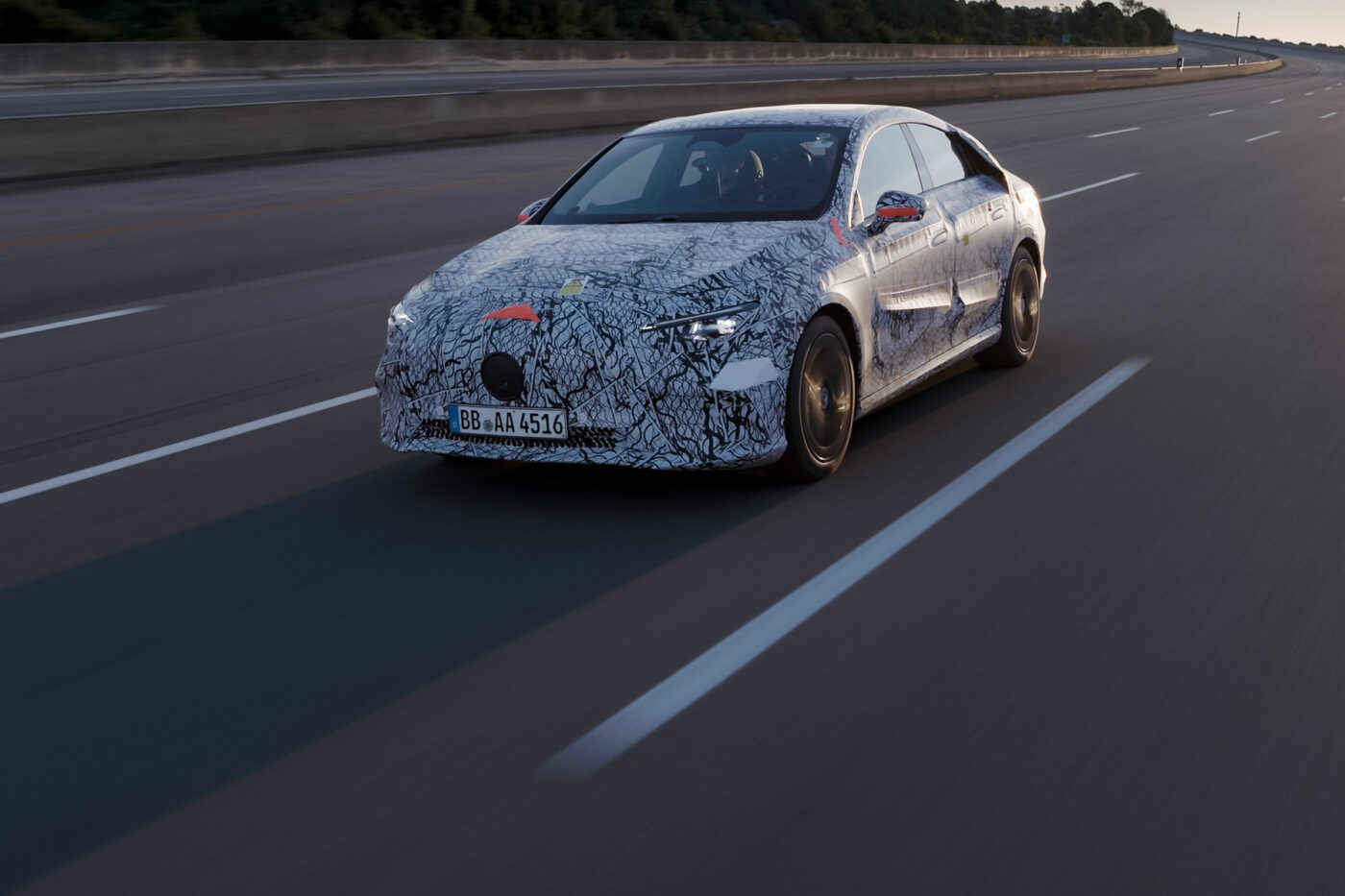
Deep Dive MMA: Wie Mercedes beim Elektro-CLA mit Effizienz punkten will
Zugegeben, schon mit dem EQS und der betont aerodynamischen Karosserie des Elektro-Flaggschiffs hat Mercedes einen gewissen Wert auf die Effizienz gelegt. Bei einem über 2,6 Tonnen schweren Luxus-Gefährt mit in der Spitze bis zu 560 kW Leistung von Effizienz zu sprechen, ist aber relativ. Und klar ist auch: Gerade auf dem für Luxuslimousinen wichtigen Markt in China hat das ursprüngliche Konzept des EQS nicht gut gezogen.
Der kommende CLA, der auf der Mercedes Modular Architecture (MMA) basiert, soll ungleich erfolgreicher werden. Die kompakte Limousine bildet im nächsten Jahr den Auftakt für die kommende Kompakt-Modellfamilie der Stuttgarter, die für hohe Stückzahlen sorgen soll. Dass die MMA nicht in einer neuen A-Klasse debütiert, hat einen einfachen Grund: Das Modell-Portfolio wird radikal aussortiert, Nachfolger der A- und B-Klasse wird es nicht geben. Sondern eben jenen CLA, einen zugehörigen Shooting Brake als dynamischen Kombi und zwei SUV-Modelle – ein mal etwas dynamischer im Stile des GLA/EQA und einmal kantiger mit mehr Platz und Nutzwert wie der GLB/EQB.
Doch noch geht es nicht um die Details zu den vier Modellen, zu den Fahrzeugen will sich Mercedes noch nicht weiter äußern. Der Autobauer hatte vielmehr zu einem Technik-Workshop rund um die MMA ins Werk Sindelfingen geladen, konkret in das „Electric Software Hub“, wo ein Großteil der Entwicklungsarbeit rund um die neue Plattform stattfand. Infos zu den Antrieben, einige Aussagen zu den Batterien und zur Art und Weise, wie die MMA entstanden ist, will Mercedes mit der Öffentlichkeit teilen. Die Details zum CLA wird es im kommenden Jahr zur Weltpremiere geben. Einen Einblick, was in dem Auto stecken wird, gibt es aber schon jetzt.
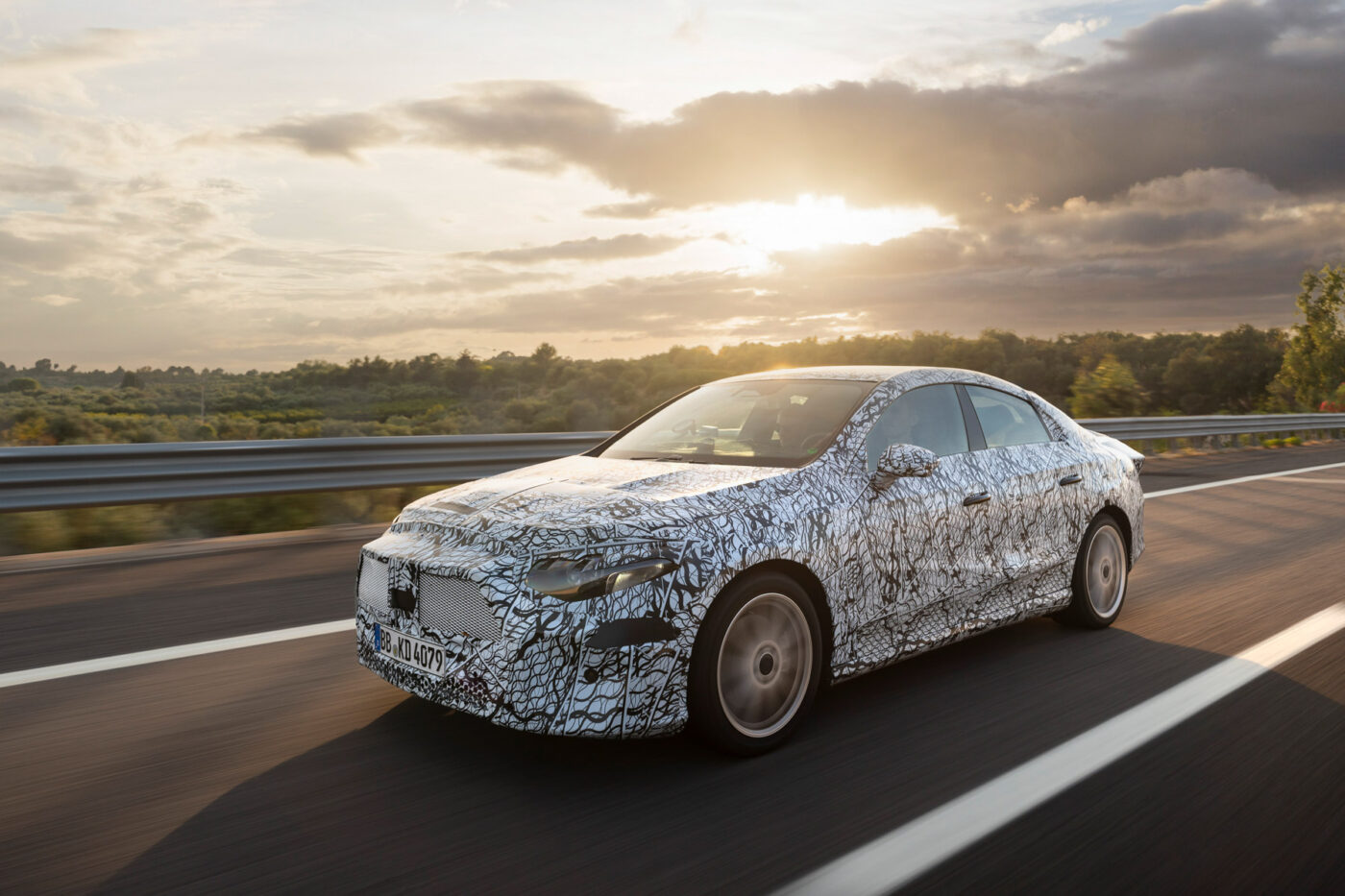
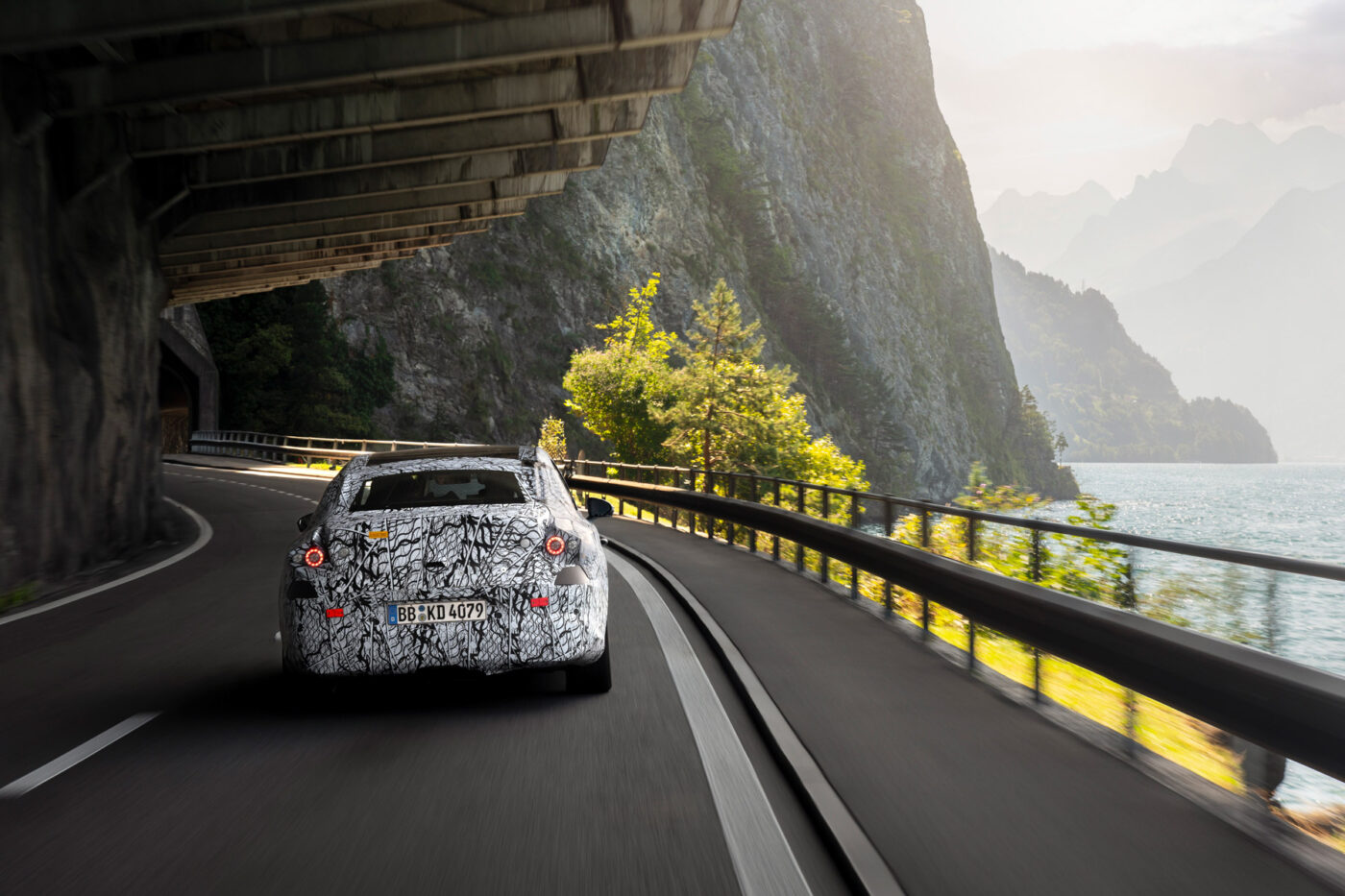
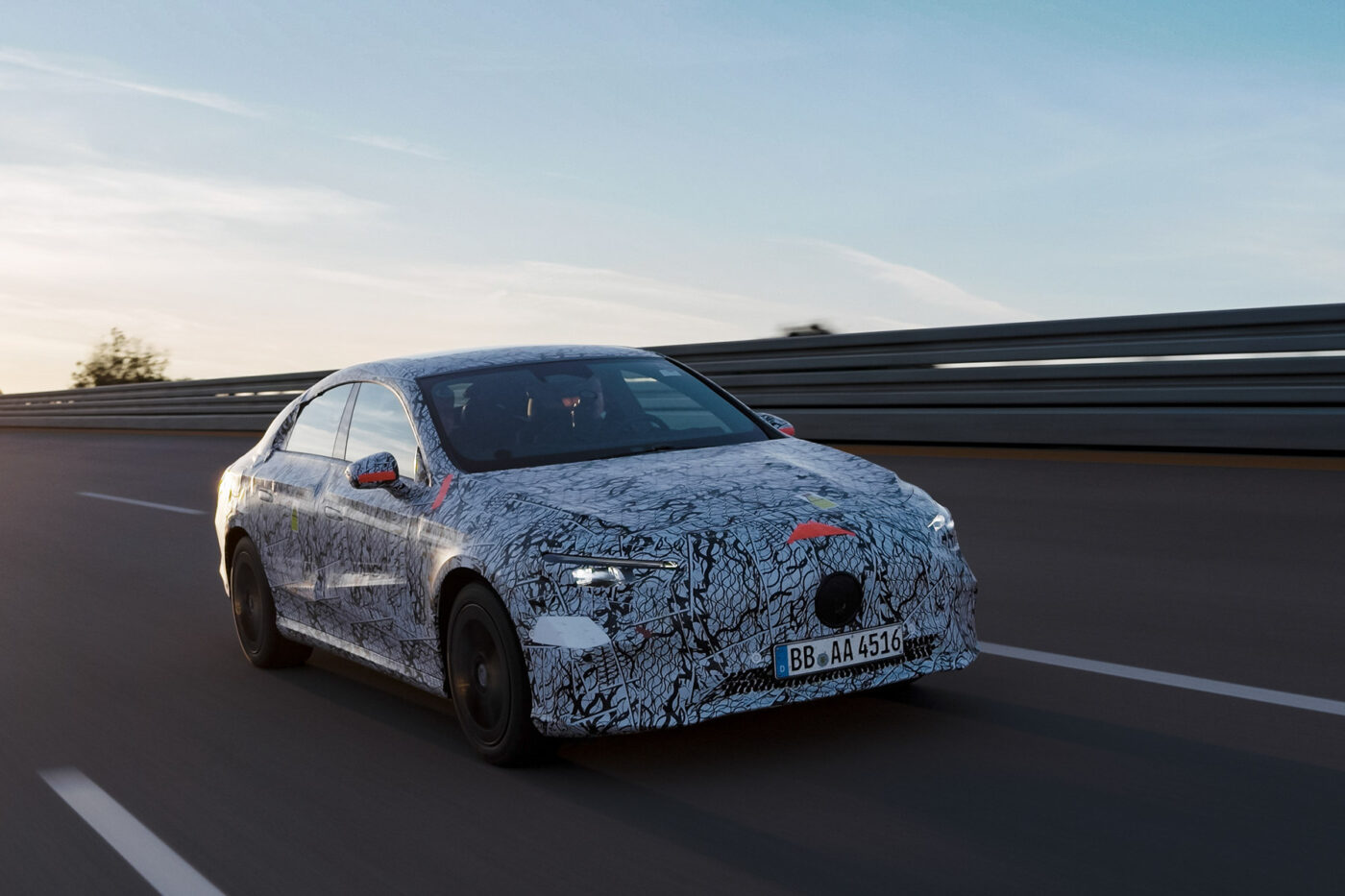
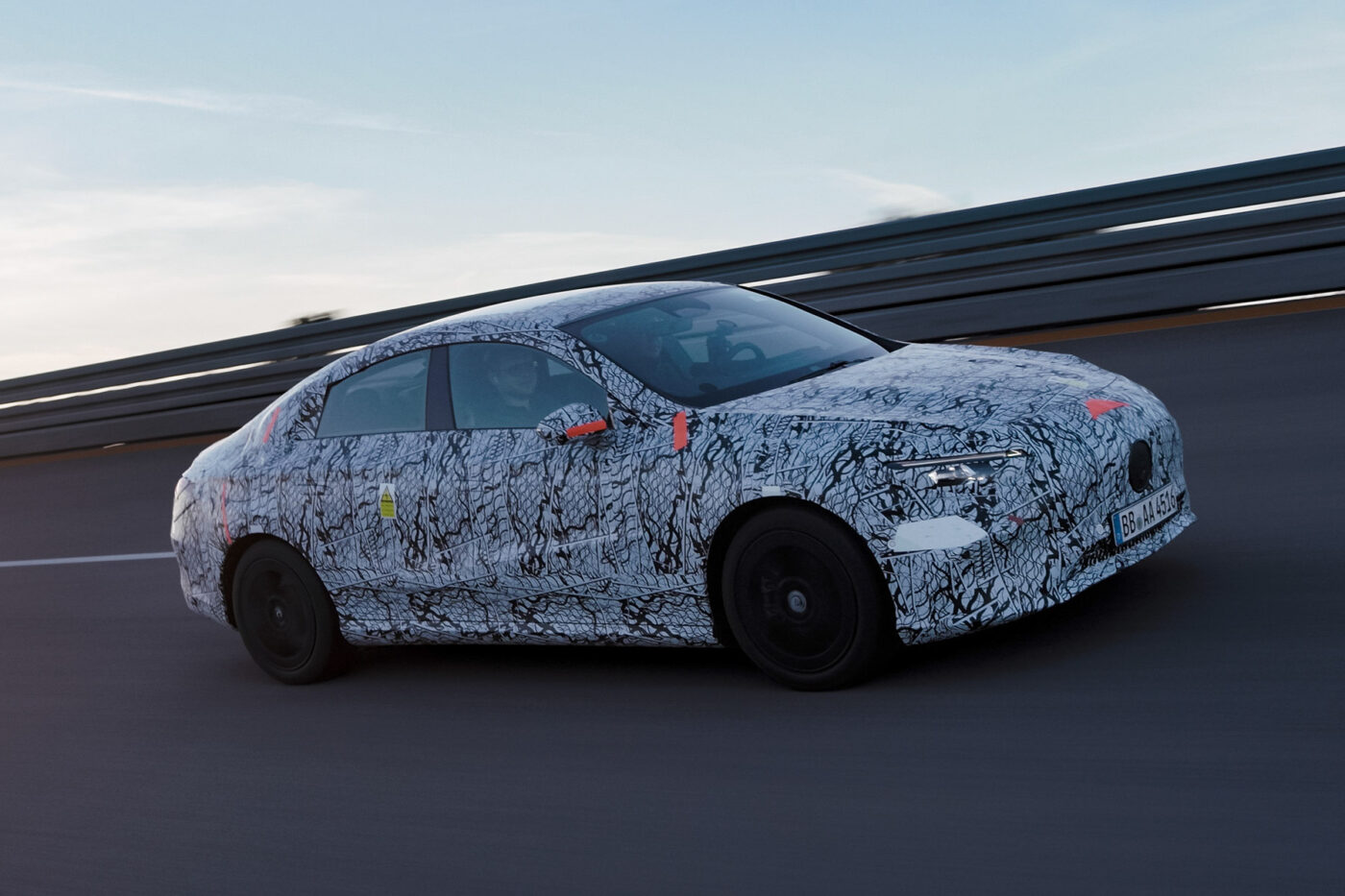
Dreh- und Angelpunkt der Entwicklung ist das Thema Effizienz. Wie Torsten Eder, Vice President Entwicklung Elektrifizierte Antriebe, in seinem Vortrag erläutert, hatte sein Team dabei nicht nur die klassische Energieeffizienz im Blick, sondern auch etwas, was man bei Mercedes „Zeiteffizienz“ nennt. Denn aus Kundensicht geht es eben vor allem darum, möglichst schnell am Ziel anzukommen – sei es nun durch eine hohe Reichweite dank des effizienten Antriebs, durch kurze Ladezeiten oder eine intelligente Ladeplanung. Alles spielt eine Rolle.
