Fraunhofer IIS will E-Auto-Batterien mit Röntgenstrahlen prüfen
Mit dem neuen System sollen laut dem Fraunhofer-Entwicklungszentrum Röntgentechnik, ein Bereich des Fraunhofer-Instituts für Integrierte Schaltungen IIS, vor allem die Kosten und die Dauer einer solchen Prüfung sinken. Denn bisher sei das vollständige Röntgen endmontierter Fahrzeuge „nur an wenigen Orten weltweit unter Laborbedingungen“ möglich – unter anderem am Entwicklungszentrum Röntgentechnik des Fraunhofer IIS in Fürth. Da die Prozedur so aufwändig und teuer ist, wird sie nur bei wenigen, sicherheitsrelevanten Bauteilen angewandt.
Das neu entwickelte AIR-System gleicht einer Waschanlage, wie es die Forscher beschreiben. Die Röntgenstrahlen werden von oben emittiert, der Strahl passiert das Fahrzeug samt der Batterie und wird dann von einem Detektor am Boden aufgefangen und verarbeitet. „Selbst in voll gekapselten Batteriemodulen ist eine Detailbetrachtung der Batterie möglich, um Aussagen über den mechanischen Zustand einzelner Batteriezellen, des Batterierahmens und weiterer Merkmale treffen zu können“, so das Fraunhofer IIS.
Damit sollen etwa die Diagnose-Möglichkeiten für Gutachter erweitert werden. „Es läuft in der Praxis im Wesentlichen genauso ab, wie man es von der Fehlerdiagnose halbwegs moderner Fahrzeuge kennt. Stecker rein und eine Diagnosesoftware liest eventuelle Probleme aus. Teilweise wird dies bei manchen Konzepten über mehrere Tage während der Fahrt praktiziert“, beschreibt Klaus Böhm der Hochschule München, der selbst als Gutachter tätig ist. Er berichtet auch von einem bekannten Problem: „Bei schwerwiegenderen Unfällen, beispielsweise dann, wenn der Airbag im Fahrzeug ausgelöst hat, gibt es sehr klare Handlungsanweisungen der Hersteller. Hier muss in der Regel verpflichtend der Austausch der Traktionsbatterie vorgenommen werden, auch wenn diese unter Umständen keinen Schaden genommen hat.“
Da die einzelne Batterie nach dem Unfall ohne entsprechenden Aufwand nicht genauer untersucht werden kann, würde sie ins Recycling gehen – obwohl sie unter Umständen voll funktionsfähig ist. „Hier gibt es einen großen Bedarf des Marktes nach einer zusätzlichen objektiven Bewertungsmöglichkeit von Fahrzeugbatterien. Deshalb forschen wir bereits seit vielen Jahren an Röntgensystemen, die bei der Begutachtung von Hochleistungsakkus eine zentrale Rolle einnehmen könnten“, so Michael Salamon, Gruppenleiter am Entwicklungszentrum Röntgentechnik des Fraunhofer IIS.
In der Testphase hat das Entwicklungszentrum Röntgentechnik unter anderem ein Tesla Model 3 durchleuchtet. In dem Scan sind neben der Struktur des Fahrzeugs und des Batteriepacks auch die Zellen zu erkennen. „Deutlich sichtbar sind die einzelnen zylindrischen Batteriezellen und deren richtige Lage, wodurch eine Beschädigung auszuschließen ist“, schreibt das Institut dazu.
