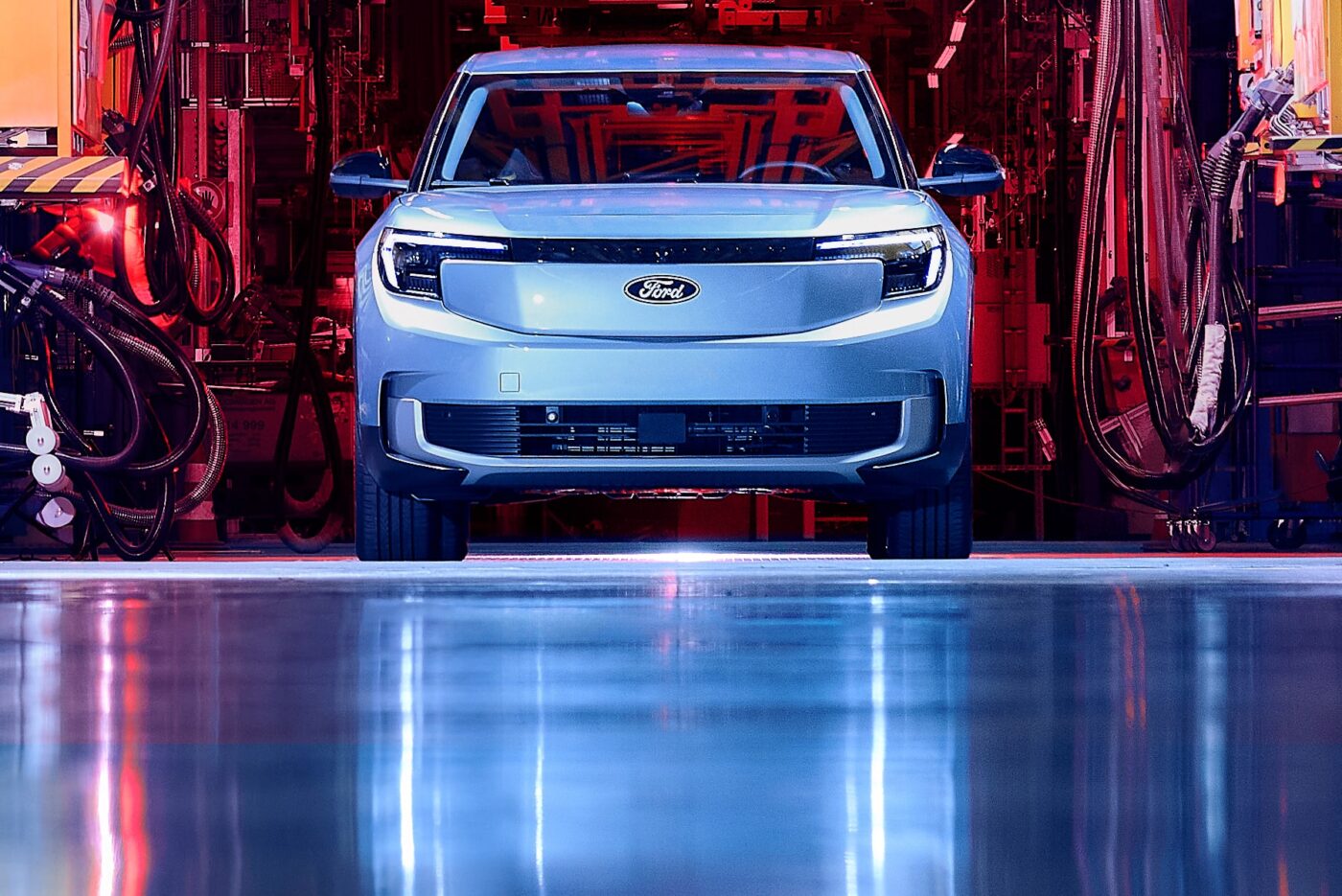
Hoffnungsträger: Ford läutet die Serienproduktion des elektrischen Explorer ein
Mehr als zwei Milliarden US-Dollar hat die Zentrale in Detroit in den deutschen Standort investiert, um das Kölner Werk fit für die Zukunft zu machen – für die Produktion von Elektroautos. Denn seit dem Sommer 2023, als in der Endmontage der letzte Fiesta fertiggestellt wurde, hat kein Serienfahrzeug mehr die Halle verlassen. Genau genommen müsste man sogar den vorletzten Fiesta nennen, denn das allerletzte Exemplar hat die Halle nie verlassen – das Fahrzeug steht als Ausstellungsstück bis heute mit den Unterschriften aller Mitarbeiter am Rande der Montagelinien.
Doch nicht nur die Montage des Fiesta ist in Köln Geschichte, für den Explorer und das zweite Modell, das noch in diesem Jahr seine Premiere feiern wird, wurde und wird der gesamte Standort umgebaut. Getriebe werden in Köln keine mehr gefertigt, die alte Motorenproduktion wurde abgerissen. Wo früher Dreizylinder hergestellt wurden, laufen derzeit noch die Arbeiten an der eigenen Batterie-Montage. Ab dem Sommer will Ford die Batteriepacks für das E-SUV Explorer und den sportlicheren Elektro-Crossover selbst montieren. Bis dahin werden die fertigen Batteriepacks von Technik-Partner VW komplett fertig angeliefert – konkret aus Skodas Batterie-Montage in Mlada Boleslav.
Der europäische Ford Explorer, nicht zu verwechseln mit dem größeren US-Modell, ist bekanntlich der Erstaufschlag aus der Kooperation mit Volkswagen – alle technischen Daten zu dem Modell finden Sie in diesem Artikel. Der VW-Konzern stellt die technische Basis über seine Elektro-Plattform MEB bereit und liefert einige Komponenten direkt in das Kölner Ford-Werk, derzeit eben noch die komplette Batterie, den Elektromotor und etwa einzelne Blechteile für die Plattform-Konstruktion an sich.
Ford baut in Köln nur noch E-Autos
Im Kölner Werk, seit dem Umbau zur reinen Elektroauto-Produktionsstätte Cologne Electric Vehicle Center genannt, fügt Ford im Rohbau diese Blechteile mit über 250 Robotern in einem hochautomatisierten Prozess zusammen. Schweißen, kleben, löten – alles ist mit dabei. In diesen Unterbau werden später in der Endmontage auf einer eigenen Linie die Batterie und die beiden Achsen eingebaut.