Bei Mercedes ist man sich sehr sicher, damit genau richtig zu liegen. „Die Effizienz wird unserer Meinung nach den Unterschied machen bei künftigen Elektromodellen“, sagt Eder. Und: „Effizienz ist die neue Währung.“
An diesem Satz werden sich der CLA und alle weiteren Elektro-Mercedes messen lassen müssen. Für den MMA-Erstling ist ein Verbrauch von 12 kWh/100 Kilometern angesagt. Wie das erreicht werden soll, zeigen die folgenden Kapitel.
Der Antrieb
Im CLA kommt die neue eATS 2.0 zum Einsatz. Dieser „elektrische Antriebsstrang 2.0“ (auch englisch MB.EDU 2.0 genannt) ist eine Art Elektromotoren-Familie – im CLA wird das erste von vier „Familienmitgliedern“ verbaut, wie Eder erklärt. Dabei handelt es sich um einen hochintegrierten Elektromotor, den Mercedes nicht nur selbst entwickelt hat, sondern auch im Stammwerk Untertürkheim selbst baut.
Direkt ein kleines Aber: Nur der Elektromotor an der Hinterachse ist eine solche eATS 2.0. Der zweite E-Motor, der bei der Allrad-Variante an der Vorderachse verbaut wird, ist zwar auch nach Mercedes-Vorgaben entwickelt worden, stammt aber von einem Zulieferer.
Bei der eATS 2.0 handelt es sich um eine permanenterregte Synchronmaschine (PSM). Die Peak-Leistung liegt bei 200 kW, die Antriebseinheit selbst ist sehr kompakt verbaut und soll so einen großen und tiefen Kofferraum ermöglichen. Die Leistungselektronik (vorne und hinten kommen SiC-Halbleiter zum Einsatz) wird