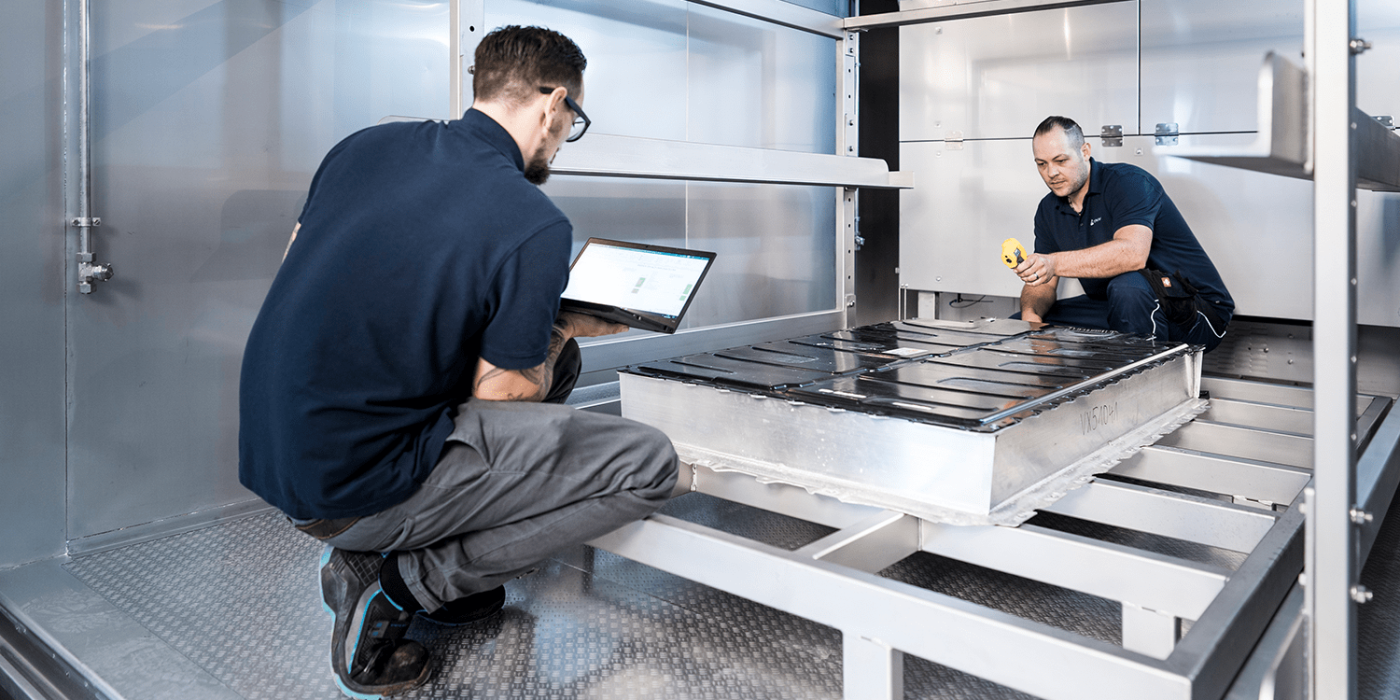
Eigener Bunker für zerstörende Batterie-Tests
Die Tests umfassen die elektrische Sicherheit und Verlässlichkeit, Leistung und spezielle Klima- und Umweltbelastungen. Im Anschluss werden mechanische Tests und Haltbarkeitstests durchgeführt, bevor dann die zerstörenden Prüfungen folgen. Dabei werden die elektrischen, thermischen oder mechanischen Belastungsgrenzen der Batterie ermittelt.
Um diese Test präzise durchführen zu können, wurden in den 18 Monaten Bauzeit zum Beispiel sieben Klimakammern errichtet, die Temperaturen zwischen -60 und +90 Grad Celsius und eine Luftfeuchtigkeit von zehn bis 95 Prozent abbilden können. Zudem gibt es eine Salz-Korrosionskammern, eine Kammer zur Staubprüfung, einen Shaker zur Simulation von Schwingungen und Stößen sowie einen Teststand für Schwallwasser (Prüfkammer nach LV124). Auf einem der 16 Batterie-Testständen können die elektrischen Tests sowie die Simulation der Lebensdauer durchgeführt werden. In einer speziellen Bunkeranlage werden dann die zerstörenden Tests durchgeführt. Die Anlage mit den Maßen 8x7x8 Meter ist für Falltests, Nagelpenetration, Über- und Tiefenentladung, Druck, Quetschung und Brandsimulation ausgelegt.
Neben den Typprüfungen sind auch Tests von Prototypen-Batterien möglich, die bei der Entwicklung unterstützen sollen – damit das spätere Serienprodukt genau jene Normen einhält. Genau diese Entwicklung geht gerade rasant voran. „Die Dynamik im Bereich Elektromobilität ist extrem hoch. Hersteller drängen mit immer neuen Modellen auf den boomenden Markt“, sagt Michael Fübi, Vorstandsvorsitzender der TÜV Rheinland AG. „Unser Ziel ist es, mit der Arbeit an unserem neuen Standort in Heerlen-Aachen dazu beizutragen, Elektromobilität sicher zu gestalten und gleichzeitig Innovationen zu begleiten.“
„Die Innovationskraft im Bereich der Elektrofahrzeugbatterien ist so hoch wie nie zuvor – dementsprechend wichtig sind unabhängige Prüfkapazitäten“, sagt Achim Kampker, Leiter des Lehrstuhls „Production Engineering of E-Mobility Components“ (PEM) der RWTH Aachen bei der Inbetriebnahme des Labors. „Haltbarkeit und Kosten, Materialeinsatz und Leistungsfähigkeit, Reichweite und Recycling-Fähigkeit: Das sind zentrale Aspekte der Batterieentwicklung. Die Prüfleistungen des neuen Testzentrums tragen zu einer höheren Verlässlichkeit der Technologien bei, aber auch zu marktfähigen Innovationen.“
Quelle: Info per E-Mail
0 Kommentare