Die eigentliche Karosserie entsteht wenige Meter weiter komplett in Köln, ohne VW-Teile. Der neue Explorer ist das erste vollelektrische Großserienmodell von Ford, das in Europa für Europa entwickelt wurde. Beim Design der Karosserie haben sich die Ford-Leute von dem amerikanischen Markenerbe inspirieren lassen und den Explorer zum Beispiel etwas breitbeiniger und präsenter entworfen als die Schwestermodelle aus dem Wolfsburger Markenreich. „Der Explorer musste ein echter Ford werden und eigenständig auftreten“, sagt auch Fords Geschäftsführer Marketing und Handel in der DACH-Region, Christian Weingärtner. „Wir wollten nicht nur unser Logo auf ein anderes Auto kleben. Der Explorer nutzt zwar eine VW-Plattform, sieht aber ganz anders aus.“
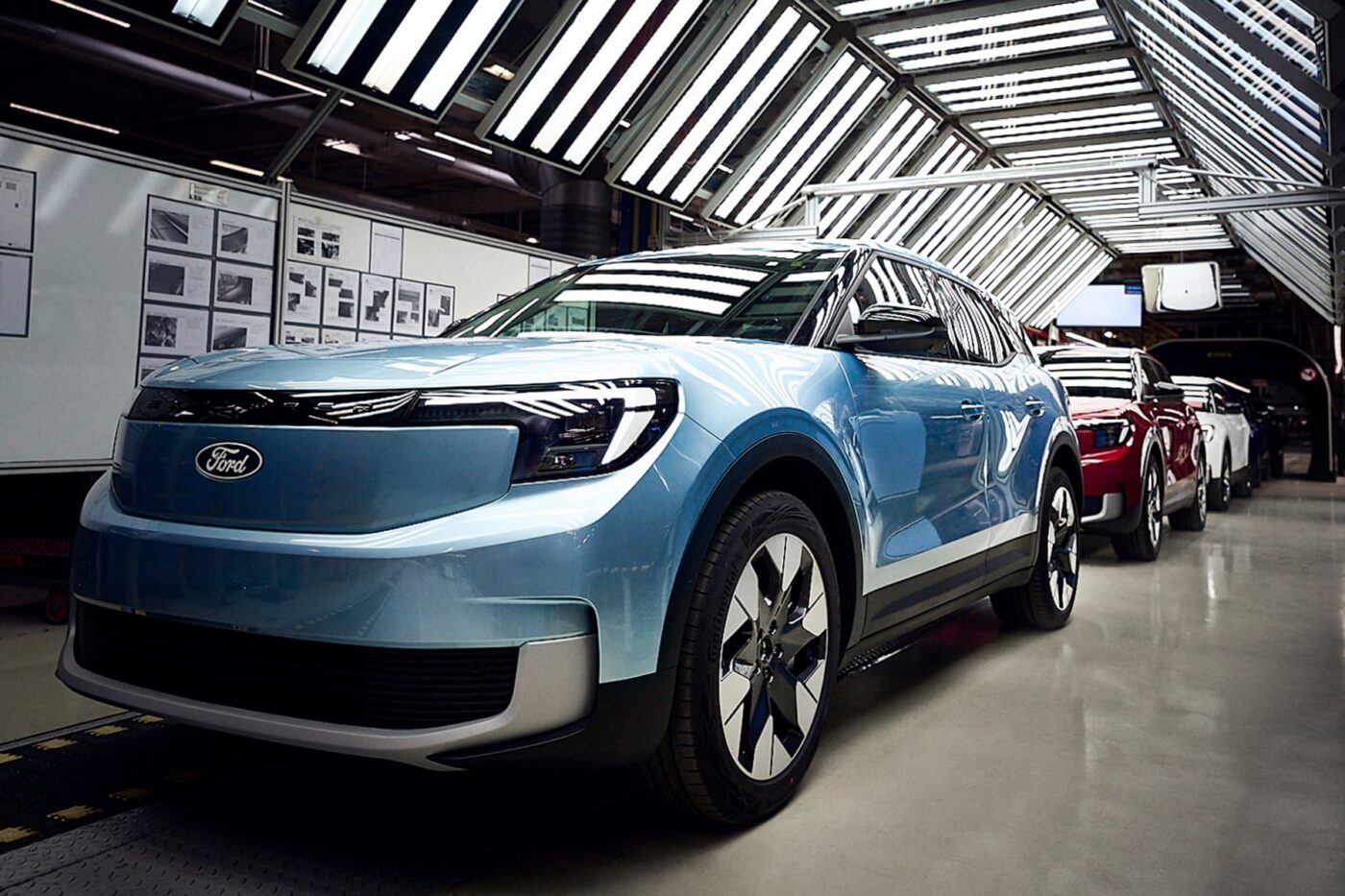
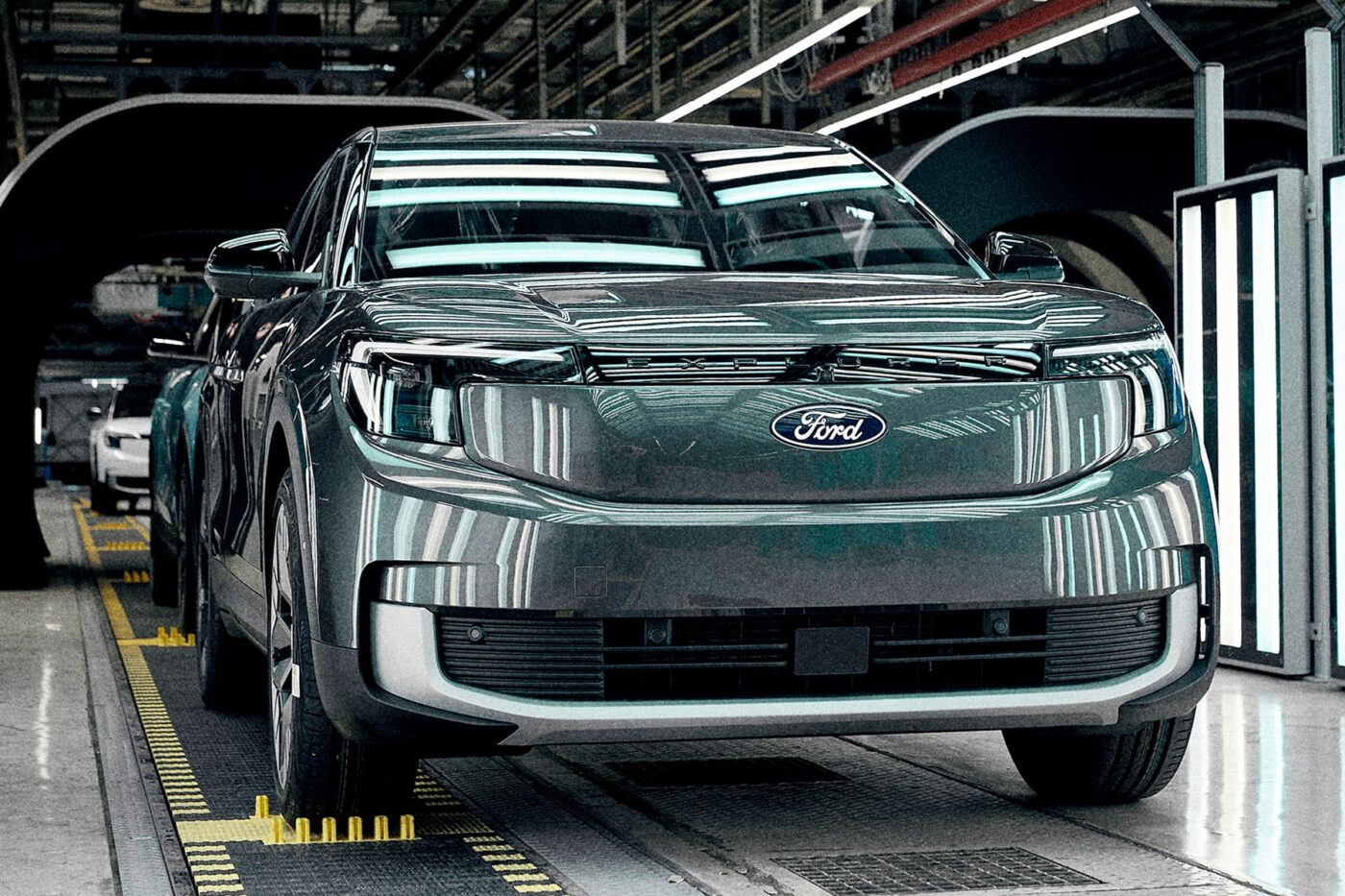
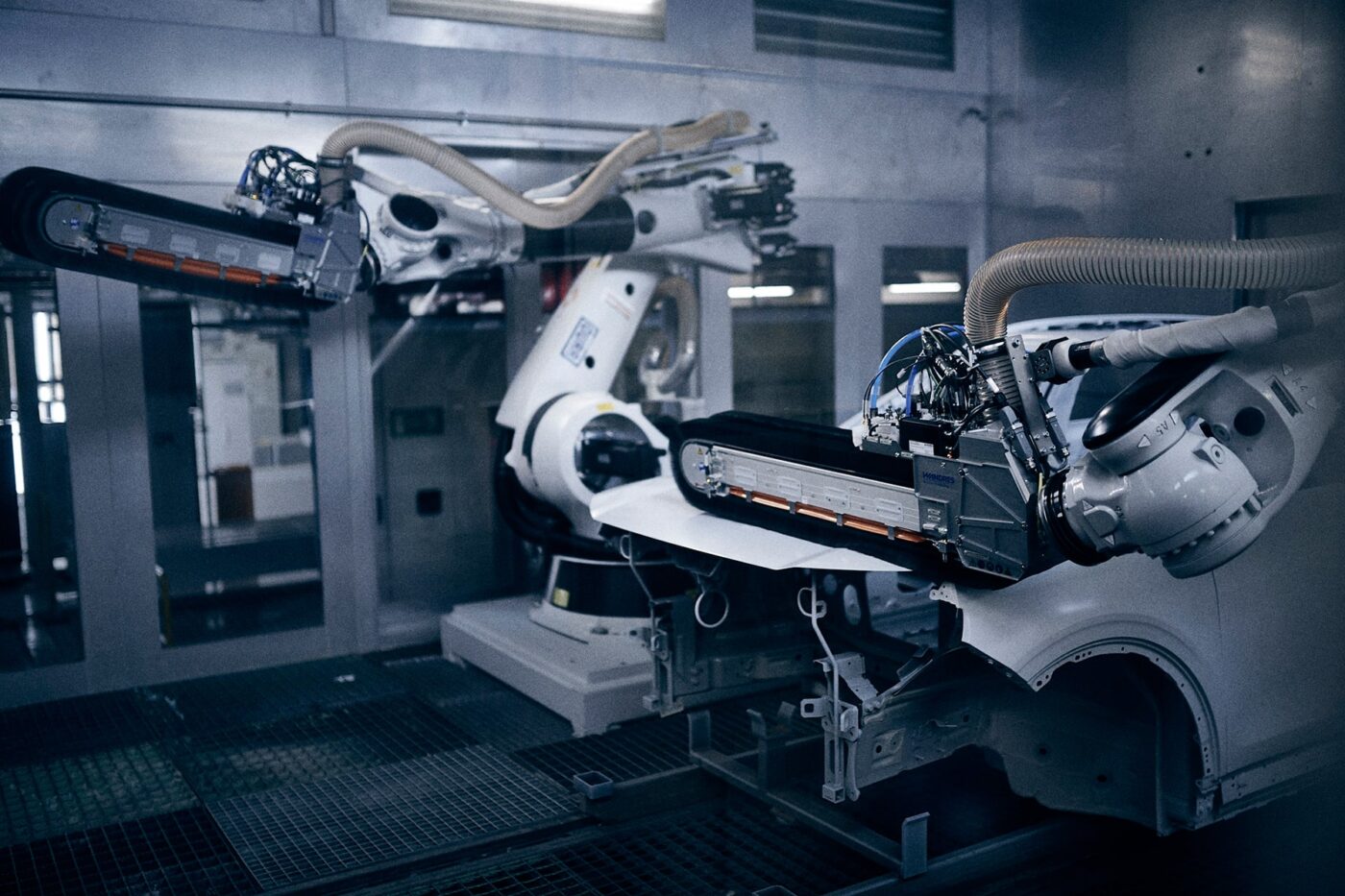
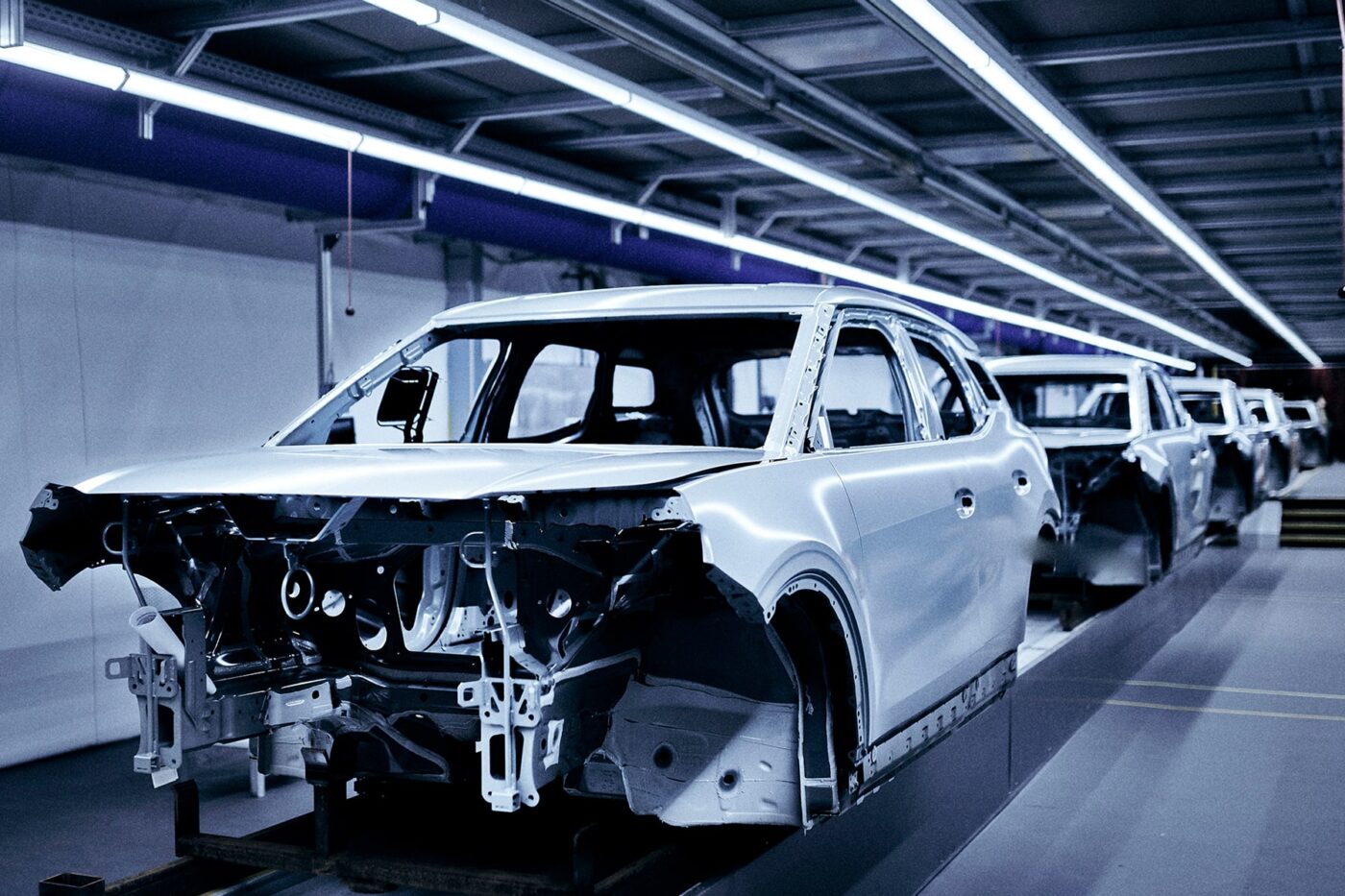
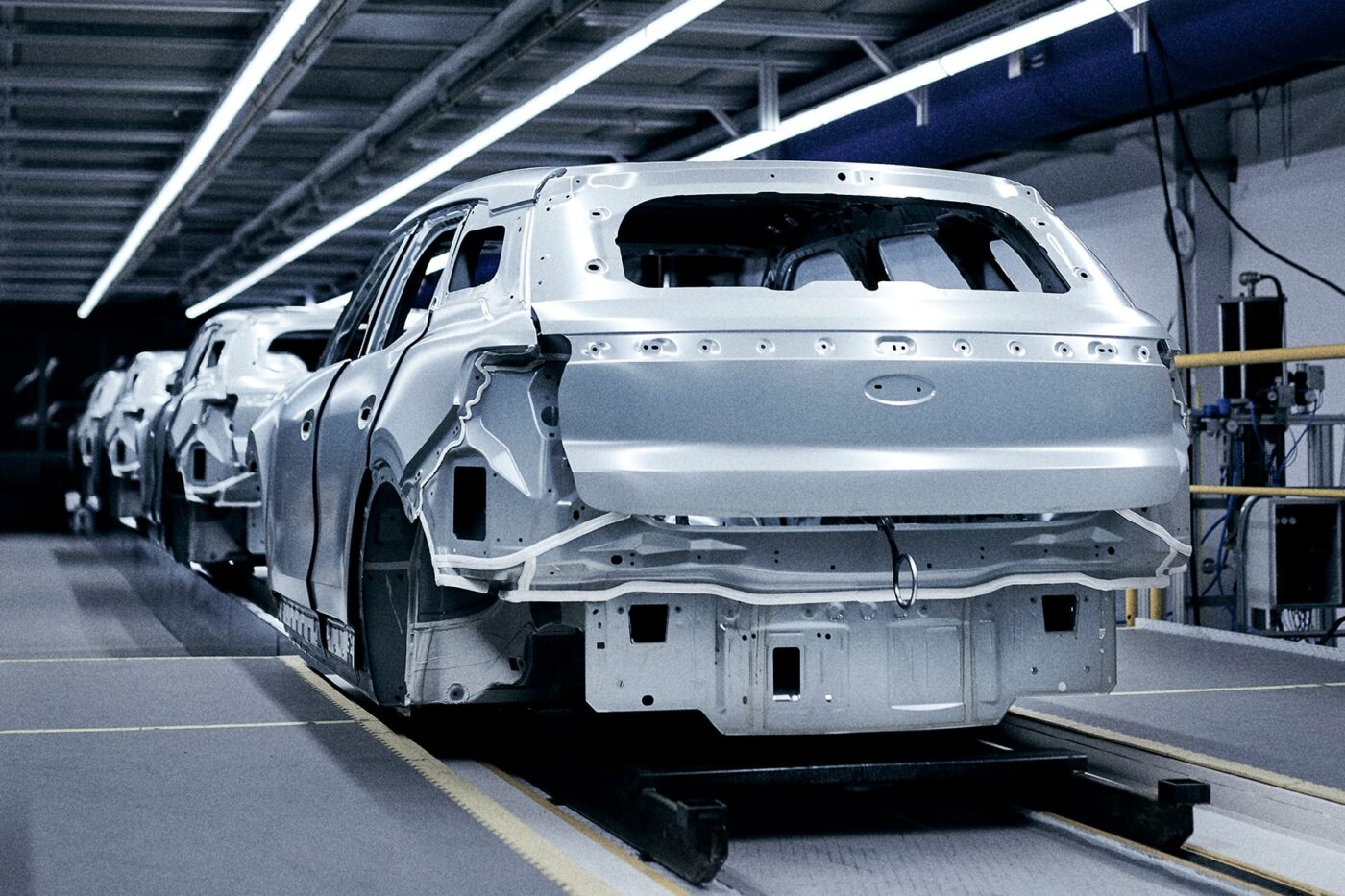
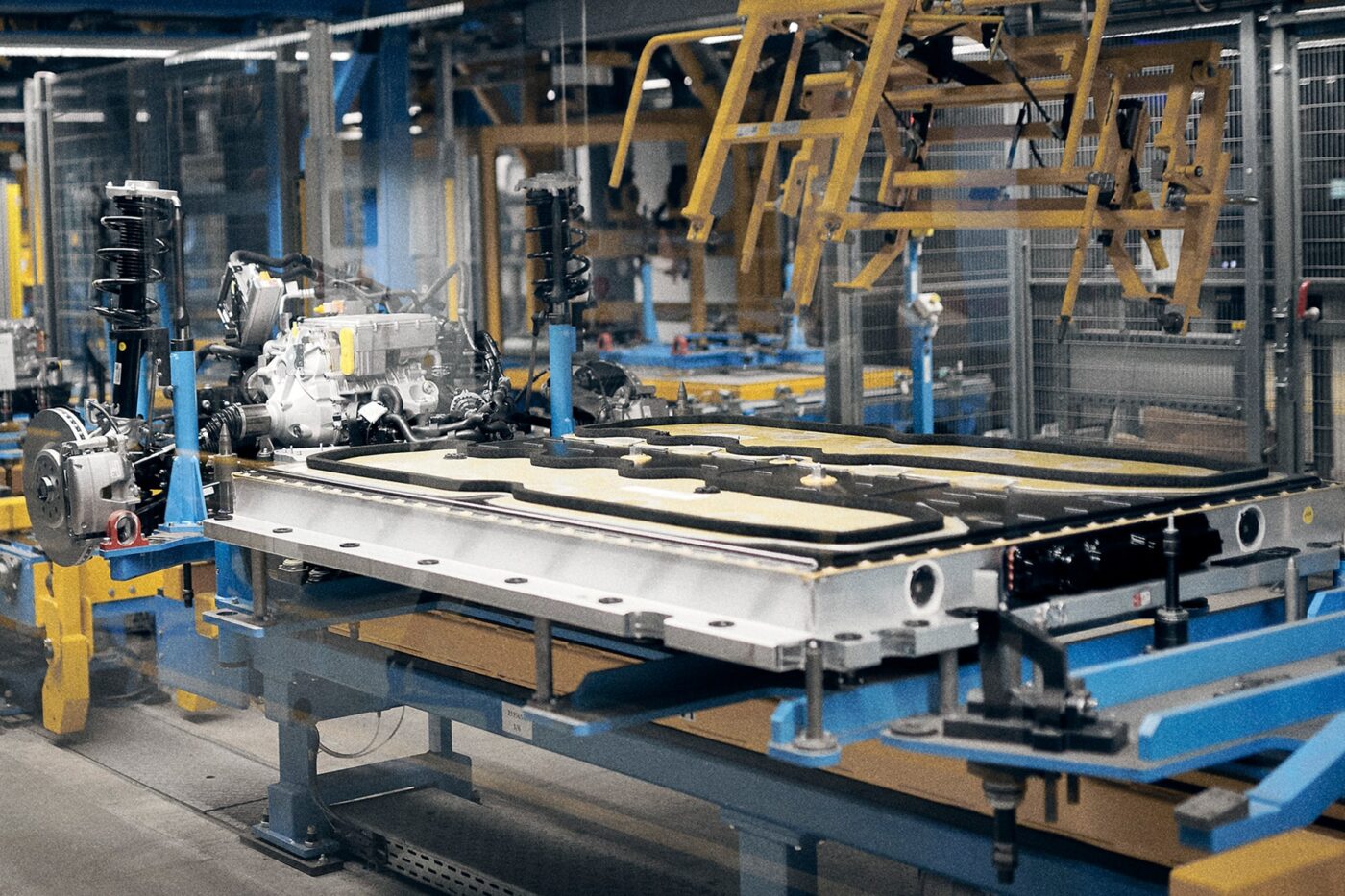
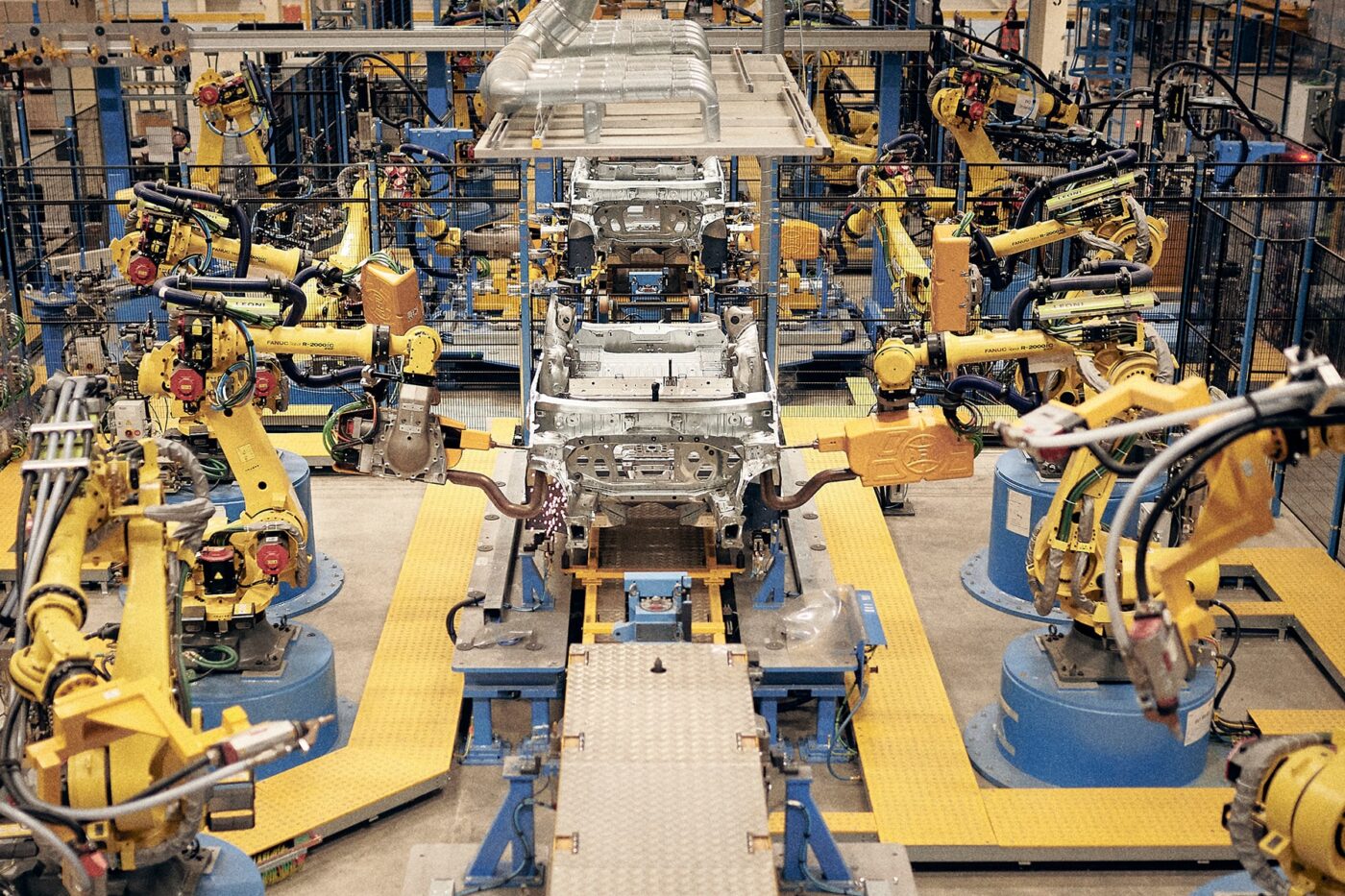
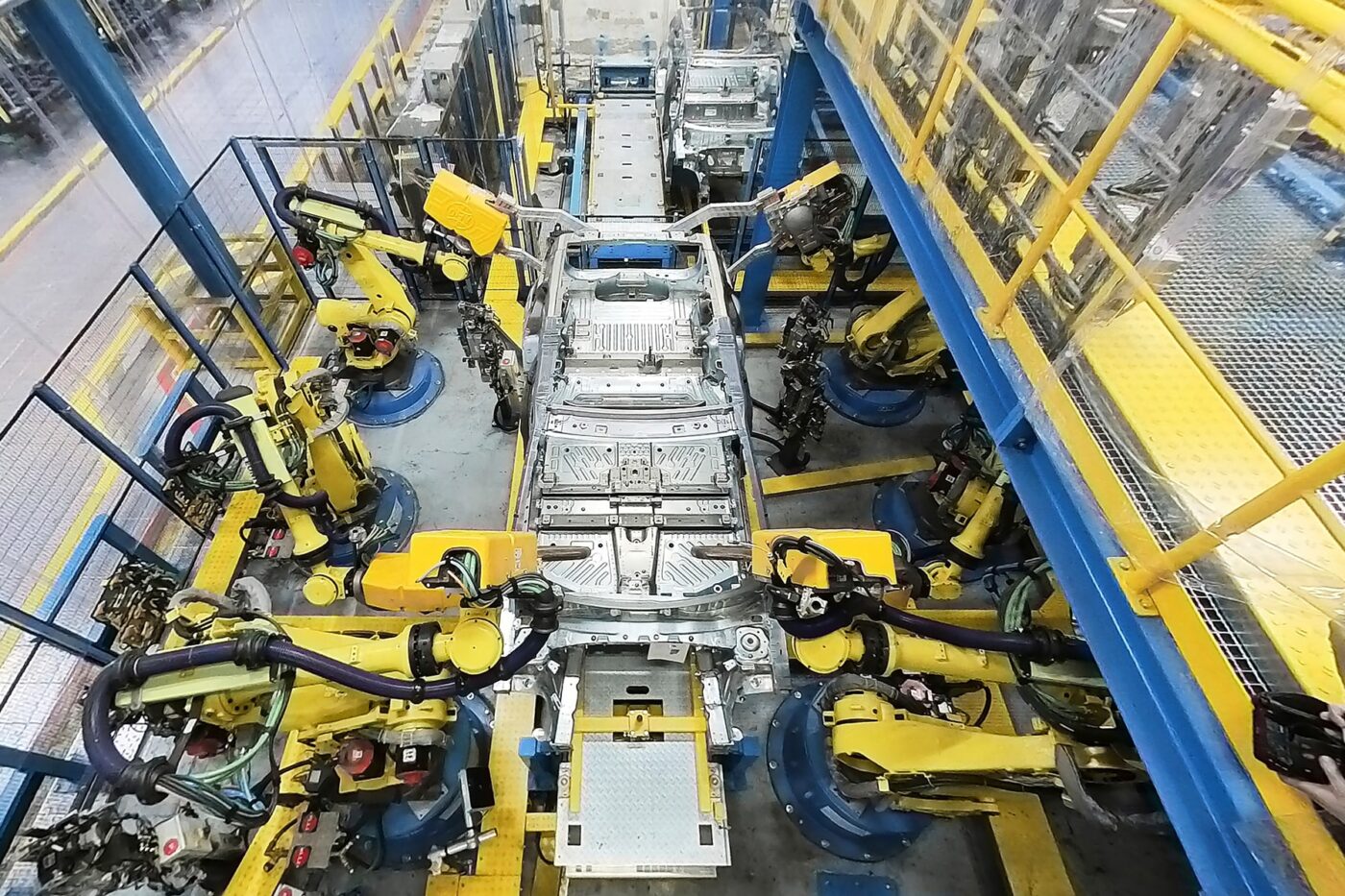