etwa an der Vorderseite des Gehäuses platziert, nicht mehr oben. Die PSM kommt trotz der Dauermagnete „so gut wie“ ohne seltene Erden aus, wie Christian Pfeffer, Projektleiter für Serienentwicklung des CLA-Antriebsstrangs, erklärt. Erreicht wurde das durch Hairpin-Wicklungen im Stator und eine Doppel-V-Anordnung der Dauermagnete im Rotor.
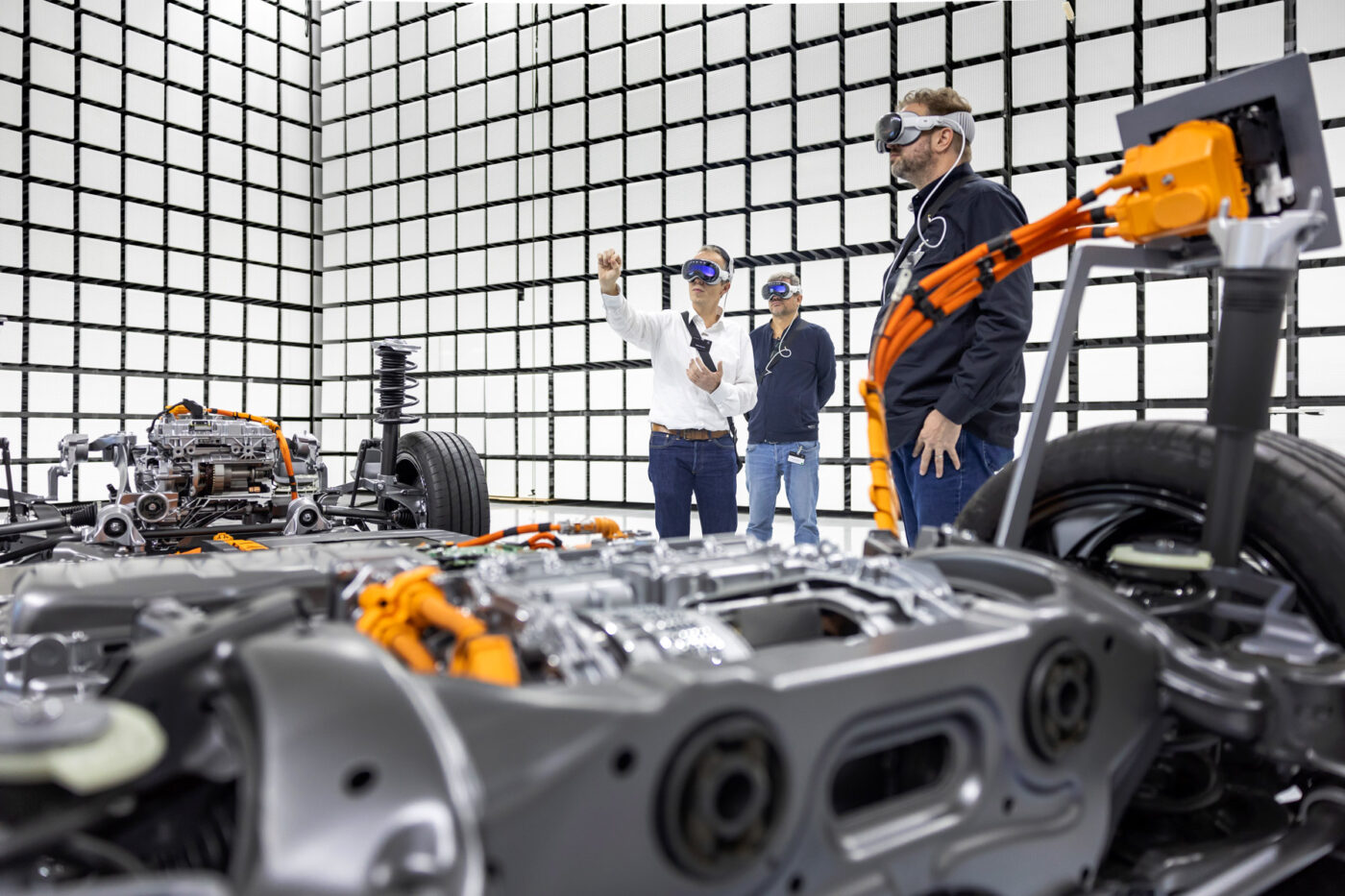
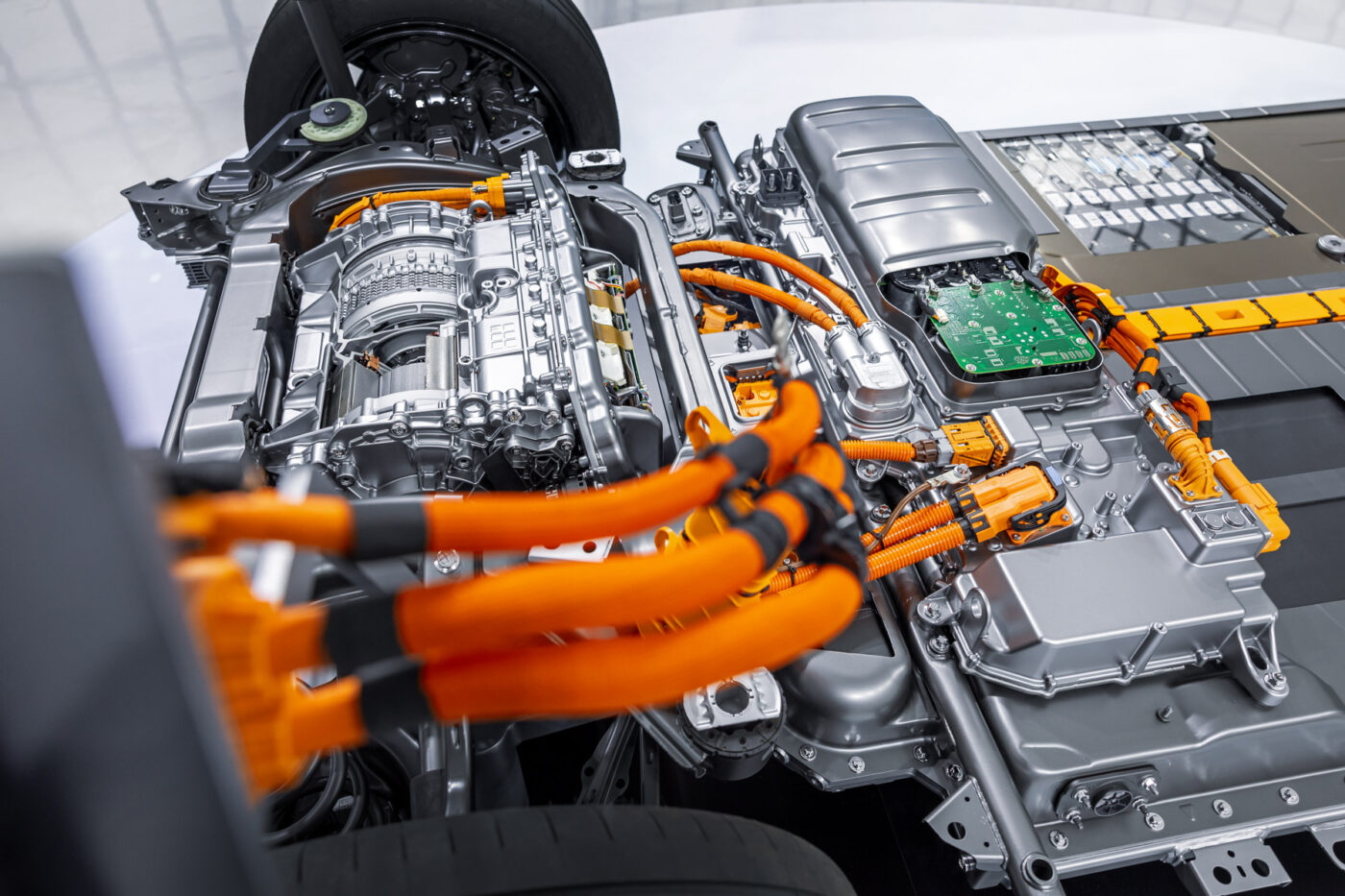
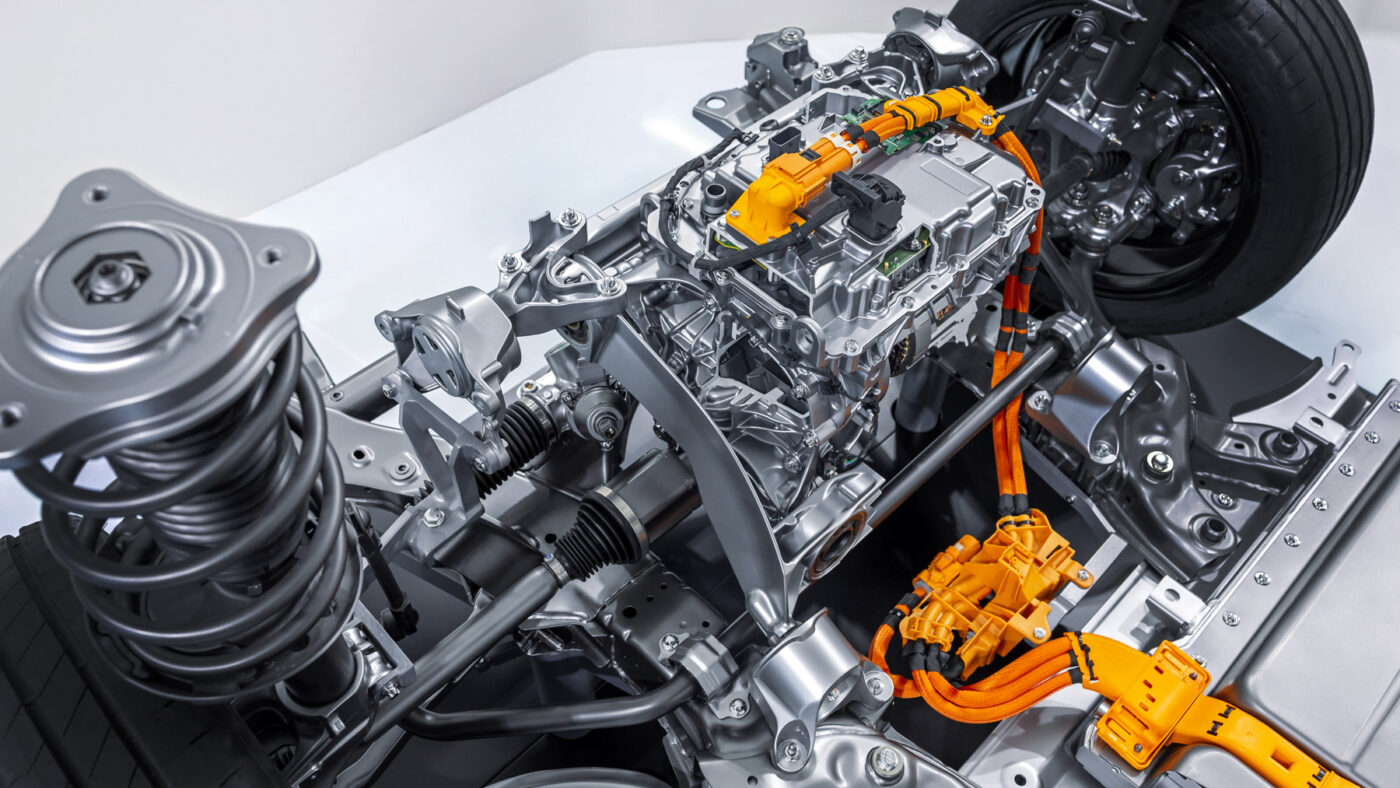
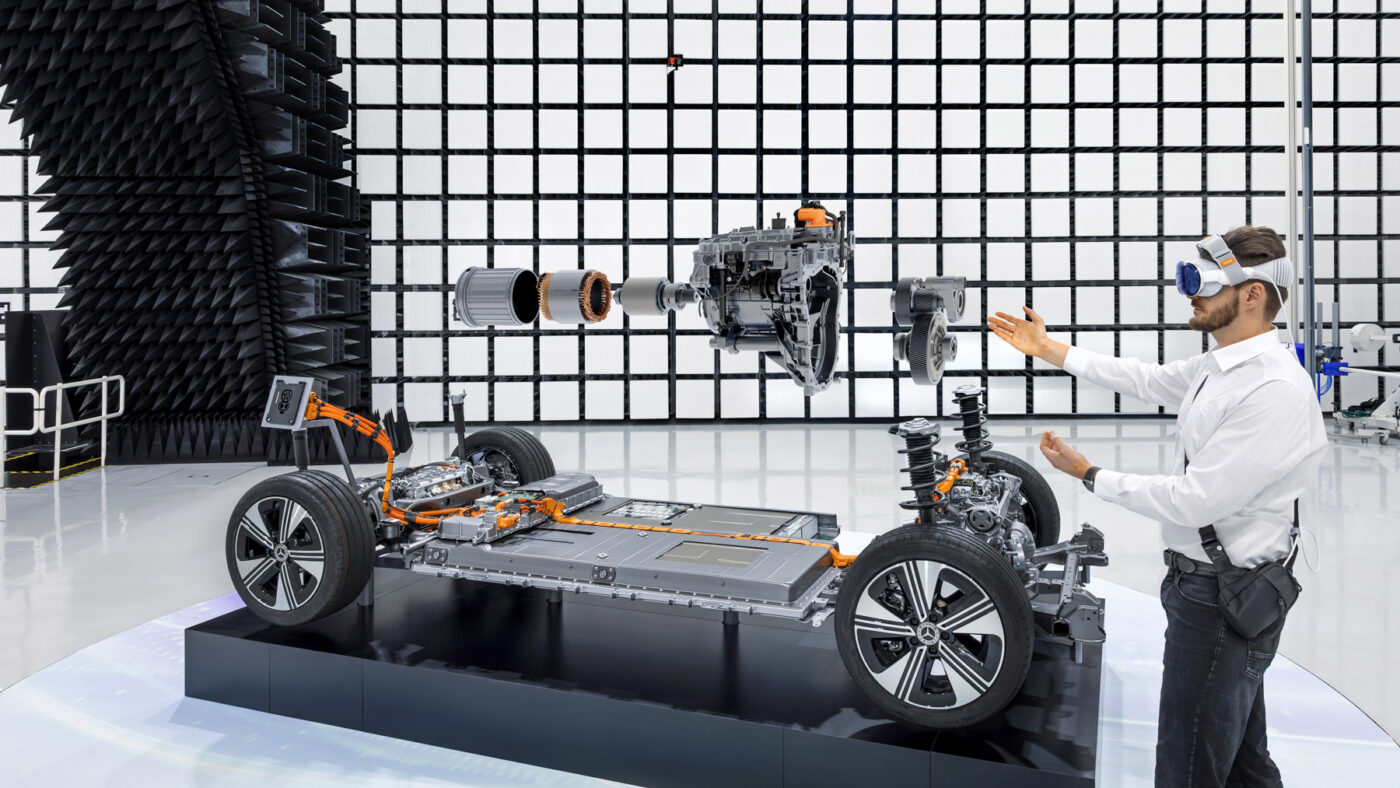
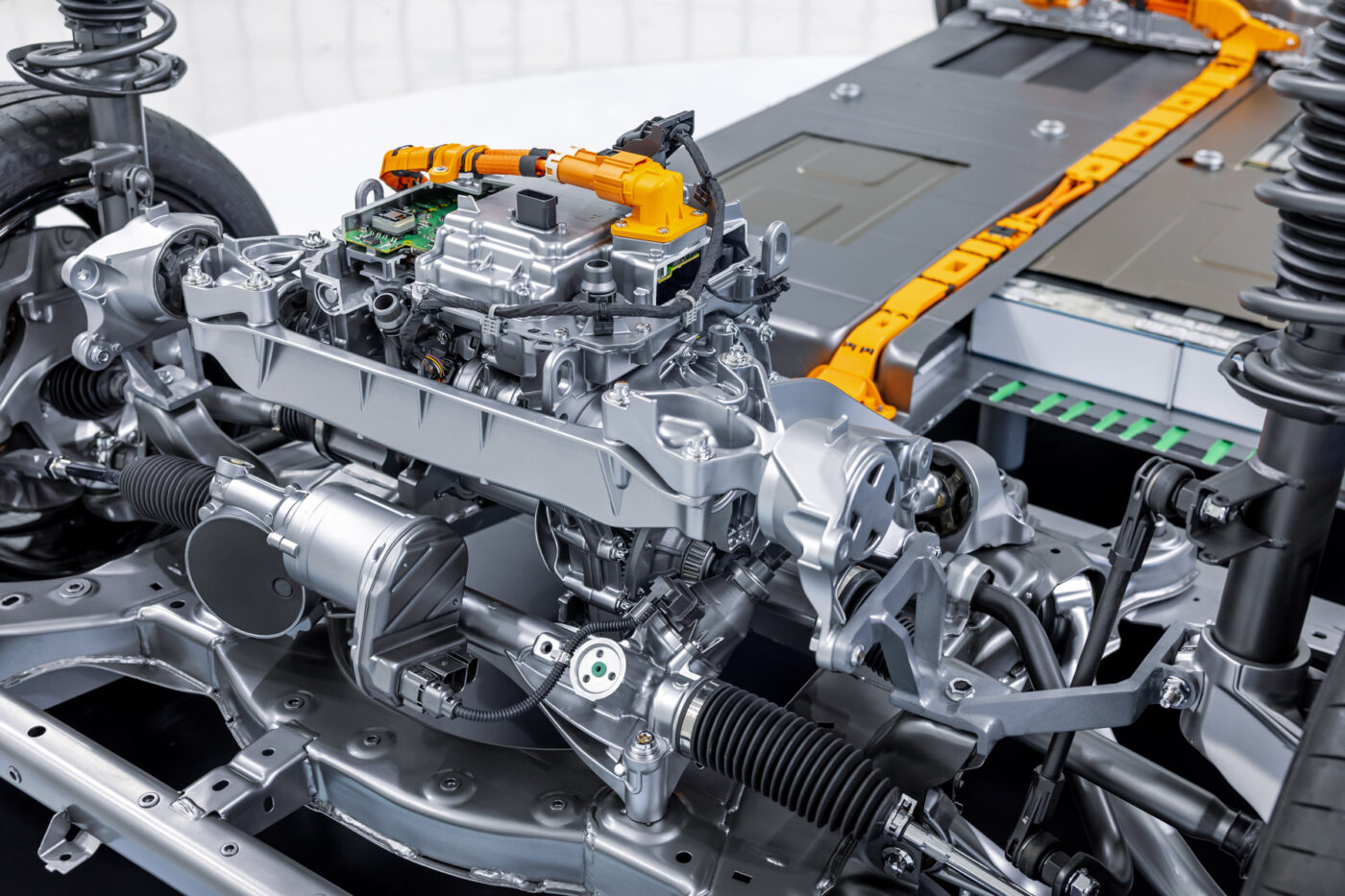
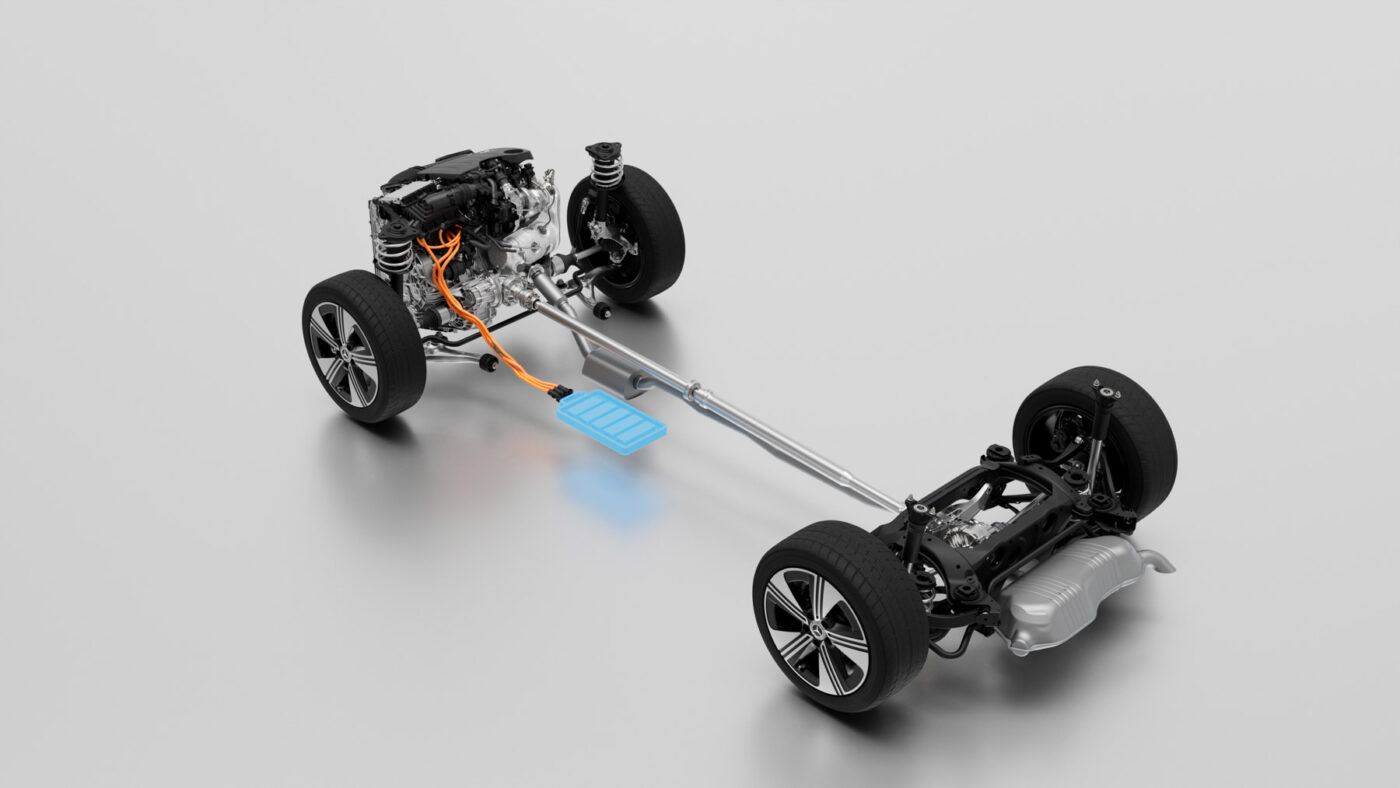
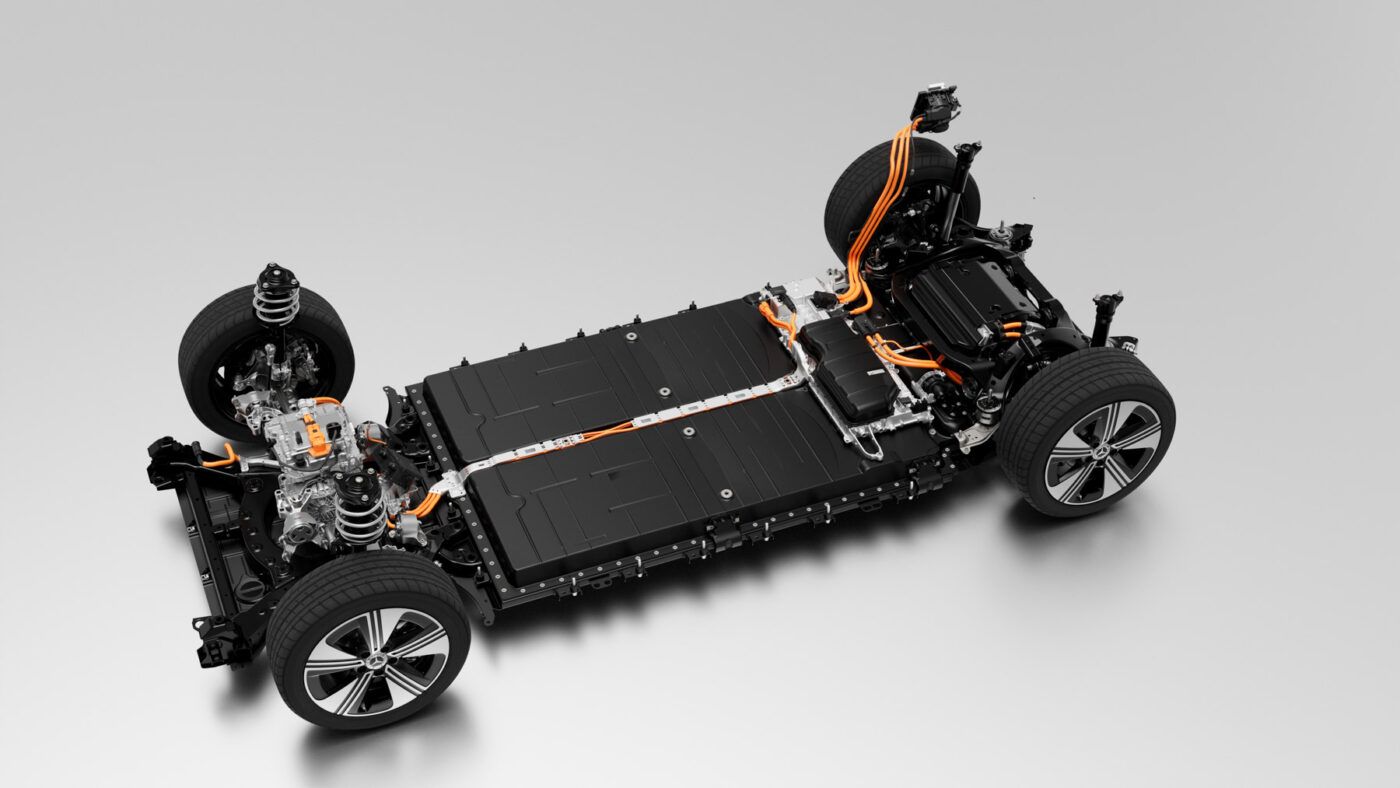
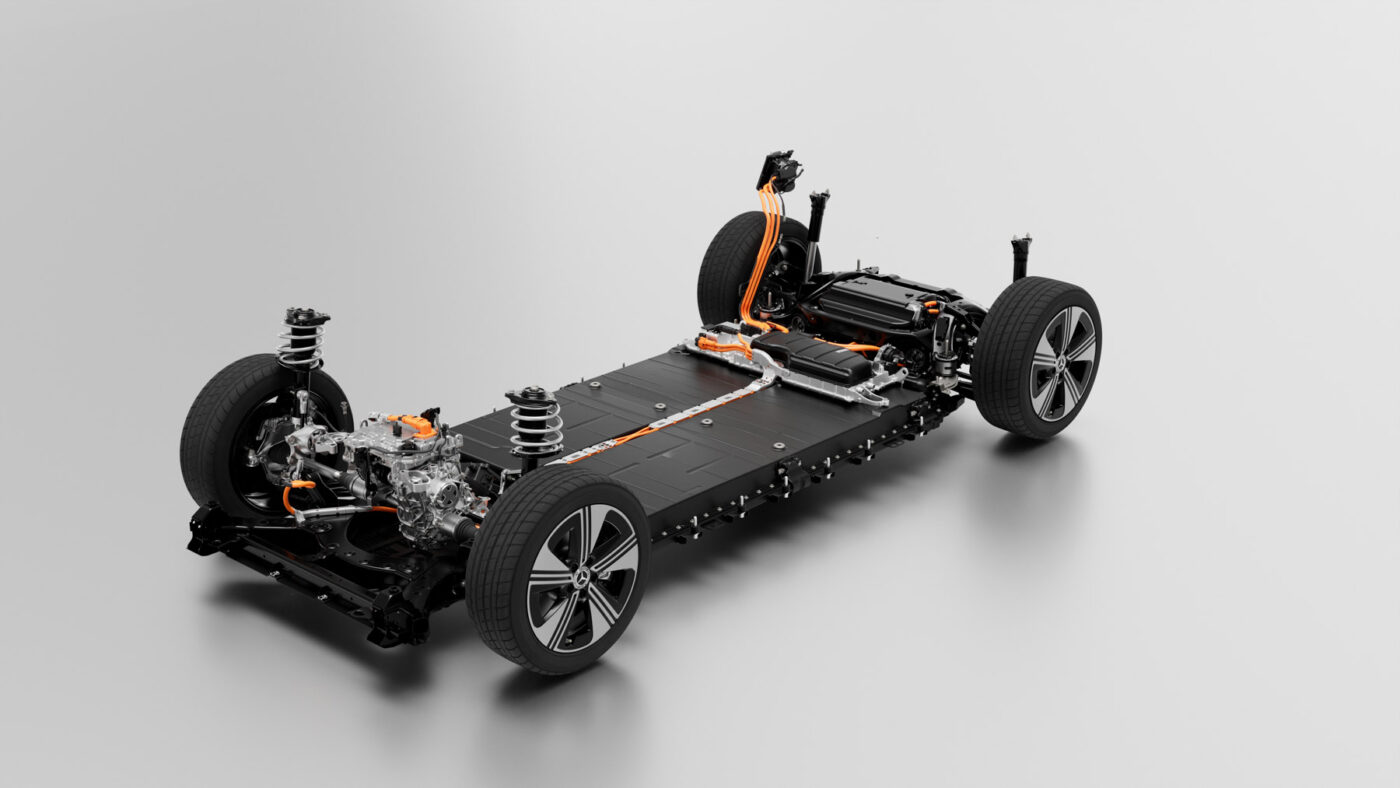
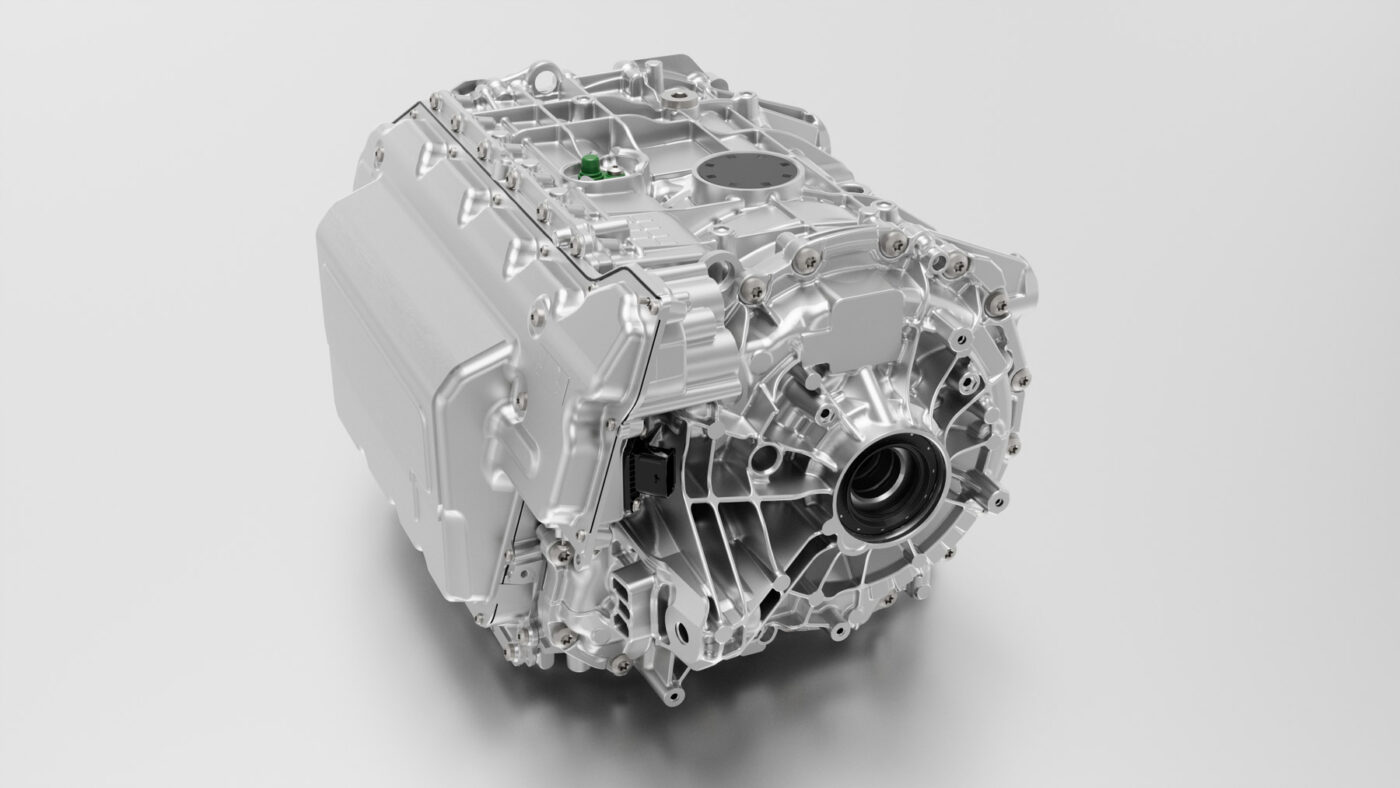
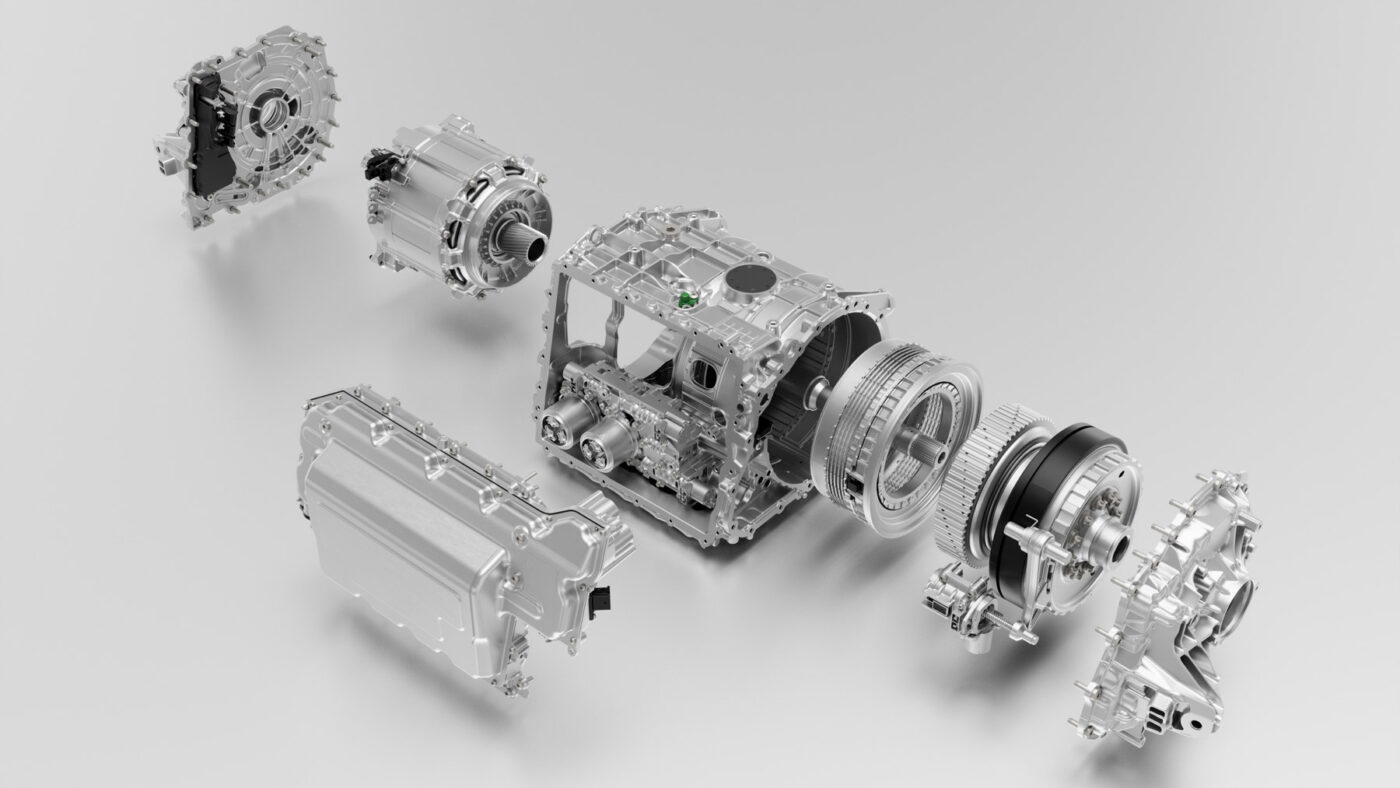
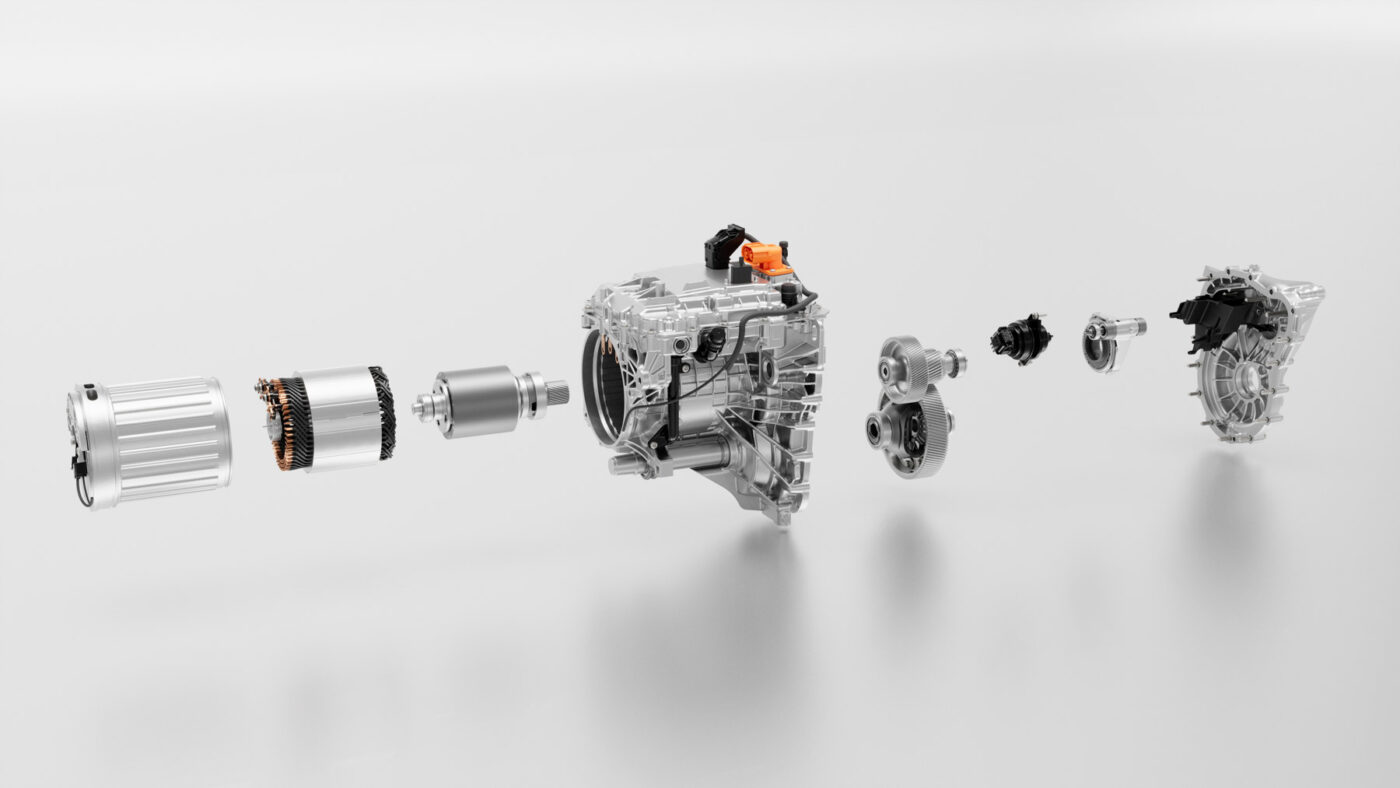
Der wohl kontroverse Part des E-Antriebs im CLA: Die Antriebseinheit im Heck verfügt über ein Zwei-Gang-Getriebe. Porsche hatte sich einst beim Taycan für ein Zwei-Gang-Getriebe an der Hinterachse entschieden, um die geforderte Beschleunigung und hohe Endgeschwindigkeit in Einklang zu bringen – viele Nachahmer hat das seitdem nicht gefunden, selbst beim Macan gibt es hinten nur einen Gang. Bei Mercedes ging es aber nur nebenher um die Dynamik, sondern vor allem um die Effizienz.