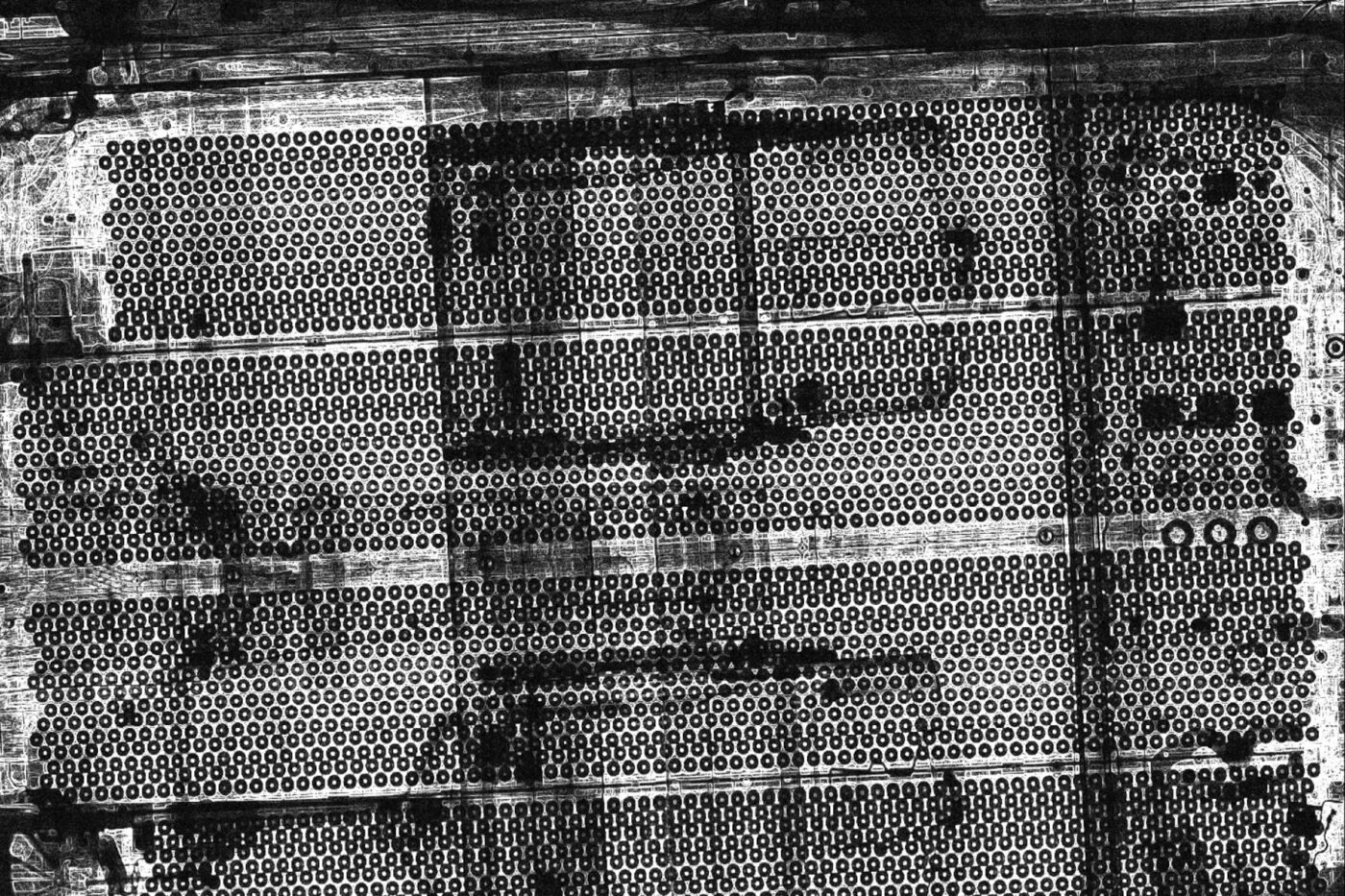
Das AIR-System wird nun im nächsten Schritt für Anwendungen der Schadensbegutachtung, Wertermittlung und Lebenszyklusanalyse im Feld erprobt und weiterentwickelt. Dafür sucht das Institut Probanden, die ihr Fahrzeug für die Erhebung von Röntgendaten zur Verfügung stellen – den Kontakt finden Sie in der verlinkten Pressemitteilung.
Auch wenn die Optimierung des Systems noch läuft, vom Potenzial sind Salamon und Böhm überzeugt. „Mit der AIR-Technologie erschließt sich erstmalig die Möglichkeit, eine detaillierte Betrachtung des Fahrzeugunterbodens schnell und einfach vorzunehmen. Mit der Ausrichtung der Technologie auf den Lebenszyklus von Fahrzeugen, leistet das Fraunhofer IIS im Rahmen einer Strategischen Initiative Pionierarbeit, um das Vertrauen in die noch junge Technologie zu steigern und so unter anderem den im Entstehen befindlichen Gebrauchtwagenmarkt zu fördern“, sagt Salamon. Und Böhm ergänzt: „AIR hat das Potential, die Gutachtenerstellung im Kontext der Elektromobilität – und darüber hinaus – zu revolutionieren. Genauere und belastbarere Gutachten können zudem zu kalkulierbareren Gebrauchtwagen-Prozessen und zu günstigeren Versicherungsprämien bei Elektrofahrzeugen führen.“
2 Kommentare