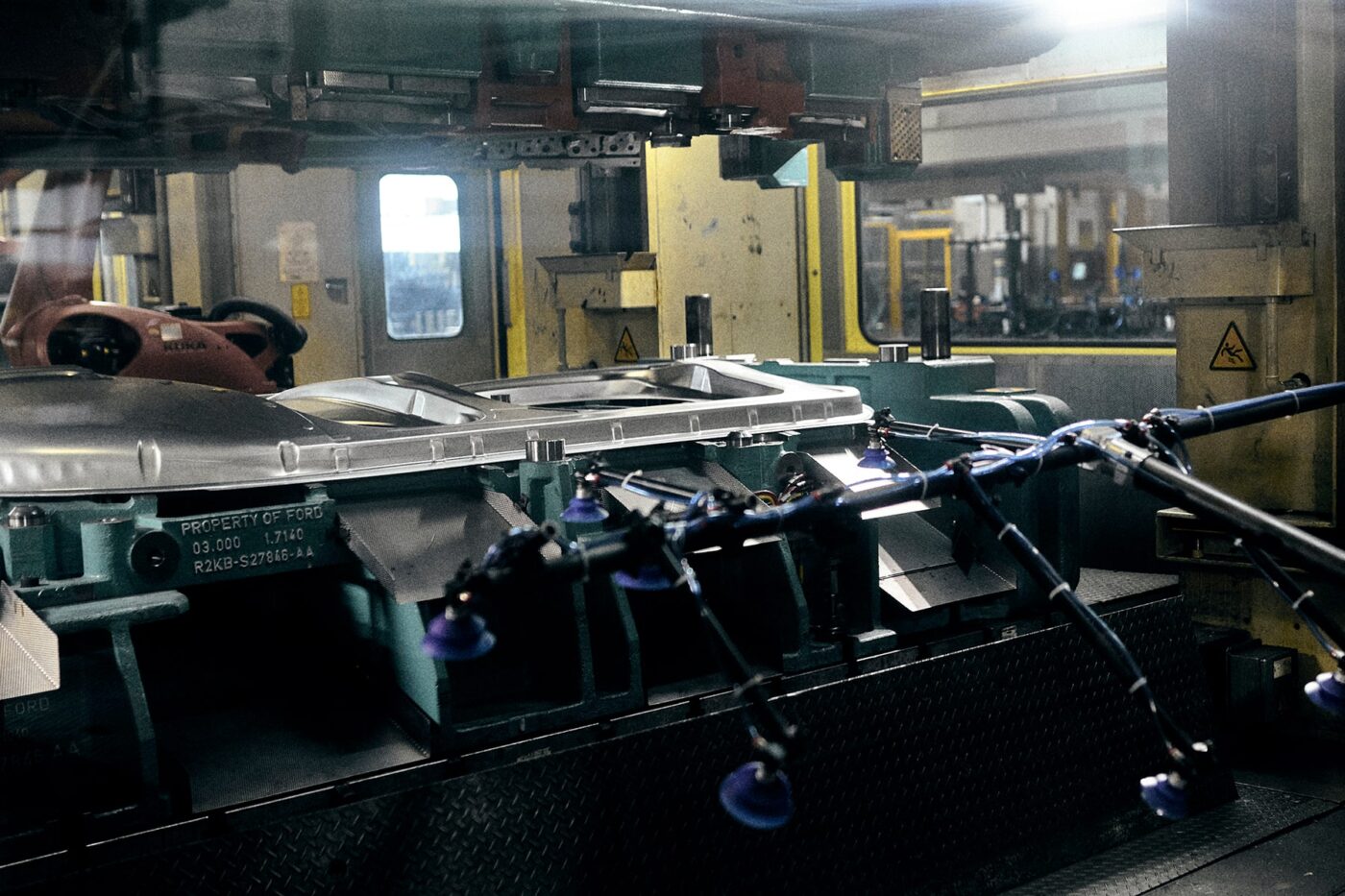
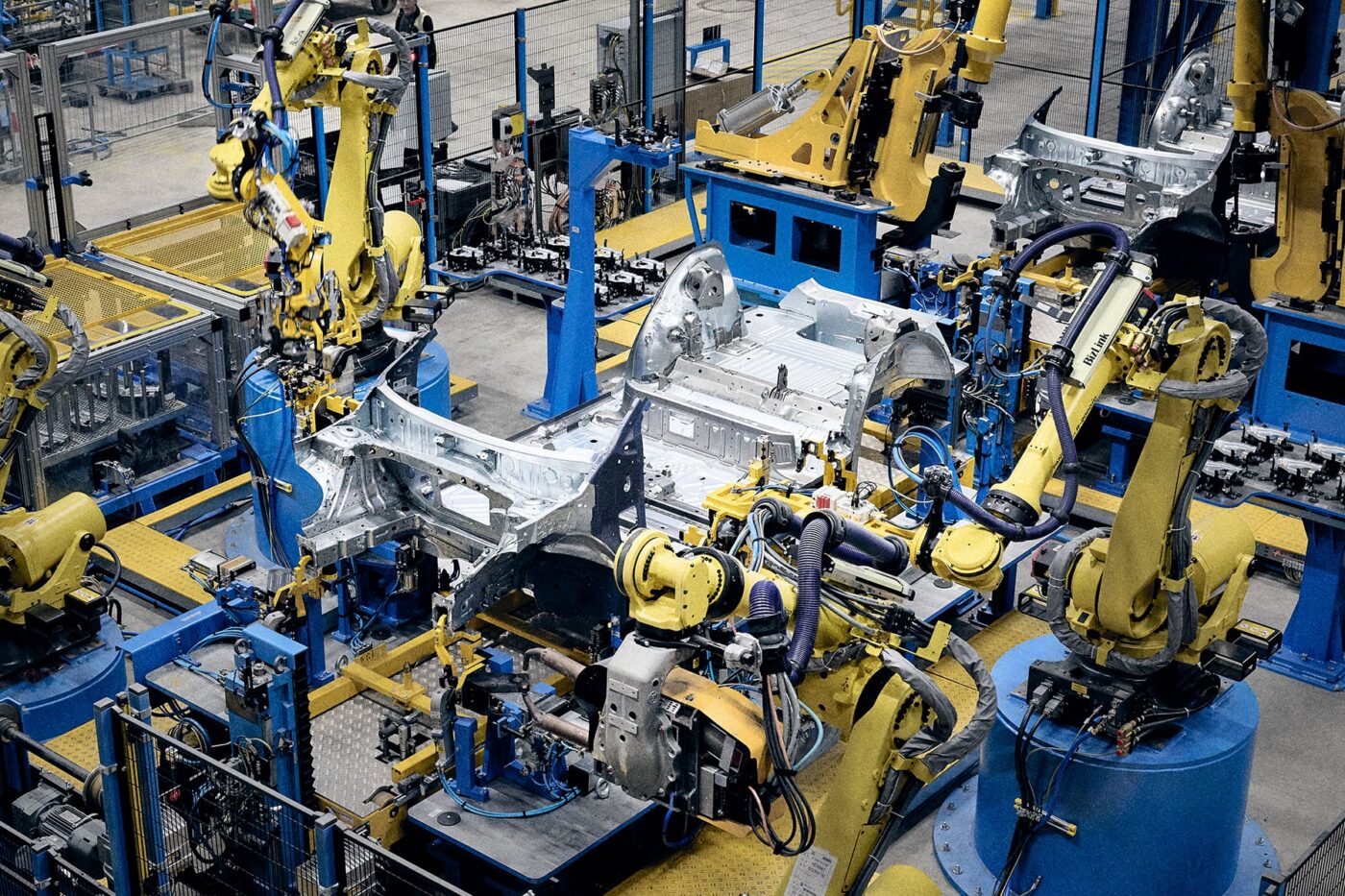
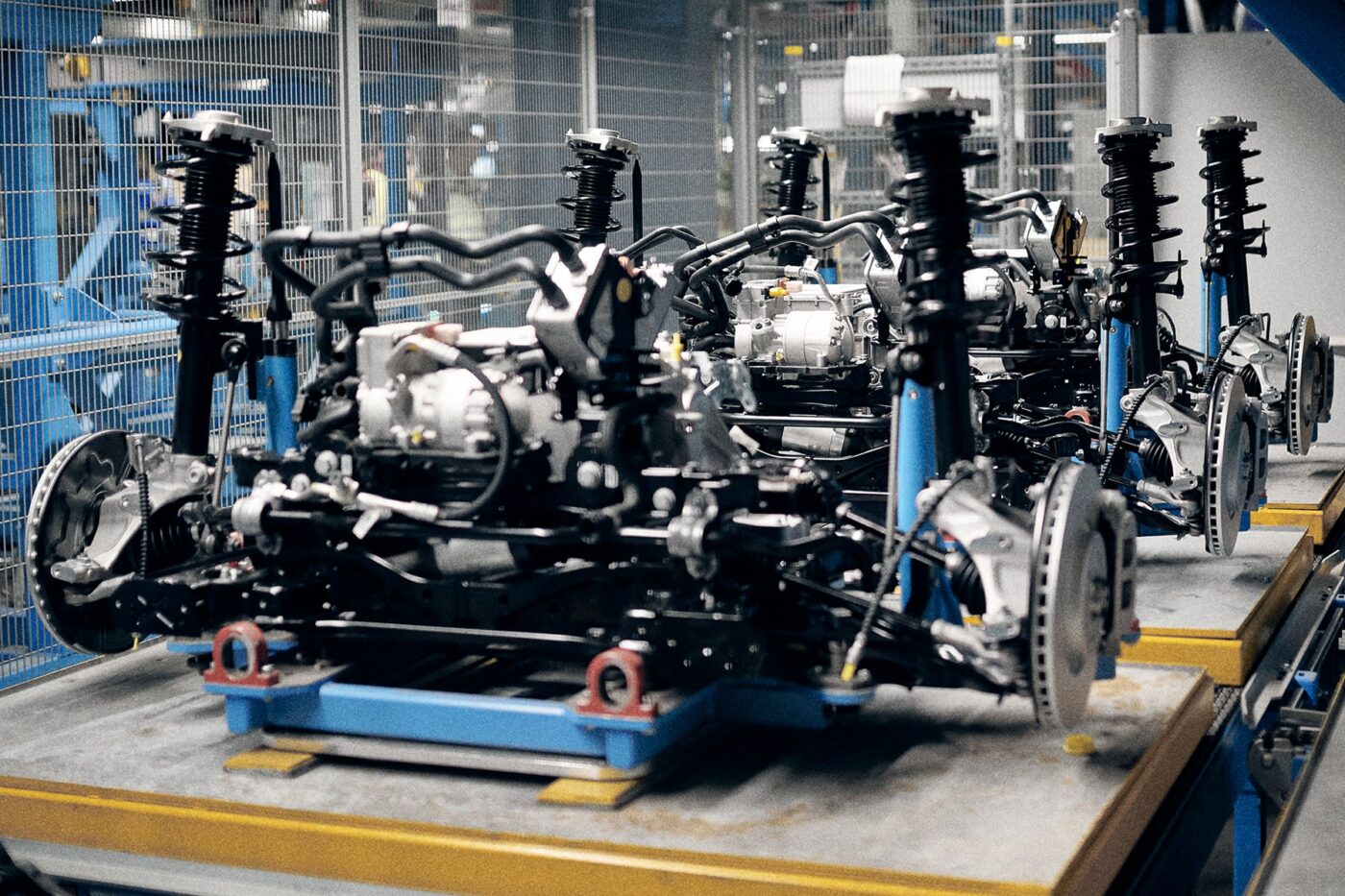
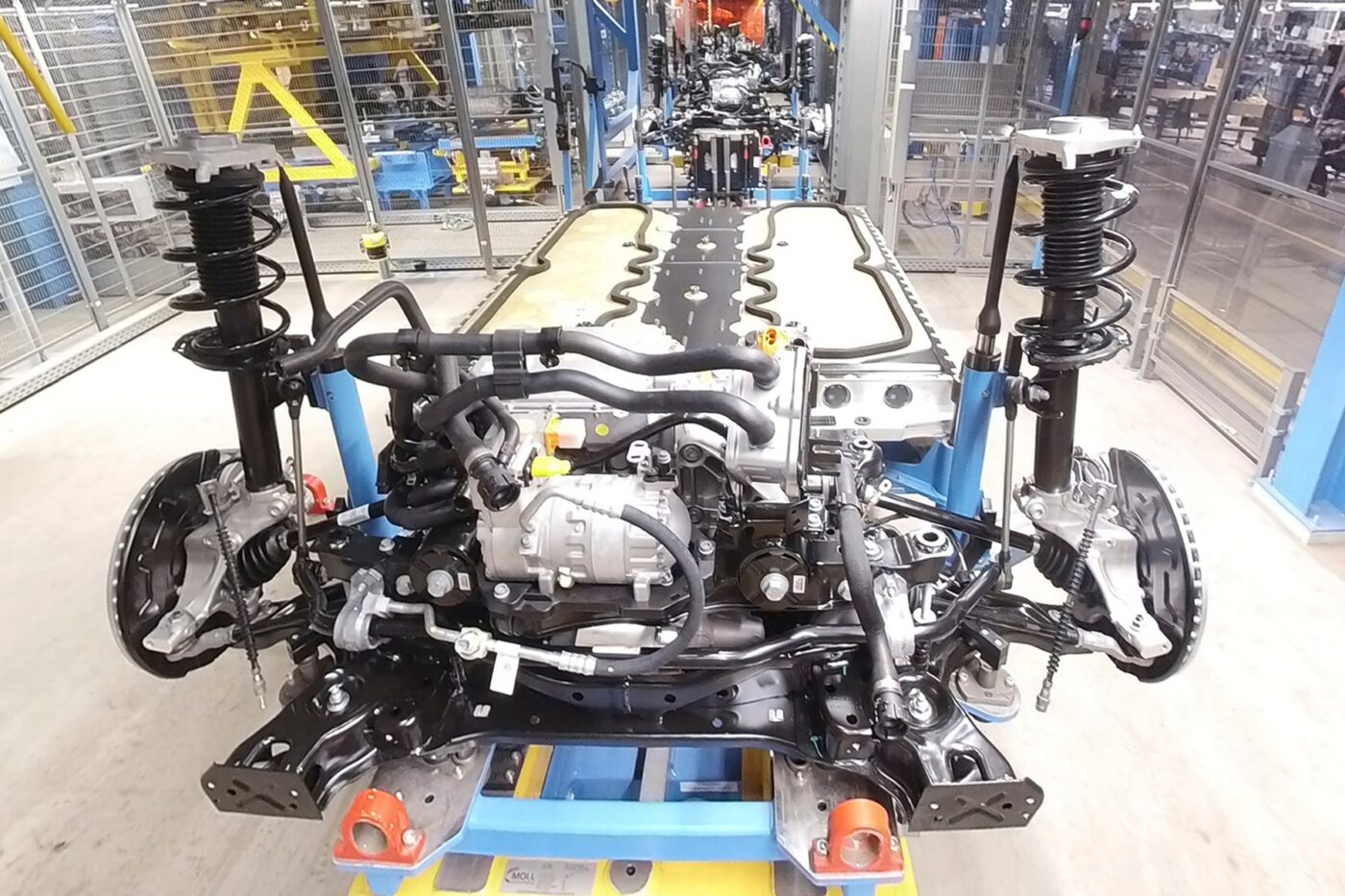
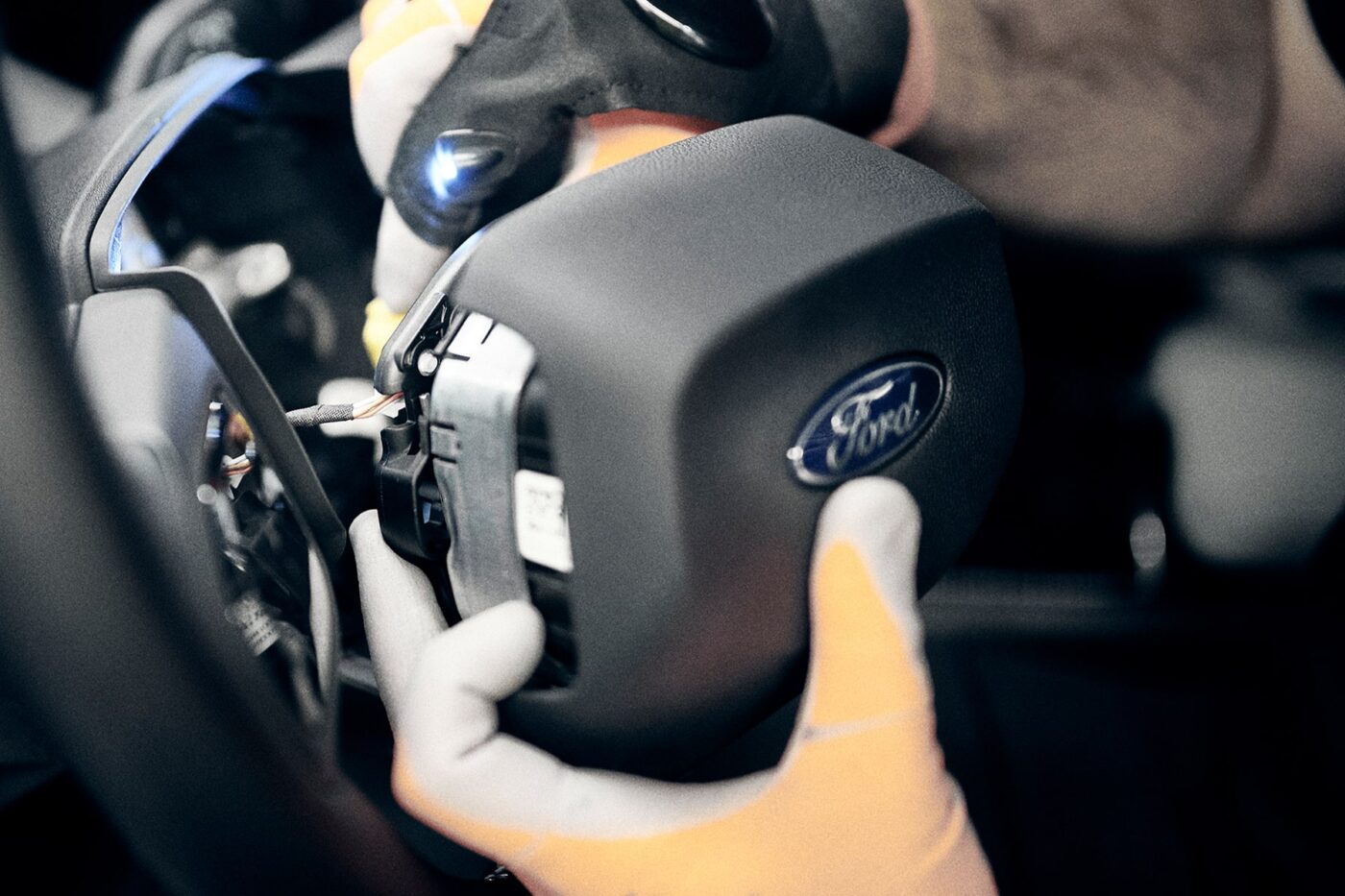
Die Produktion ist aber eine vorrangig deutsche Sache – der Prozess wurde von dem Kölner Produktionsteam in Zusammenarbeit mit mehreren Maschinen- und Anlagenbauern entworfen. Ein Beispiel: Für die Produktion der Elektromodelle hat Ford ein eigenes Mess-Zentrum in den Karosseriebau integriert. Zwar werden in der Fertigung selbst unzählige Produktionsschritte – bis hin zum Auftragen von Klebstoffen – komplett überwacht. In der Sekunde, in der der Roboter den Klebstoff aufträgt, kontrollieren aber mehrere Laser Dicke und Lage des Materials. Gibt es eine Abweichung, wird das Teil aussortiert und wird nachbearbeitet.
Zusätzlich zu diesen „In-Line“-Kontrollen werden pro Schicht mehrere Werkstücke in dem Mess-Zentrum genauer untersucht, zum Teil bis auf einen Tausendstel Millimeter. Dabei werden einzelne Bauteile, die Plattform oder auch der komplette „Body in White“, also die