„Mit zwei Gängen können wir in einem extrem großen Bereich eine hohe Effizienz erreichen“, erläutert Pfeffer. Eine bestimmte Geschwindigkeit, bei der die Lamellenkupplung und -klauen den Gangwechsel vollziehen, gibt es dabei nicht. „Wir berechnen laufend, welcher Gang effizienter ist“, so der Entwickler. „Das hängt von der Last ab, dem gewählten Fahrmodus aber auch Faktoren wie der Batteriespannung.“
Der Vollständigkeit halber: Der erste Gang ist mit 11:1 übersetzt, der zweite mit 5:1. Über 110 km/h ist immer der zweite Gang eingelegt, beim Anfahren der erste – dazwischen entscheidet das Steuergerät.
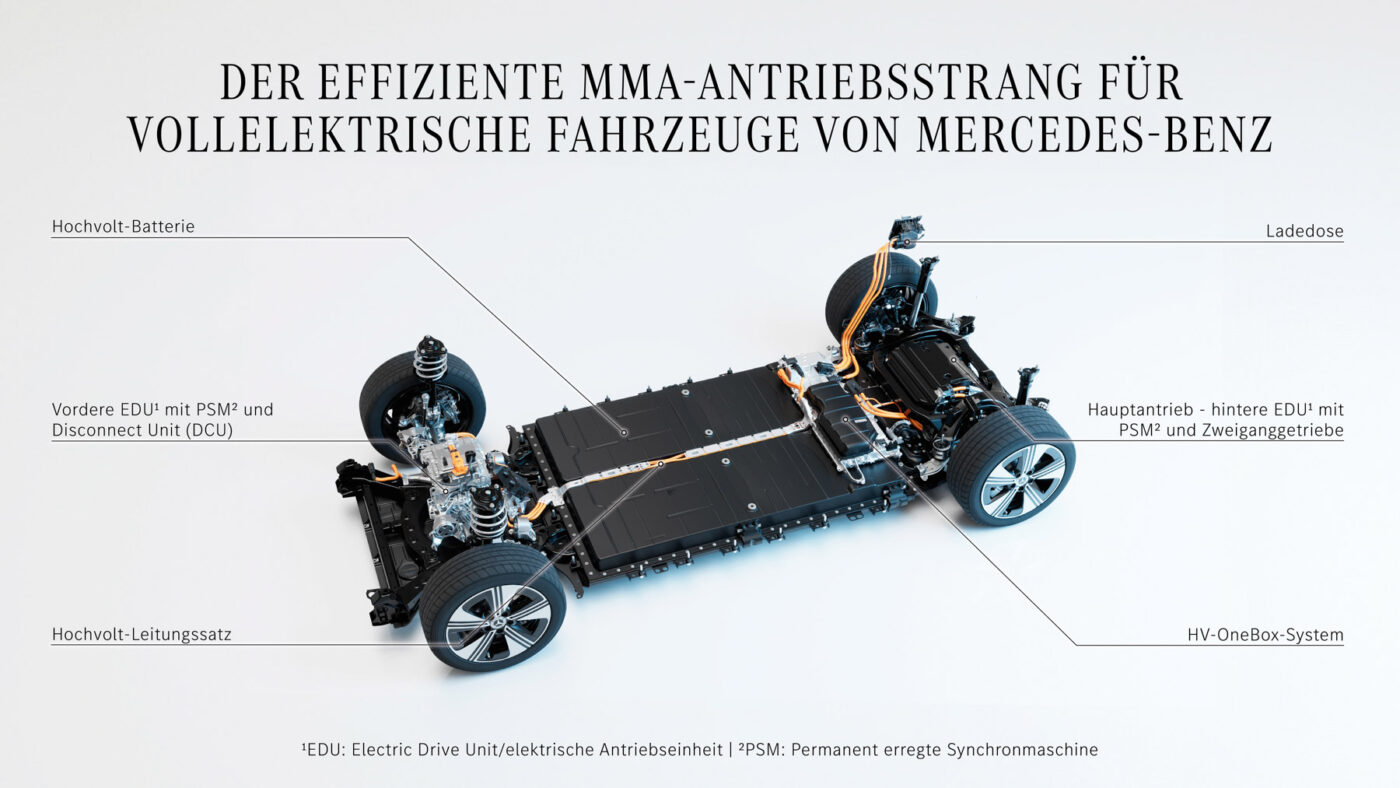
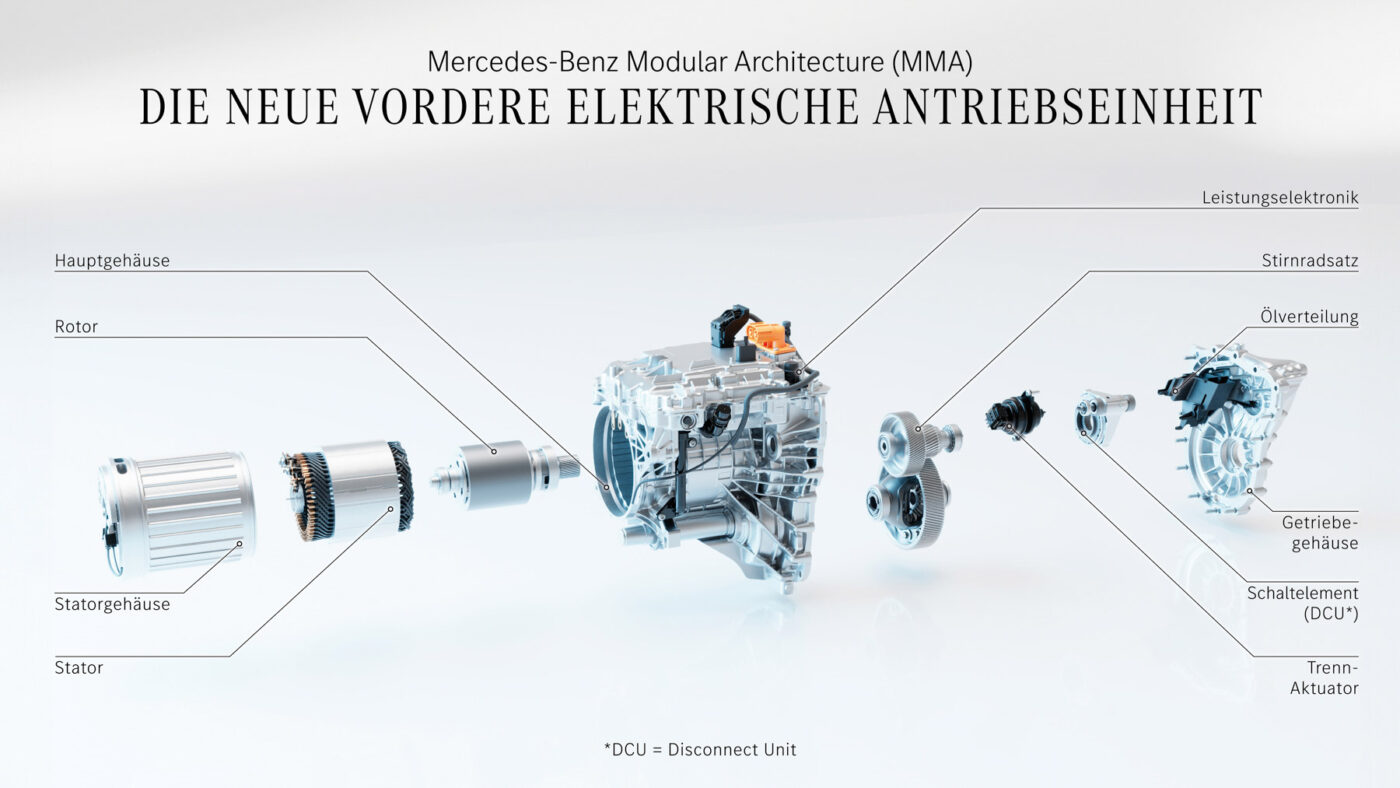
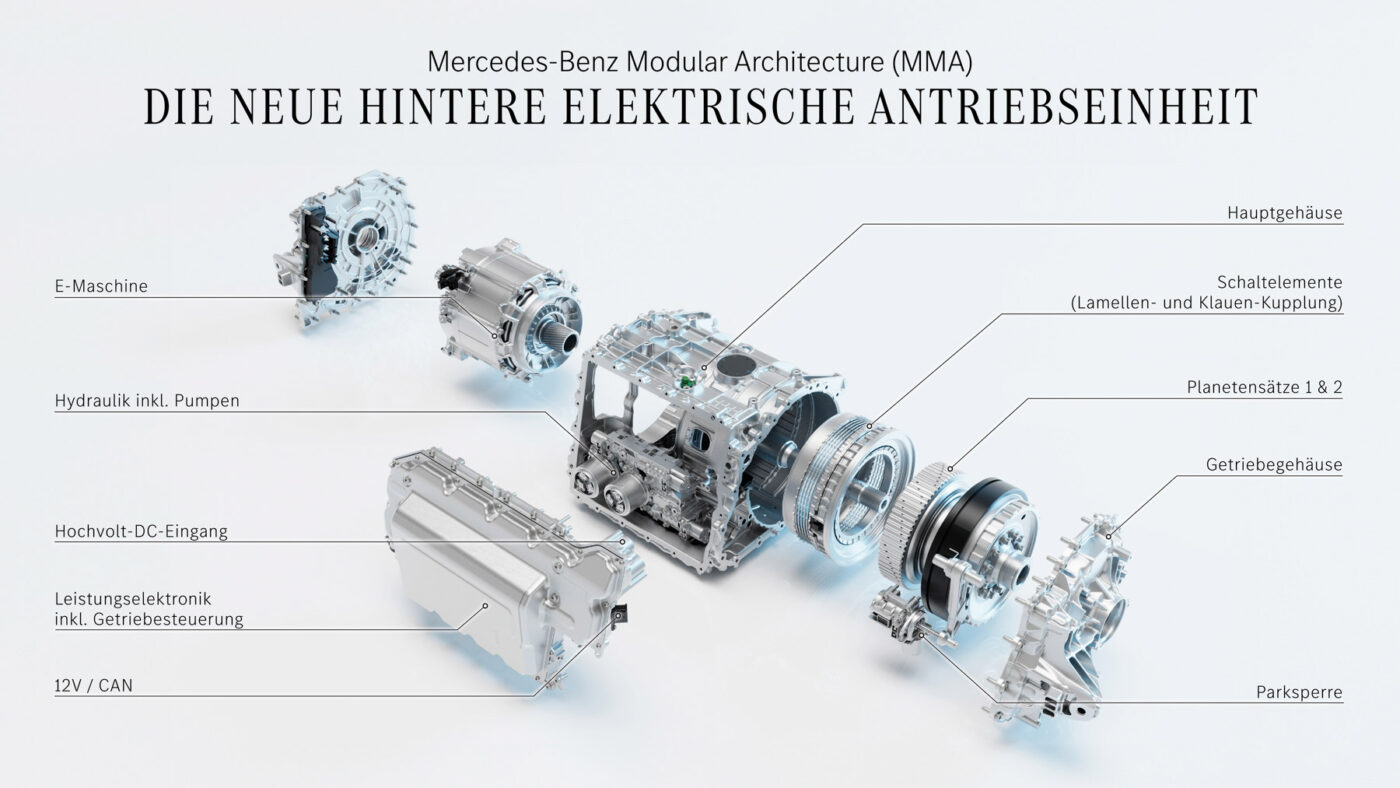
Bei den Allradlern kommt vorne noch eine zugekaufte PSM mit 80 kW zum Einsatz. Diese wird zum Anfahren und bei hoher Last als Boost-Aggregat genutzt. Bei den meisten Alltagsfahrten und konstanter Geschwindigkeit wird dieser Motor über eine eigene Kupplung in der sogenannten „Disconnect Unit“ mechanisch abgekoppelt. Das geschieht innerhalb von 0,2 Sekunden – so kann der vordere Motor auch schnell zum Rekuperieren zugeschaltet werden. Im CLA wird es wieder vier Rekuperations-Stufen geben – vom One-Pedal-Drive bis zur automatischen Regelung D-Auto. Die hintere Antriebseinheit wird – trotz ihres Getriebes – nicht abgekuppelt. Selbst beim Segeln bleibt der E-Motor mechanisch mit den Rädern verbunden und wird lediglich stromlos geschaltet. Im Stand wird laut Pfeffer „möglichst viel abgeschaltet, um jedes Watt zu sparen“.