fertige, aber noch unlackierte Rohkarosse, mit Kameras und Lasern genau erfasst. Weichen die vermessenen Bauteile minimal vom Idealzustand ab – noch deutlich vor Erreichen der eigentlichen Fertigungstoleranz – kann das Mess-Team das erfassen und direkt an die jeweilige Station in der Fertigung weitergeben. So kann frühzeitig nachjustiert werden, auch wenn es nur um Zehntel-Millimeter geht. „Wir überwachen jeden Fertigungsschritt, vom Zusammensetzen der ersten Teile bis zum Herausrollen des fertigen Fahrzeugs, und erzielen so für unsere Kunden ein nie dagewesenes Qualitätsniveau“, erklärt Rene Wolf, Geschäftsführer Produktion Ford-Werke GmbH.
Aus zwei Montagelinien wird nur noch eine
Die Lackieranlage, in der die Rohkarossen gesäubert, versiegelt, grundiert und lackiert werden, ist ein Neubau. Der Explorer – obwohl mit 4,45 Metern etwas kürzer als die bekannten MEB-SUVs – ist schlichtweg größer als der zuvor in Köln gebaute Fiesta. Nur: Eine moderne Lackieranlage war gar nicht so leicht in den Standort zu integrieren. Das Kölner Ford-Werk wurde seit 1930 gebaut und ging 1931 in Betrieb – und auch bei den vorigen Umbauten galten noch ganz andere Maßstäbe und Vorgaben. Also musste eine alte Lagerhalle weichen – für einen 100 Meter langen, 25 Meter breiten und 25 Meter hohen Neubau. Auf drei Etagen sind Anlagen und Maschinen verbaut. Das 320.000 Liter große Tauchbecken für die galvanische Grundierung befindet sich etwa im Obergeschoss auf 18 Metern Höhe. Wärmetauscher, Lüfter und Filter sorgen dafür, dass möglichst viel Wärme im Gebäude bleibt und weiter genutzt werden kann – einige Prozesse finden bei bis zu 60 Grad statt, das Einbrennen der Grundierung erfolgt sogar bei 165 Grad. Schließlich soll das neue Werk zu den „effizientesten Fertigungsstätten von Ford weltweit“ zählen – auch den Wasserverbrauch konnte man senken, so das Unternehmen.
Die fertig lackierten Karosserien gehen dann in die Endmontage. Dabei handelt es sich zwar noch um die gleiche Halle, die aber innen komplett umgebaut wurde. Zu Fiesta-Zeiten gab es noch zwei identische Montagelinien, auf denen parallel gearbeitet wurde. Der Explorer und das zweite Modell werden nur noch auf einer Linie gebaut – das aber aufgeteilt in insgesamt sechs Bereiche.