Zwar will Mercedes selbst auf direkte Nachfrage noch nicht kommentieren, ob von der 200-kW-Antriebseinheit auch weitere Leistungsstufen geplant sind (etwa mit der kleineren Batterie-Option). Klar ist aber, dass unabhängig von der Batterie immer die gleiche Antriebs-Hardware verbaut wird – mit welcher Leistung dann auch immer. Und auch, dass dieses Grundkonzept in weiteren Modellen auftauchen wird, nicht nur in den vier MMA-Stromern. „Der Triebstrang, den wir für die MMA entwickelt haben, ist skalierbar – auch in andere Architekturen“, sagt Torsten Eder. „Wir können mehrere Technologien auch in andere Fahrzeugklassen übernehmen und so Synergien schaffen.“
Die Batterie
Ähnliches gilt auch für die Batterie: In der MMA debütiert quasi keine Spezialentwicklung für diese Plattform, sondern eine Art Baukasten, an deren Technologien sich auch größere Modelle später bedienen werden. Zwar gibt es bei den Stuttgartern keine dezidierte „Einheitszelle“ wie in einem Konzern mit Sitz in Wolfsburg, aber ein ähnliches Grundkonzept. Die Skalierung der Zellen will Mercedes über zwei Dimensionen steuern: die Zell-Chemie und die Größe der Zellen – hier ist vor allem die Höhe gemeint.
Im CLA ist das Batteriepack mit 192 prismatischen Zellen sehr flach – bei dem Workshop in Sindelfingen war von einem „bemerkenswert“ geringen Gesamtvolumen des Packs die Rede. Das ist nicht nur das Ergebnis der Arbeit der Batterie-Entwickler im Haus. „Wir haben uns in der Entwicklung sehr früh mit den Fahrzeug-Kollegen abgestimmt“, sagt Uwe Keller, Leiter Entwicklung Batteriesysteme.
Um eine so flache Batterie zu erreichen, hat Mercedes erst einmal eine Menge Grundlagen-Arbeit erledigt. Um das Knowhow und die Entwicklung intern zu stärken, wurden neue Wege beschritten. So steuert Mercedes mit seiner Software inzwischen alle Sensoren und Aktuatoren (z.B. im Kühlkreislauf) in der Batterie selbst an. „Wir haben uns von unseren Zulieferern quasi leere Steuergeräte besorgt“, sagt Eder. Früher wurde die entsprechende Software mit den Sensoren und Steuergeräten gleich mit eingekauft. Und mit dem e-Campus in Untertürkheim hat das Unternehmen auch die Batterie-Entwicklung auf Zell-Ebene ausgebaut.