Dass ein Elektroauto angeblich einfacher zu bauen ist, will man bei Ford so nicht direkt bestätigen, zumindest mit Blick auf die Endmontage. Denn viele Arbeitsschritte sind früher eben nicht in der Endmontage angefallen. Der Klimakompressor wurde früher über den Keilriemen des Verbrenners angetrieben und kam folglich bereits zusammen mit dem Motor fertig montiert in die Halle. Beim Elektroauto muss hingegen ein separater Klimakompressor montiert werden, ebenso die früher nicht vorhandene Wärmepumpe. Auch die Komplexität und Anzahl der Kühlsysteme ist gewachsen, entsprechend mehr Schläuche und Schellen müssen in der Endmontage angebracht und kontrolliert werden. „Für uns in der Endmontage war der Verbrenner eine Blackbox – das kam fertig an und musste nur noch eingebaut werden“, erklärt Jochen Bruckmann, Launch Leader Final Assembly. „Das Elektroauto mit der Batterie, den vielen Komponenten wie Pumpen und so weiter ist für uns komplexer.“
Das hat mehrere Folgen. Wie erwähnt gibt es in der Halle nur noch eine große statt zwei parallele Fertigungslinien. Und das Team in der Endmontage wurde von 780 Personen auf über 1.000 Leute vergrößert. Insgesamt arbeiten in Köln rund 3.300 Menschen in den verschiedenen Produktionsbereichen für die beiden Elektroautos. Zudem wurde am Ende der „Batterie-Linie“, auf der das Batteriepack sowie die Achsen mit dem bzw. den Antrieben und den unzähligen Kabeln und Kühlleitungen in die Plattform eingebaut werden, eine neue Qualitätssicherung aufgebaut. Kameras und Laser checken hier jede einzelne Plattform, bevor sie bei der „Hochzeit“ unter die Karosserie geschraubt wird. Eine künstliche Intelligenz wertet diese Daten aus und bewertet, ob alles korrekt vormontiert wurde. Das System kann dabei nicht nur erkennen, ob etwa ein Werkzeug auf dem Batteriegehäuse vergessen wurde, sondern auch erfassen, ob ein Stecker wirklich komplett eingesteckt ist oder nicht. Mit dieser KI-basierten Qualitätskontrolle soll verhindert werden, dass für Nacharbeiten die Plattform samt Batterie später nochmals vom Fahrzeug getrennt werden muss.