Die Batterie-Entwicklung selbst beschreibt Keller „wie einen Zehnkampf“. Ein Zehnkämpfer muss den optimalen Kompromiss zwischen seinen Disziplinen finden – ein überragender Läufer kann zwar in vielen Bereichen punkten, geht aber eventuell beim Kugelstoßen, Speerwurf oder Stabhochsprung unter, wenn er nicht ausgewogen trainiert. Auf die Batterie übertragen heißt das: Bei der Gewichtung der Faktoren wie Ladeleistung, Entladeleistung für den Antrieb, Design/Pack, Gewicht, Kosten und Reichweite sind zwar Schwerpunkte möglich, es ist aber immer ein Kompromiss gefragt. „Für uns unverhandelbar waren zum Beispiel die Sicherheit und Nachhaltigkeit. Hier sind wir keine Kompromisse eingegangen“, so Keller.
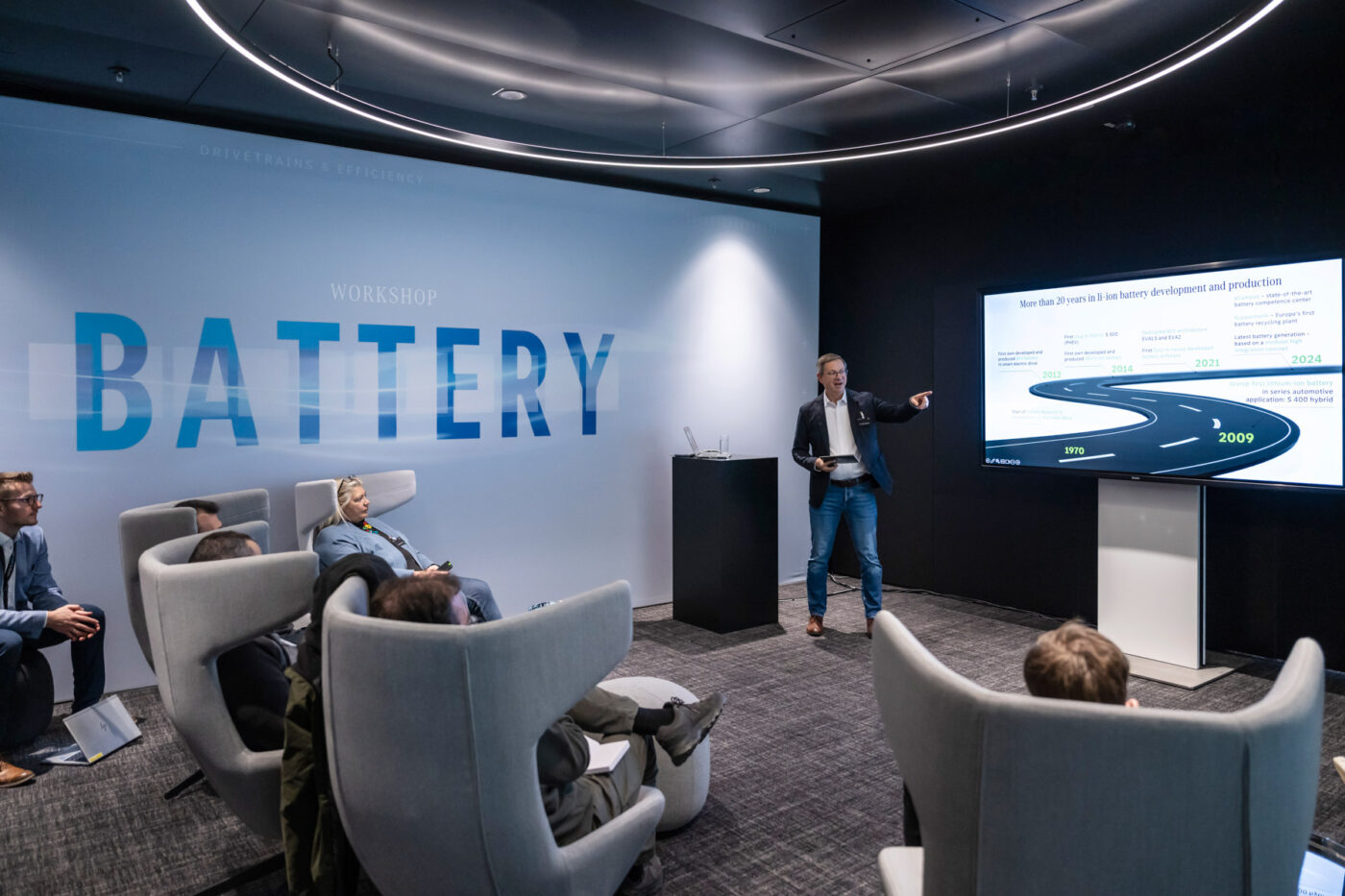
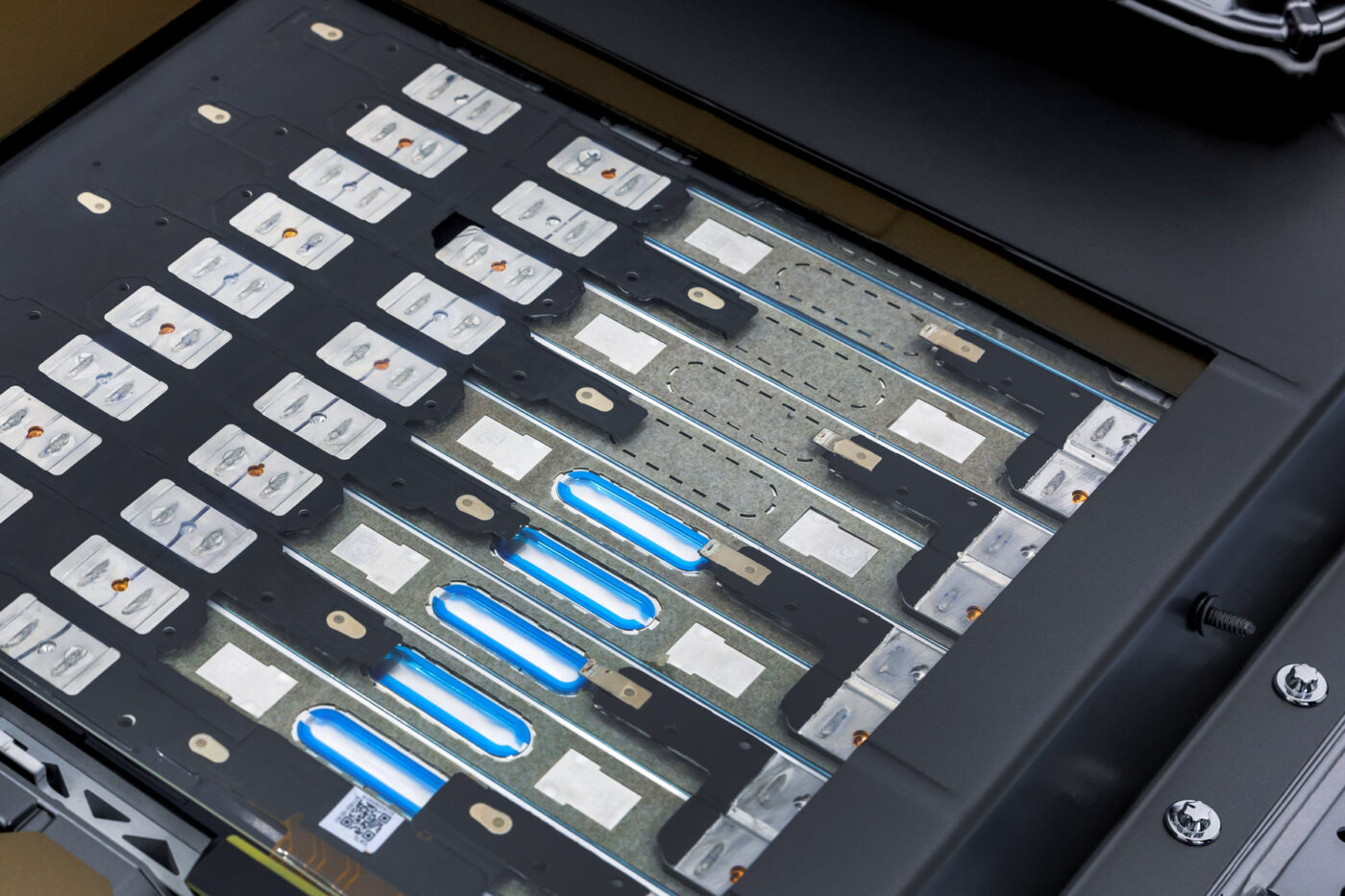
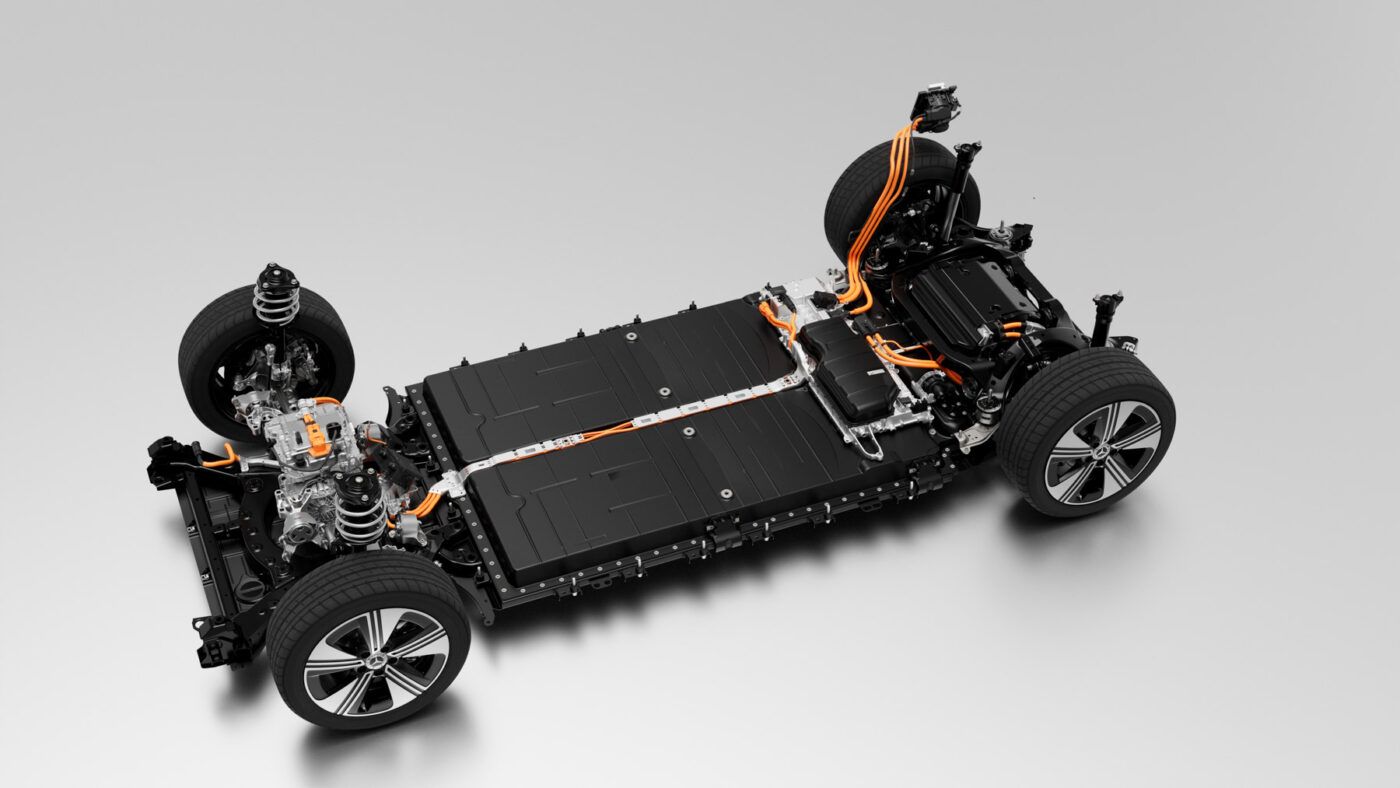
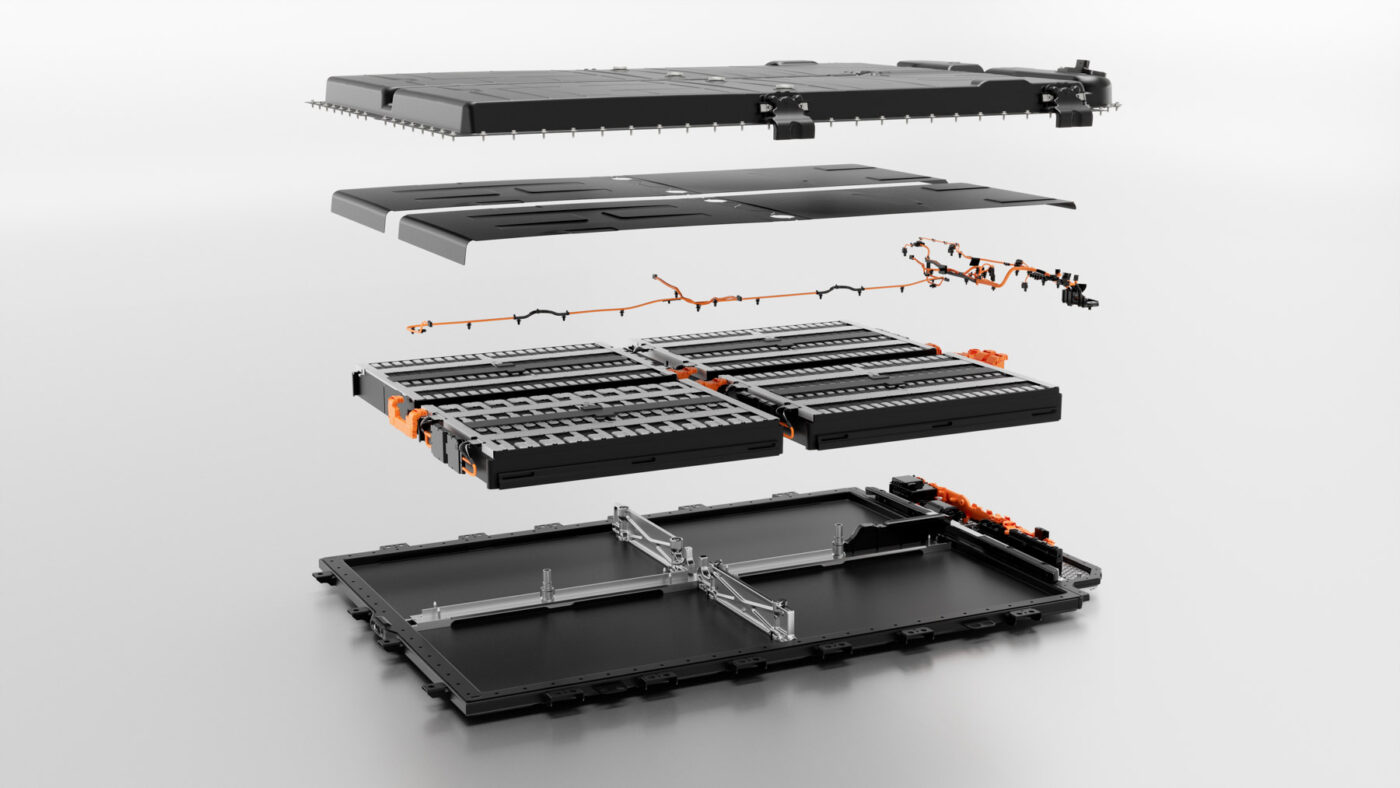
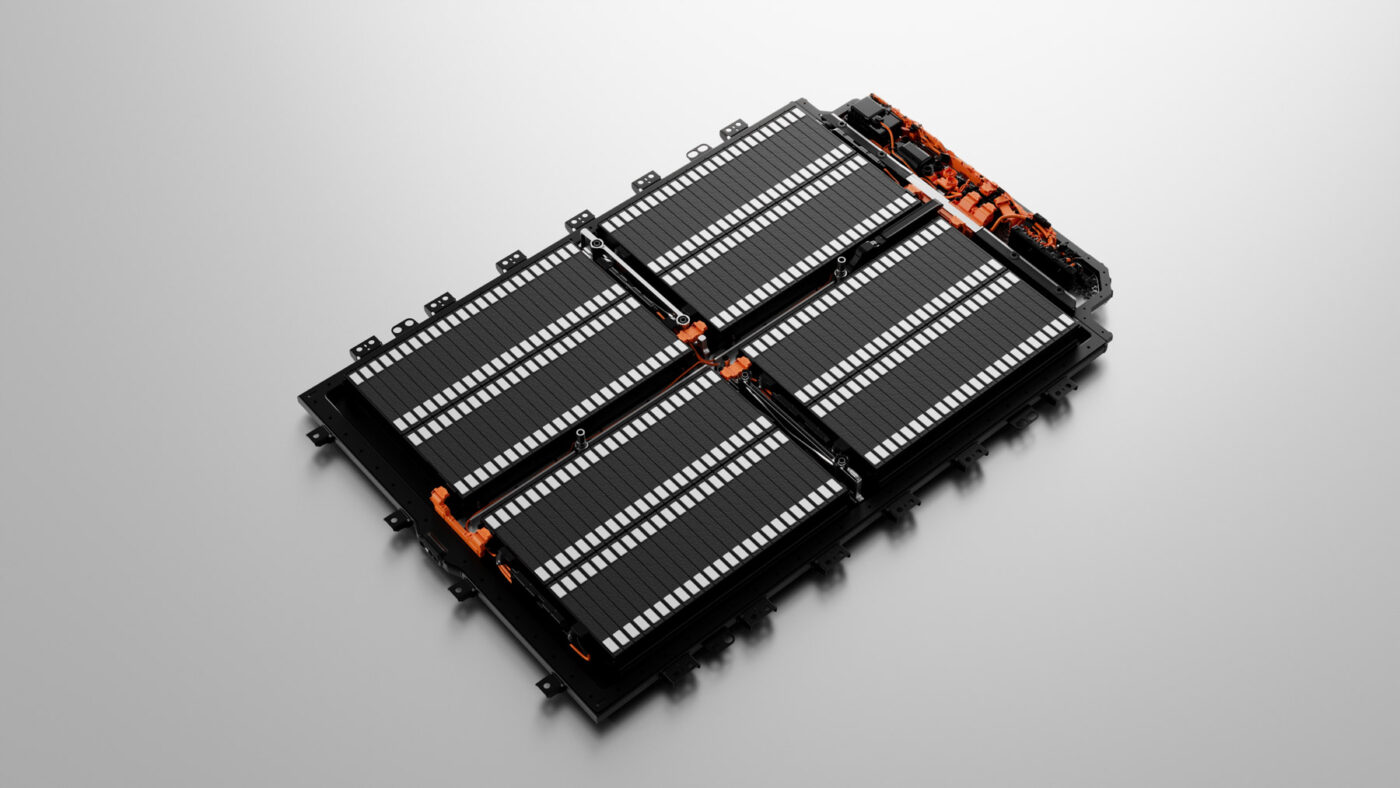
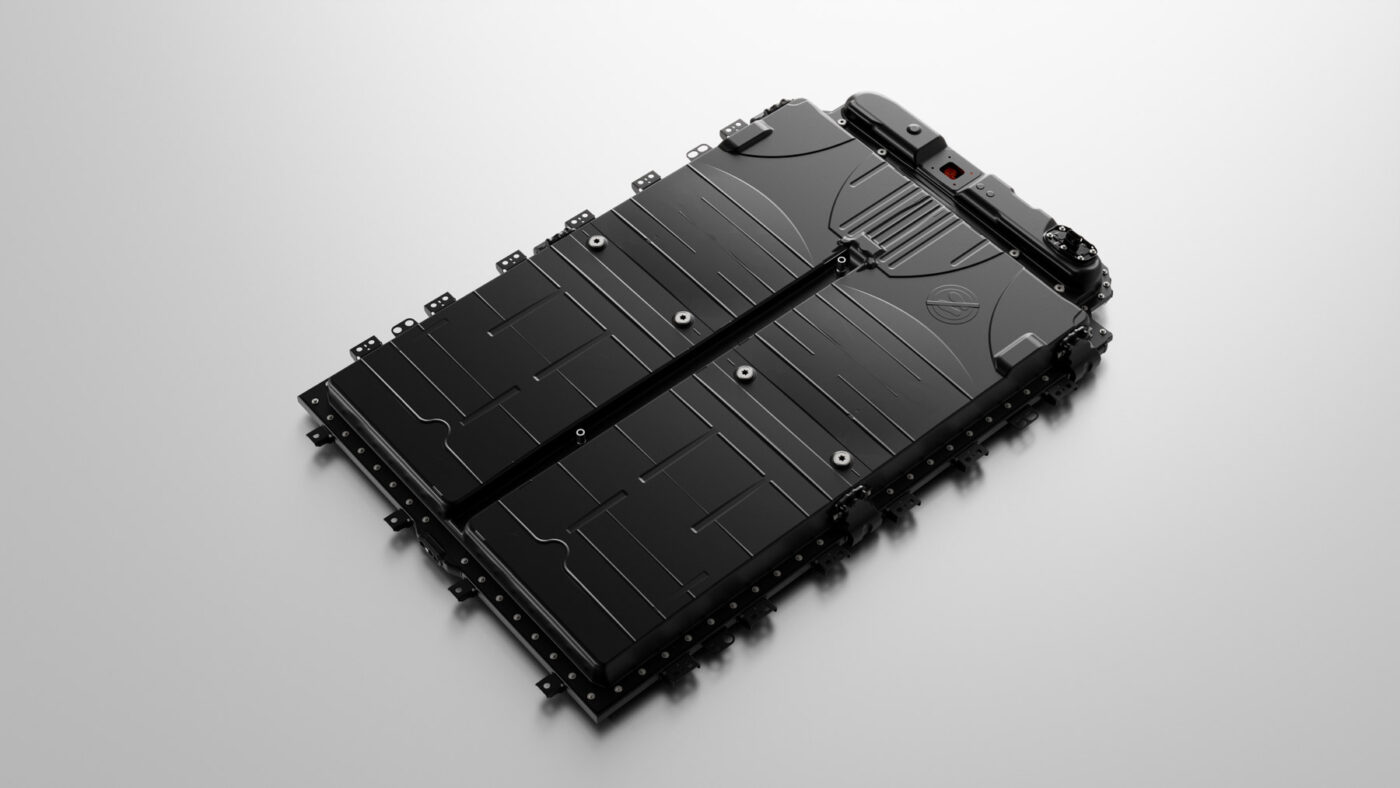
Das Ergebnis: Im CLA wird es (vorerst) zwei Batterie-Optionen geben. In der Basisversion werden LFP-Zellen genutzt, um einen niedrigeren Preis anbieten zu können. In der größeren Variante für die maximale Reichweite (angepeilt werden 750 Kilometer) kommen NMC-Zellen zum Einsatz, zum ersten Mal bei Mercedes mit einer Silizium-haltigen Anode. Beide Batteriepacks sind gleich groß und in etwa gleich schwer. Mit der höheren Energiedichte kommt das NMC-Pack auf 85 kWh, die LFP-Batterie auf 58 kWh – beides sind netto-Werte, also der tatsächlich nutzbare Energiegehalt.
Bei der Lithium-Eisenphosphat-Chemie gibt Mercedes eine Energiedichte von 450 Wh/l an, bei der NMC-Batterie sind es 680 Wh/l. Das sind bei letztgenannter Batterie 30 Prozent mehr als bisher, die gravimetrische Energiedichte konnte um 20 Prozent zu den aktuellen Batterie-Generationen gesteigert werden. Und dabei ist das Ganze noch 30 Prozent günstiger – die absoluten Werte nennt Mercedes hier nicht.
Auch zum genauen Silizium-Anteil will sich Batterie-Entwickler Keller nicht äußern. Auf wiederholte Nachfrage lässt er sich mit einem Augenzwinkern nur entlocken, dass es „unter 50 Prozent sind“ – ob fünf Prozent, zehn oder 49,9 wollte er aber nicht kommentieren. Sein Kollege Franz Nietfeld aus der Zell-Entwicklung ergänzt, dass man im Labor bereits an Hoch-Silizium-Anoden arbeite – serienreif seien diese aber noch nicht.
Bleiben wir also bei den bekannten Fakten: Gebaut wird das Pack – unabhängig von der Zellchemie – im sächsischen Kamenz und wird von dort an die Fahrzeugwerke geliefert. Also vorerst nach Rastatt für den CLA, später aber auch ins ungarische Werk Kecskemét.