58 Schrauben beim E-Auto – sechs beim Fiesta
Und auch die Hochzeit selbst ist komplexer als bei einem Verbrenner. Beim Explorer wird der Unterbau mit Batterie, Antrieben und Fahrwerk mit 58 Schrauben am Fahrzeug befestigt, die alle in der richtigen Reihenfolge mit dem korrekten Drehmoment angezogen werden müssen. Das ist so aufwändig, dass dieser Arbeitsschritt inzwischen über fünf Stationen erfolgt, an denen jeweils vier Roboter die Schrauben anziehen. 20 Roboter an einer Station würden sich nur in die Quere kommen. Zum Vergleich: Beim Fiesta waren nur sechs Schrauben nötig – vier für die Vorderachse, zwei an der Hinterachse.
Den Produktionsprozess hat das Kölner Ford-Team selbst entworfen. Bruckmann und sein Team waren von Tag 1 an dabei, als die ersten Exemplare des Explorer von Hand zusammengeschraubt wurden. Dabei wurde jeder Handgriff erfasst, bewertet und optimiert, bis die komplexe Reihenfolge der Arbeitsstationen stand und die Stationen selbst an die Möglichkeiten in der bestehenden Halle angepasst waren. All das ist inzwischen ein digitaler Prozess, die gesamte Endmontage lässt sich auch in einem Meeting-Raum direkt neben der Montage über den digitalen Zwilling in Echtzeit verfolgen.
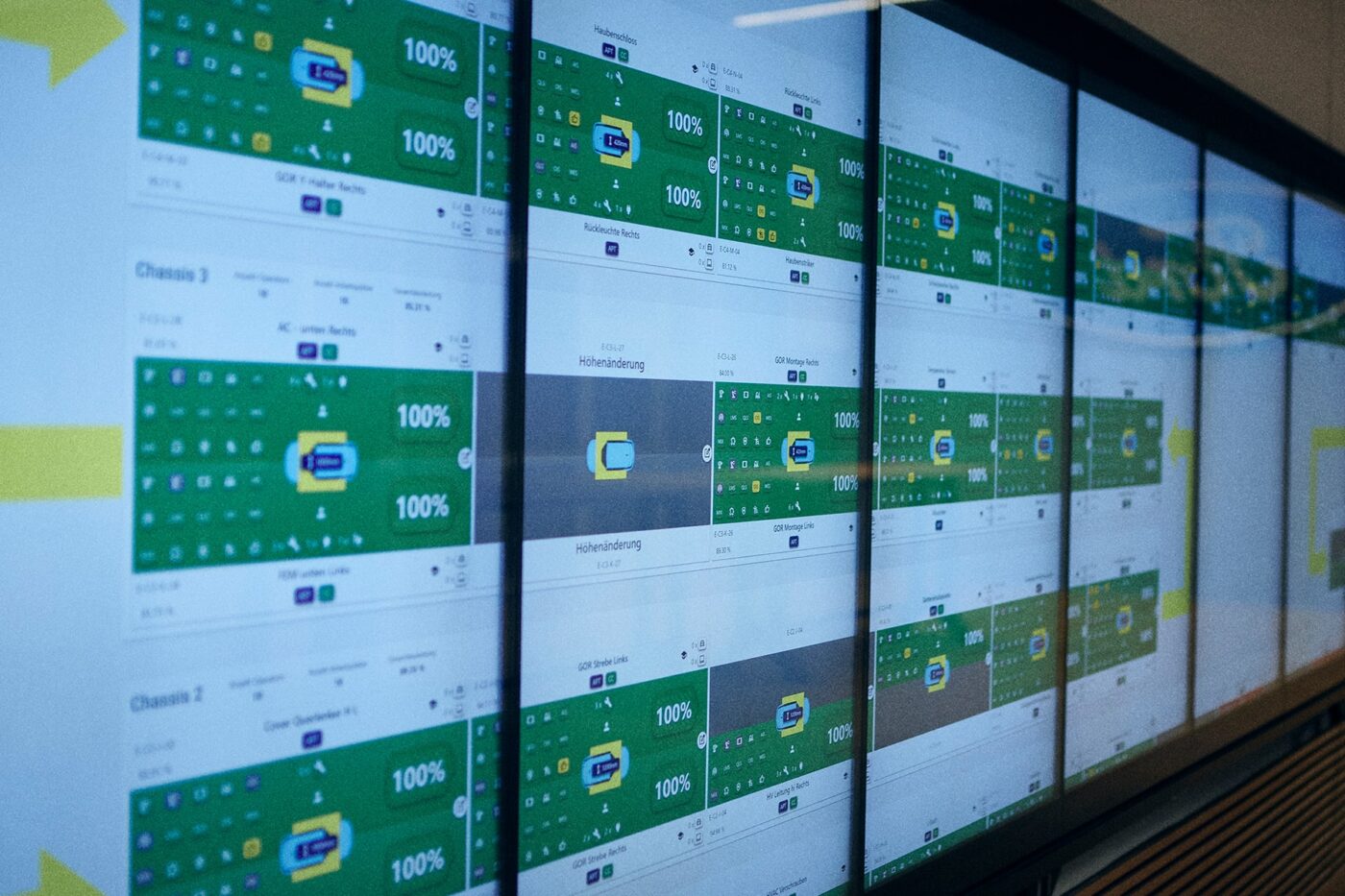
Dabei hat Ford kein Produktionssystem eingekauft, sondern die Software dahinter selbst entwickelt, wie Tobias Sender, Leiter der Endmontage, im Gespräch mit electrive erklärt. Egal ob über die mehr als zehn Meter breite Touchscreen-Anordnung in dem Meeting-Raum oder über das Smartphone, der Zustand jeder Station lässt sich so verfolgen – bis hin zur Zufriedenheit der Mitarbeiter vor Ort. „Zufriedene Mitarbeiter liefern gute Qualität“, so Sender. Werden die Bedingungen an einer Station von dem Personal schlechter bewerten, können Sender und sein Team direkt eingreifen. Die eigens entwickelte Software soll künftig auch außerhalb der Endmontage eingesetzt werden. „Auch in der neuen Batteriemontage setzen wir das System ein, bevor wir es dann in weitere Ford-Werke weltweit ausrollen“, erklärt der Manager.
Wenn alles ideal läuft, können künftig bis zu 250.000 Exemplare der beiden Modelle in Köln jedes Jahr vom Band laufen. Zum Beginn der Serienproduktion sind es natürlich noch weniger Fahrzeuge, aktuell peilt Ford 150 bis 250 Explorer je Tag an. Nach dem Ramp-up sollen es aber schon 640 Autos pro Tag werden.
Wie viele Vorbestellungen es für den neuen Explorer gibt, will Fords Geschäftsführer Marketing und Handel in der DACH-Region, Christian Weingärtner, zwar nicht genau nennen, zeigt sich aber grundsätzlich „ganz zufrieden“. „Wir haben uns hier die Markteinführung des Puma zum Vorbild genommen, weil wir mit dem Puma auch eine neue Baureihe gelauncht haben, wo Ford zuvor kein Angebot hatte. Und derzeit liegen wir beim Explorer über den Zahlen des Puma“, sagt Weingärtner. Der Manager verweist aber auch auf die Bedeutung des Zeitpunkts, weil der große Schub beim Explorer erst noch kommen soll, wenn das Fahrzeug auch bei den Händlern im Showroom steht.
Kleine Batterie kommt noch in diesem Jahr
Und im Handel sieht Weingärtner eine „ganz andere Basis als bei der Markteinführung des Mustang Mach-E“. Bei Fords erstem E-SUV war alles noch neu. Der Explorer aus Köln tritt jedoch eine Preisklasse darunter an und soll eine viel größere Kundschaft ansprechen. Der Explorer ist seit Ende März zu Preisen ab 42.500 Euro bestellbar, wobei das Modell mit der kleinen Batterie zum genannten Basispreis erst gegen Jahresende auf den Markt kommt. „In diesem Segment greift der Großteil der Kunden zur größeren Batterie“, erklärt Weingärtner. „Bei Elektroautos sehen wir, dass das Leasing wichtiger ist als der Barkauf. Und in der Leasingrate macht die größere Batterie keinen so großen Unterschied.“
Einen großen Unterschied für Ford wird es allerdings machen, ob der Explorer und das kommende Crossover-Modell im Markt einschlagen oder nicht. Denn ein Verbrenner-Modell, mit dem bei schwankender Elektro-Nachfrage das Werk ausgelastet werden könnte, gibt es bei Ford nicht mehr.
7 Kommentare