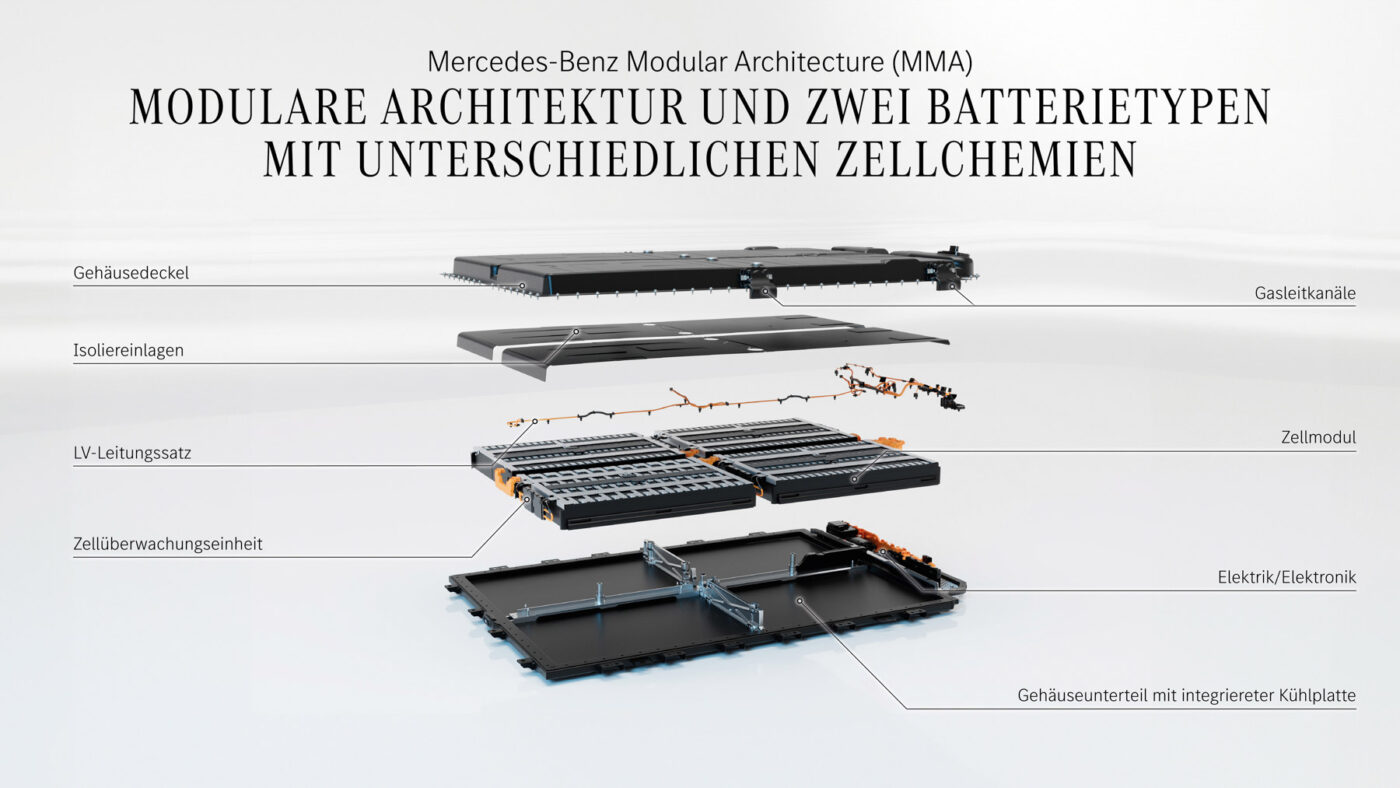
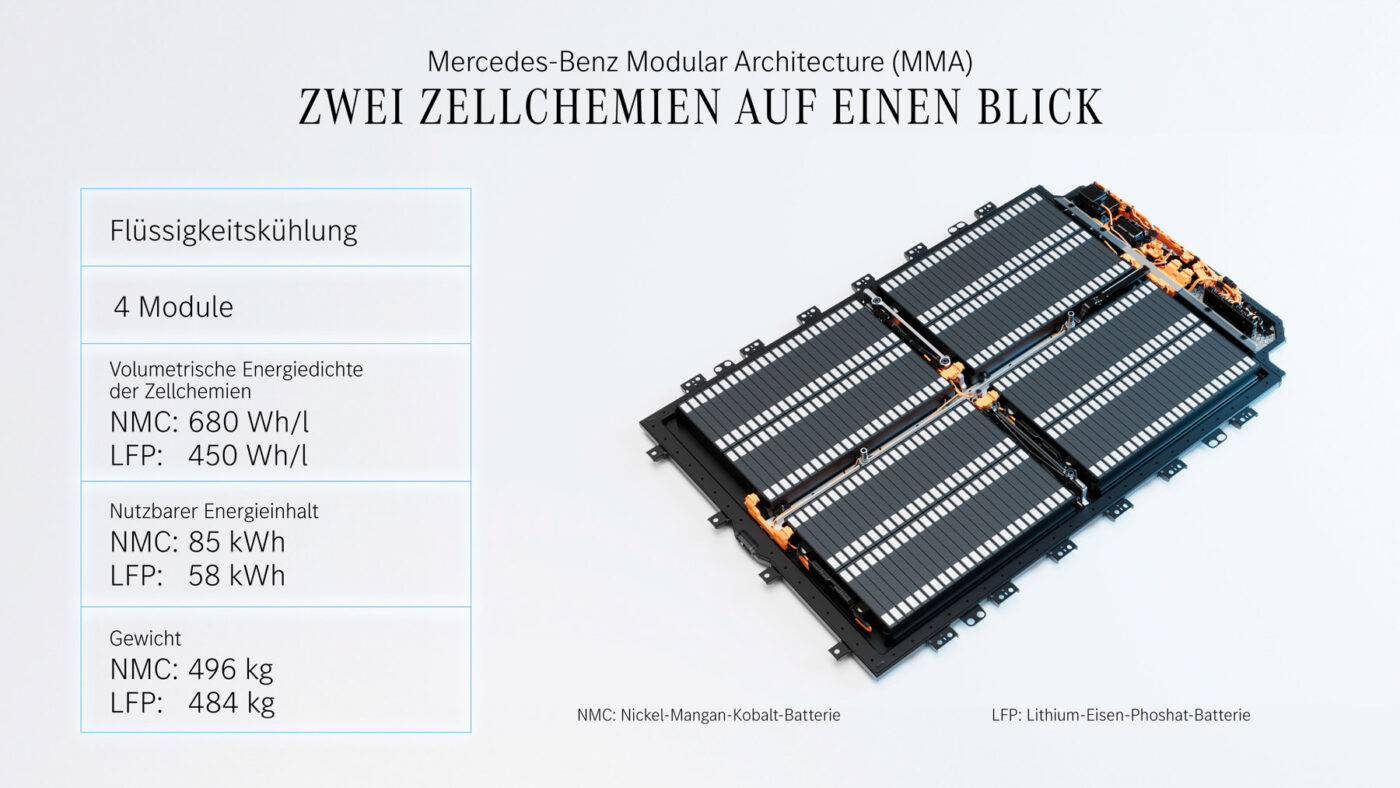
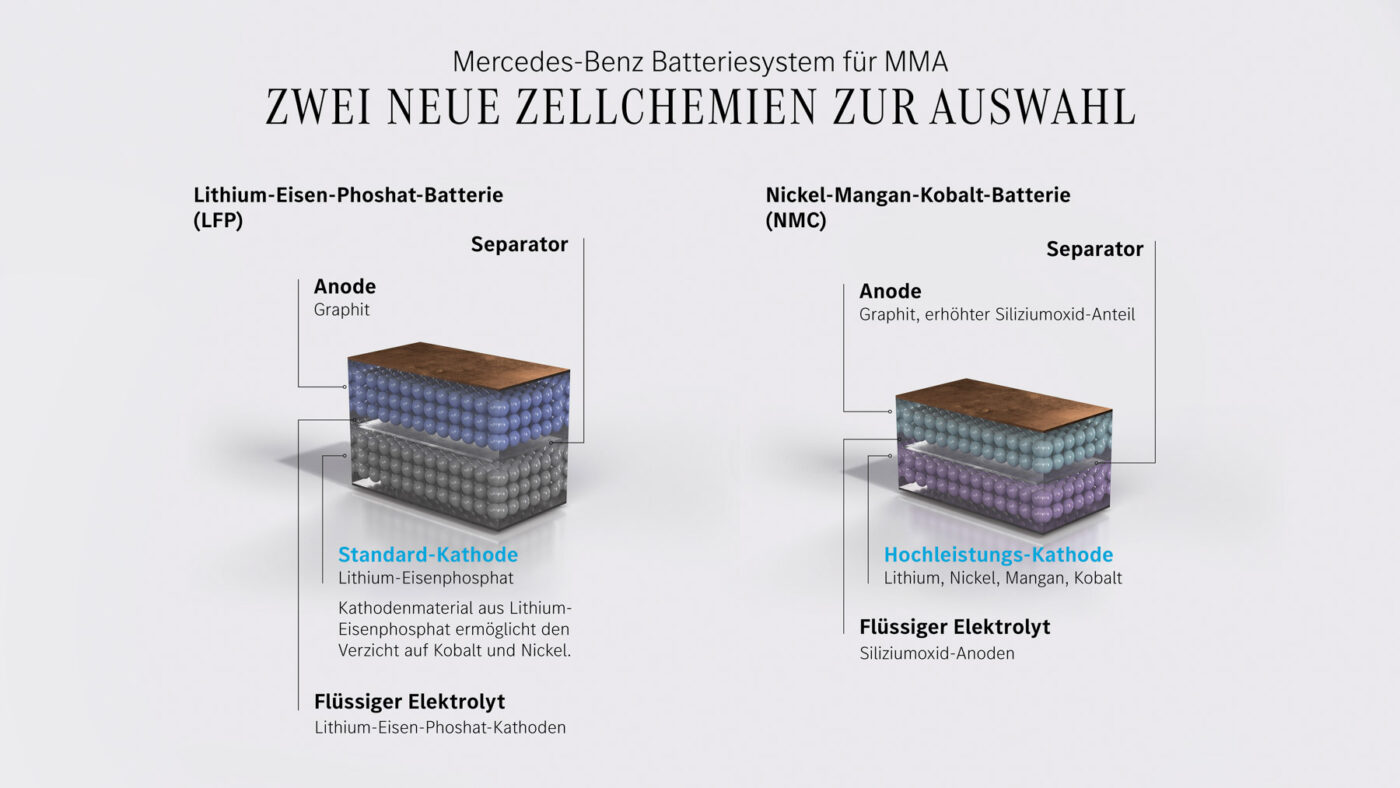
Die 192 Zellen werden dabei in vier Gruppen à 48 Zellen zusammengefasst – jeweils 24 Zellen sind nebeneinander angeordnet. Der Boden des Batteriepacks besteht aus einem Stahlrahmen mit Alu-Wanne, dort wird auch die Kühlung eingeklebt – die Zellen werden also nur über die Unterseite gekühlt bzw. erwärmt. Die vier Zell-Gruppen werden dann in das Pack eingeklebt. Das hat mehrere Vorteile: Zum einen werden ganz einfach die Steifigkeit erhöht und Gewicht eingespart. Zum anderen fallen in der Produktion keine Späne an, was bei der Zuverlässigkeit und Dichtigkeit hilft.
Daher spricht Keller auch von „einer Mischung aus Cell-to-Module und Cell-to-Pack“. Ja, es wird auch bei Mercedes geklebt, aber anders als bei einem Cell-to-Pack-Konzept eben nicht alles. So kann bei der MMA der Batteriedeckel abgeschraubt werden. Sobald die darunter liegende Isolierschicht entfernt wird, sind die Module, der Leitungssatz und sämtliche Steckverbindungen von oben zugänglich – und können bei einem Defekt einzeln getauscht werden.
Das Laden
Hier kommt die Zeiteffizienz ins Spiel. Zwar ist es gut für die Reichweite, wenn Antrieb und Karosserie effizient sind. Wenn der Kunde dann aber 40 Minuten an der Ladesäule steht, ist er nicht unbedingt schneller am Ziel als mit einem E-Auto, das zwar etwas mehr verbraucht, dafür aber deutlich schneller lädt. Bei der Veranstaltung in Sindelfingen hat Mercedes wiederholt betont, welchen Einfluss das Concept Car Vision EQXX, das ebenfalls im Electric Software Hub entwickelt wurde, auf den CLA und die MMA hatte. Der E-Motor sei „sehr ähnlich“ (wenn auch ohne Zwei-Gang-Getriebe), die Batterie-Konstruktion ebenfalls. Was Mercedes aber nicht erwähnt hat: Beim Thema Laden hebt sich der CLA deutlich vom EQXX ab. Denn dieser wurde schließlich gebaut, um auf über 1.000 Kilometer eben nicht geladen zu werden – entsprechend schwach war die Ladeleistung.
Bei einem Serienauto, das 2025 debütiert, muss das natürlich anders sein. Kurze Ladezeiten sind für die Kunden wichtig. Daher setzt Mercedes beim CLA – anders als beim großen EQS – auf 800 Volt Systemspannung. Für die 800 Volt sprechen mehr Faktoren als die reine Ladeleistung, aufgrund der geringeren Stromstärke bei gleicher Leistung können die Kabel dünner und leichter ausfallen.
Die Ladeleistung, die der CLA erreicht, wäre mit einem 400-Volt-System und der heutigen Ladeinfrastruktur nicht ohne Weiteres möglich: Es stehen 320 kW in der Spitze im Datenblatt. „Was für uns viel wichtiger ist als die Peak-Leistung: Wie viel Reichweite kann ich in zehn Minuten Nachladen?“, erklärt Torsten Eder. „Hier schaffen wir 300 Kilometer!“ Seine Entwickler ergänzen später in ihren Workshops, dass die Ladezeit von zehn auf 80 Prozent bei unter 22 Minuten liegt. Mit zwei Ladestopps à zehn Minuten sollen 1.200 Kilometer möglich sein.
All diese Angaben beziehen sich auf die 85 kWh große NMC-Batterie. Zu der LFP-Variante mit ihren 58 kWh wurden in Sindelfingen keine weiteren Details genannt. Hier muss man also die Weltpremiere abwarten, um genauere Infos zum Ladeverhalten zu erfahren.
Bei der Konstruktion weist das Ladesystem eine gewisse Ähnlichkeit mit der PPE des VW-Konzerns auf: Die gesamte Lade-Technik (für AC und DC) ist hinten auf der Oberseite des Batteriepacks verbaut – Mercedes nennt das Bauteil „One Box“. Da die Lade-Technik unter den Rücksitzen platziert ist, werden zumindest die MMA-Stromer den Ladeanschluss hinten haben – ein in Sindelfingen ausgestelltes Skateboard-Modell hatte die CCS-Buchse über dem Hinterrad auf der Beifahrerseite. Zwar gibt es die Bemühungen, aus Effizienzgründen die Hochvolt-Kabel möglichst kurz zu halten. Es ist aber denkbar, dass der Ladeport an anderer Stelle, etwa nahe dem Rücklicht, platziert wird – wahrscheinlich ist aber eher die klassische Tankdeckel-Position.
Der Hybrid
Nicht ganz unter den Tisch fallen soll auch die kommende Hybrid-Version des CLA. Die MMA wurde zwar ohne Kompromisse auf Batterie-elektrische Autos ausgelegt, ermöglicht aber auch einen Hybridantrieb. Dieser wird nach der BEV-Version kommen und ist für electrive aus einem Grund erwähnenswert: Obwohl es nur ein 48-Volt-Hybrid ist, kann der CLA rein elektrisch fahren.
Konkret handelt es sich um einen P2-Hybrid, die E-Maschine (auch hier eine PSM) wirkt auf die Eingangswelle des Acht-Gang-Doppelkupplungsgetriebes mit dem sperrigen Namen 8F-eDCT. Damit kann in allen acht Gängen mit E-Unterstützung gefahren und auch rekuperiert werden. Da in der kompakten Elektromotor-Getriebe-Einheit noch eine dritte Kupplung verbaut ist, kann der Verbrenner komplett abgetrennt werden. Mit den 20 kW der E-Maschine kann dann rein elektrisch gefahren werden – nicht nur langsam in der Stadt, sondern laut den Entwicklern bei den Testfahrten auch bei bis zu etwas über 100 km/h, wenn bei einer Konstantfahrt die Geschwindigkeit gehalten werden soll.
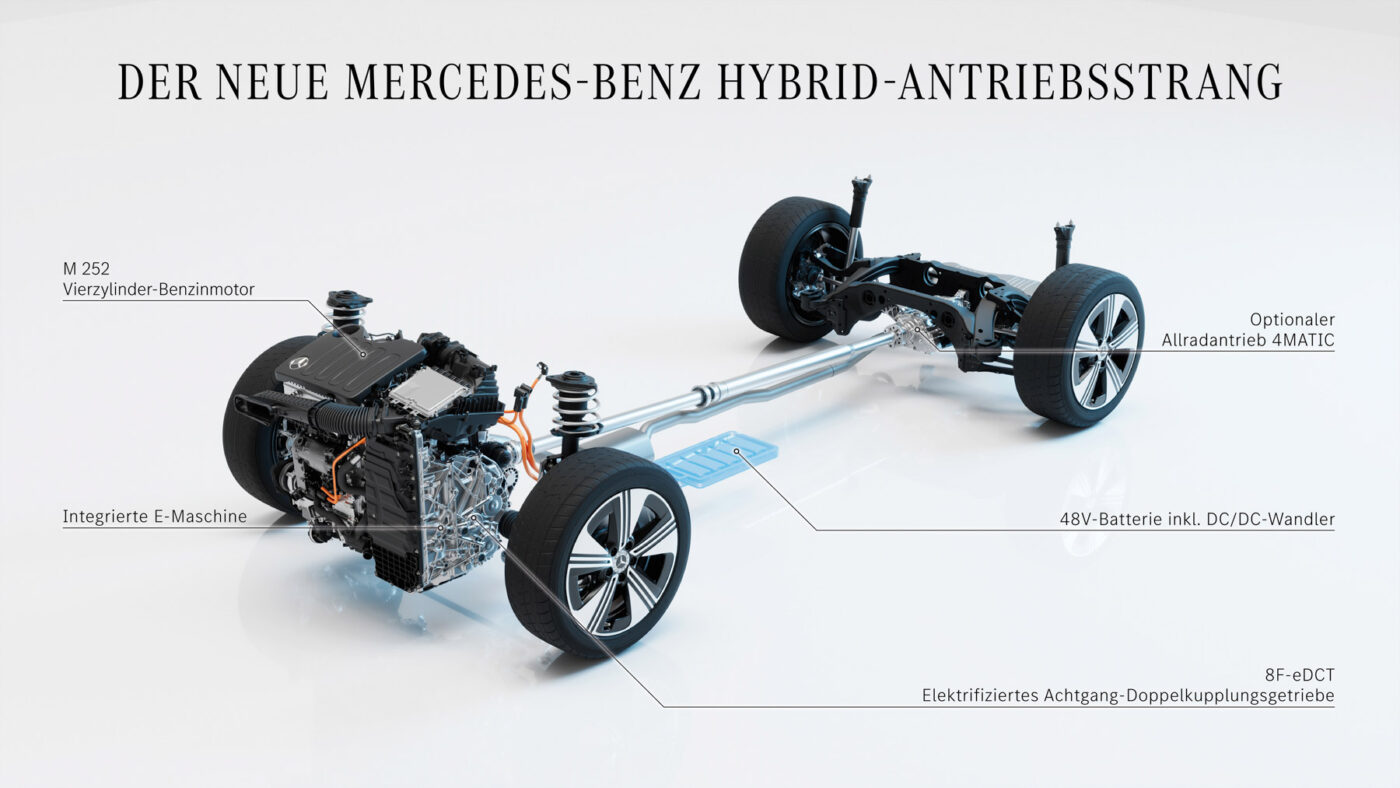
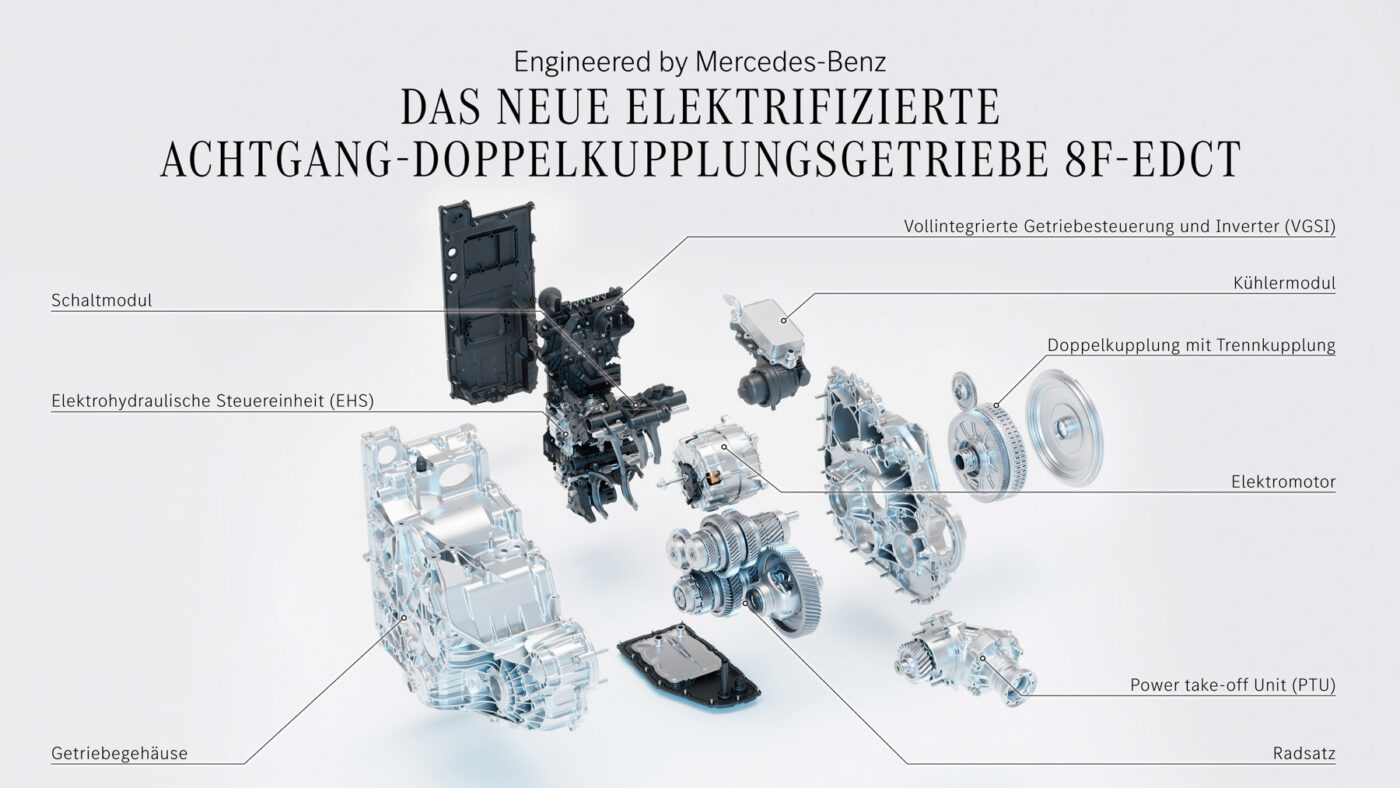
Die Batterie fasst 1,3 kWh, wovon aber nur 800 Wattstunden für das Fahren vorgesehen sind. Eine rein elektrische Reichweite wird Mercedes nicht kommunizieren und auch nicht zertifizieren lassen.
Den Verbrenner-Part übernimmt ein 1,5 Liter großer Vierzylinder, eine Neuentwicklung. Aufgrund des knappen Bauraums, der für einen kleinen Elektromotor und einen Frunk beim E-Auto ausgelegt ist, muss der ganze Hybrid extrem kompakt ausfallen. Angeboten werden drei Leistungsstufen mit 100, 120 und 140 kW. Der M252 genannte Turbo-Benziner wurde zwar von Mercedes-Benz entwickelt, gebaut wird er aber in keinem Mercedes-Werk. Sondern von der Geely-Tochter Aurabay China.
Das Electric Software Hub
Mit zum CLA und der MMA beigetragen hat auch das neue Gebäude, in dem weite Teile der Entwicklung stattgefunden haben. Das ESH, wie es Mercedes-intern genannt wird, ist eine Art interdisziplinäres Entwicklungszentrum. Denn dort wird nicht nur an der namensgebenden Software für die Elektroautos gearbeitet, sondern auch an der Zusammenführung mit der Hardware.
Das ESH bietet auf mehreren Geschossen Büroräume, aber auch Prüfstände. Dort können nicht nur einzelne Komponenten des Antriebs oder die komplette Elektro-Architektur mit allen Bauteilen stromführenden Bauteilen vom kleinen Sensor über den elektrischen Fensterheber bis zur 800-Volt-Batterie unter verschiedenen Klima-Bedingungen getestet werden, sondern auch Gesamtfahrzeuge.
„Früher hat jede Abteilung ihre Komponente für sich entwickelt und am Ende wurde alles zusammengefügt – Motor, Getriebe, Fahrwerk, Chassis und so weiter. Heute ist alles zusammen gewachsen“, sagt Test-Ingenieur Philipp Werner. „Im Electric Software Hub wird in den oberen Stockwerken die Software entwickelt und im Erdgeschoss haben wir die Antriebs- und Fahrzeugprüfstände. Wenn wir hier auf dem Prüfstand ein Problem feststellen, sind die Kollegen in wenigen Minuten mit dem Laptop hier.“
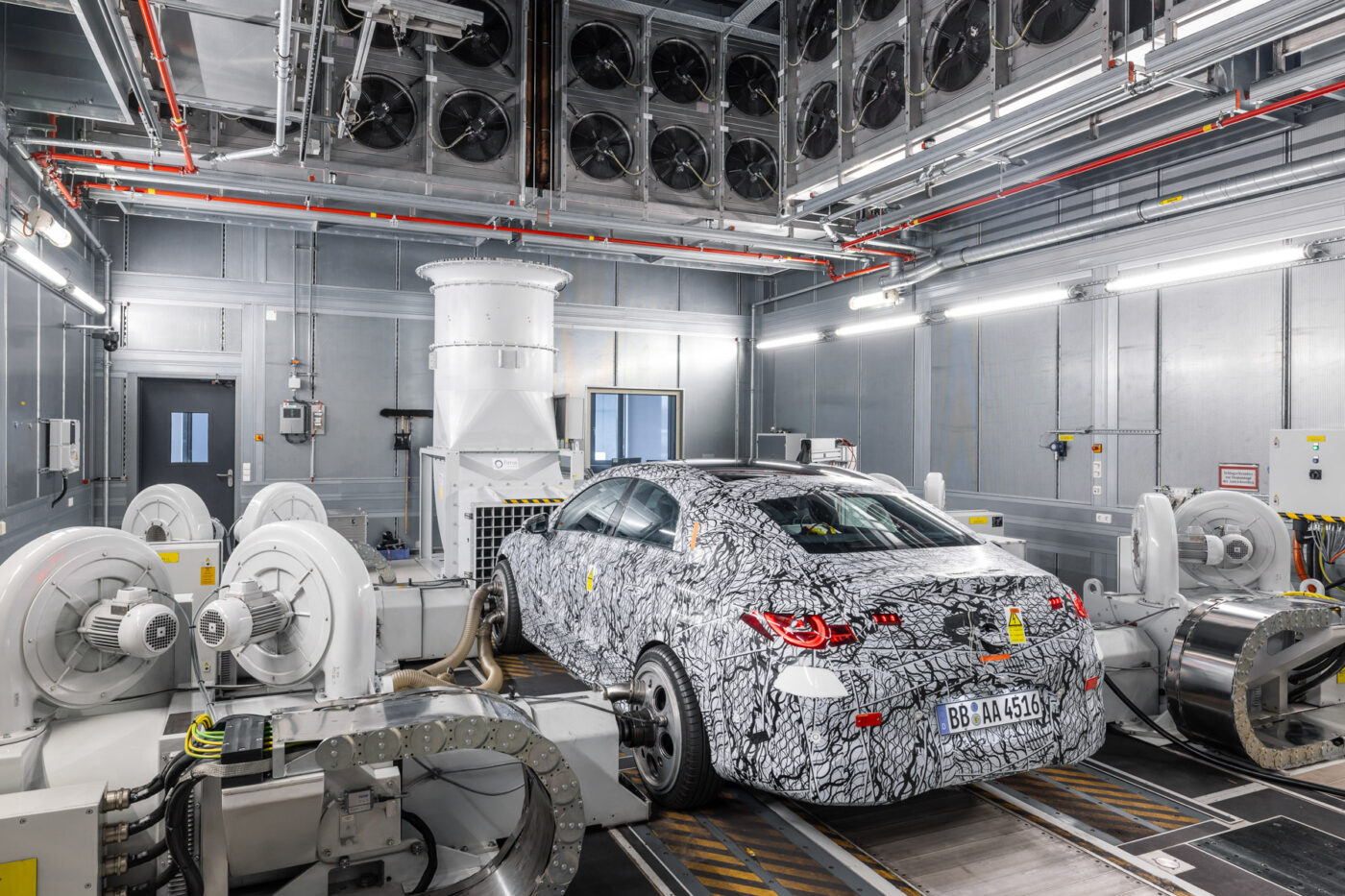
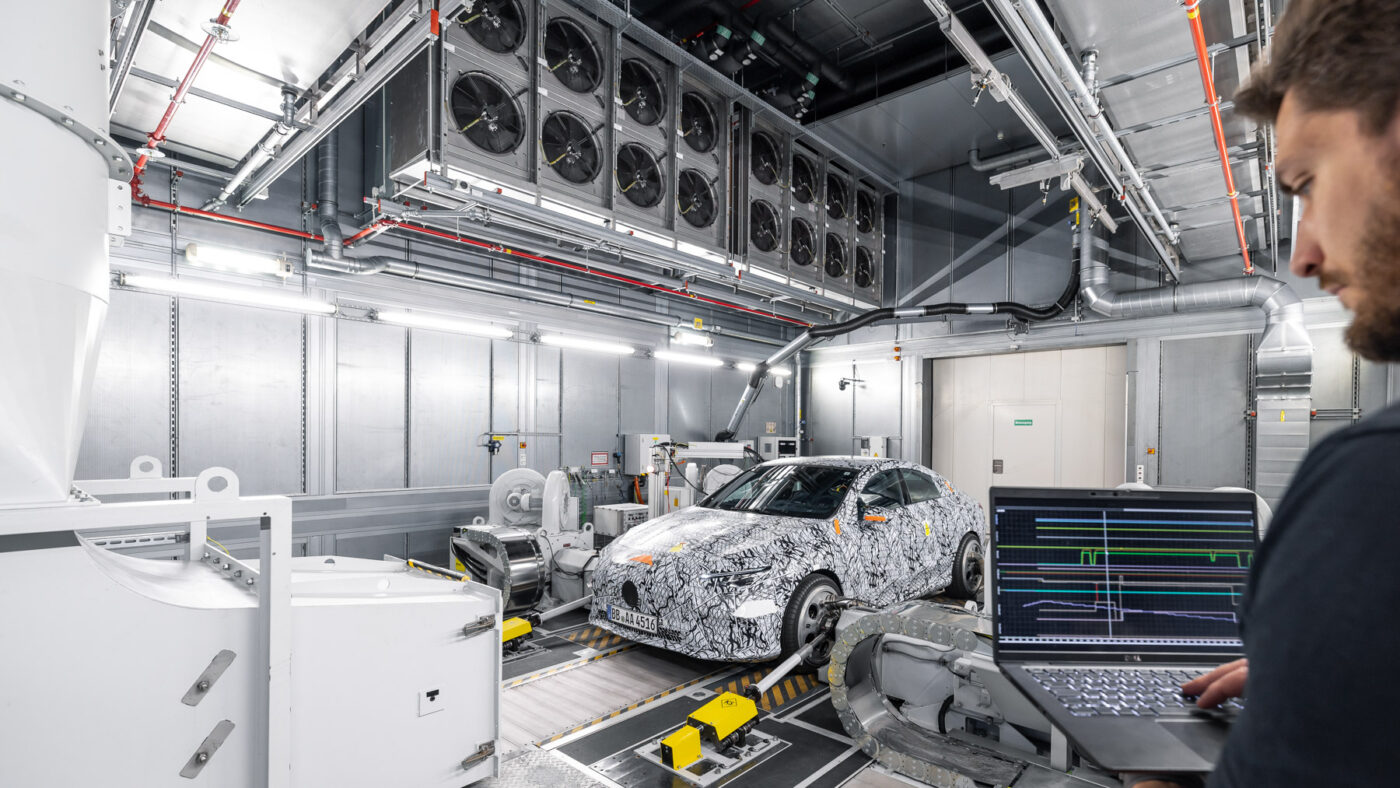
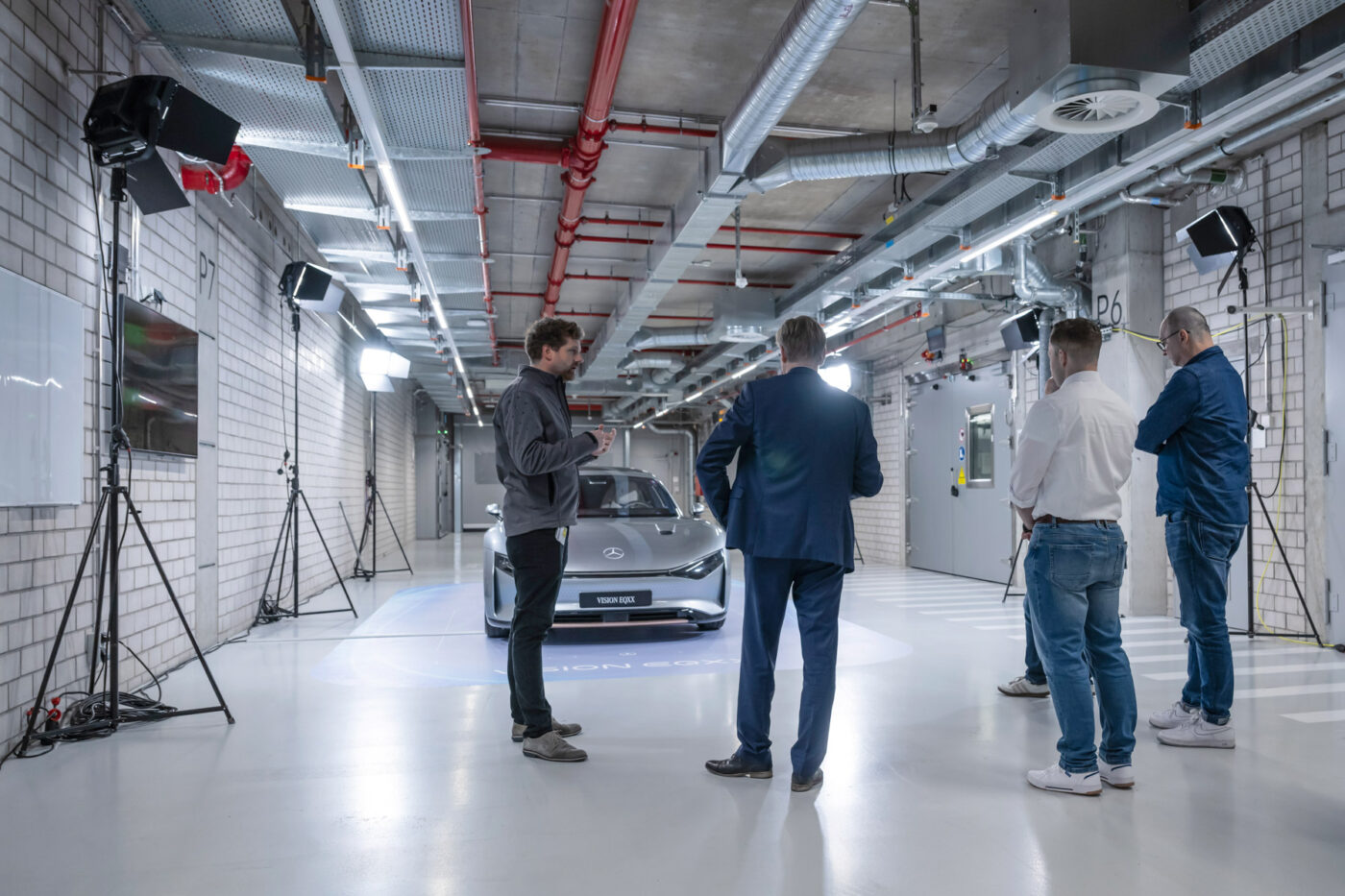
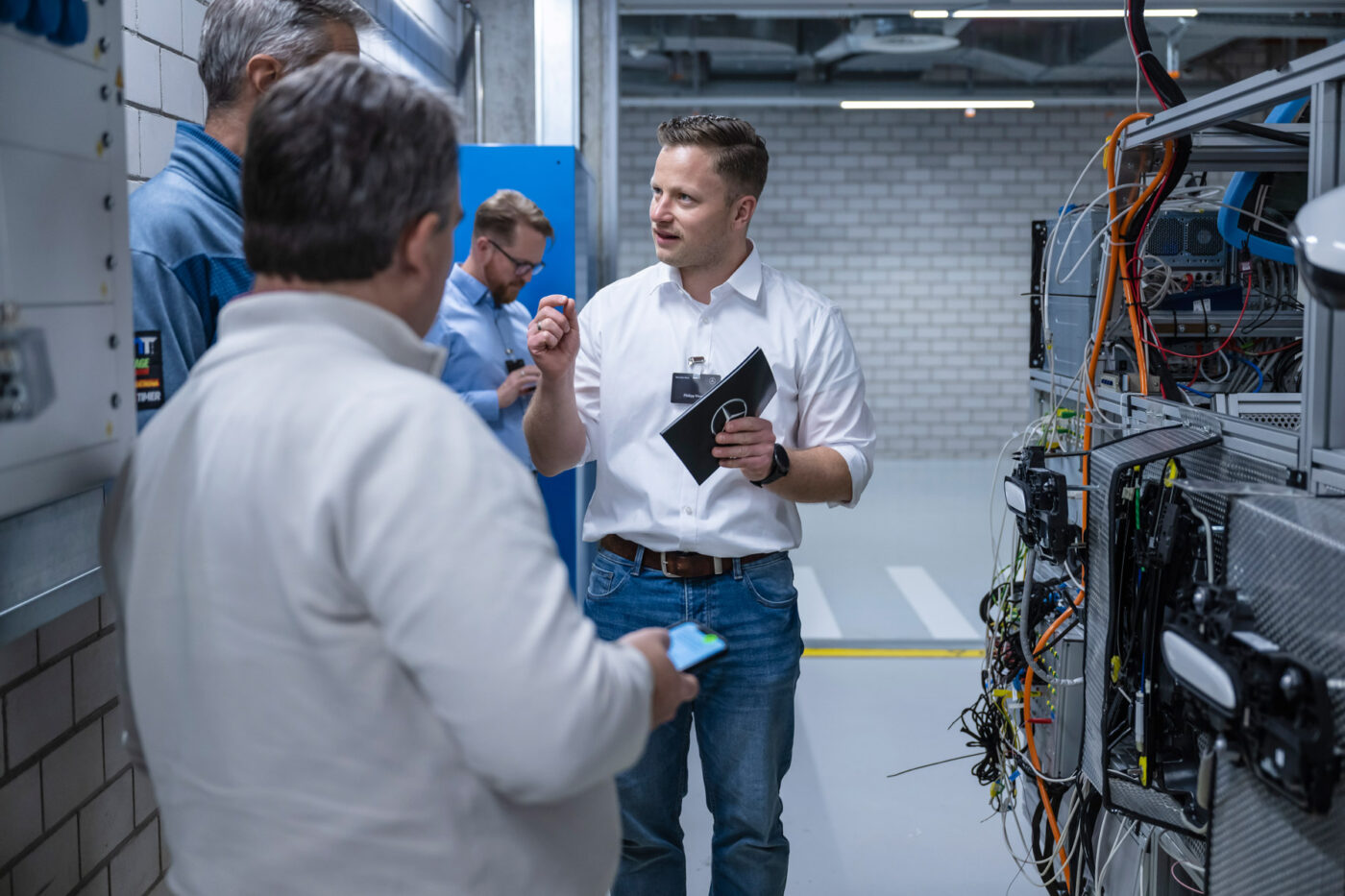
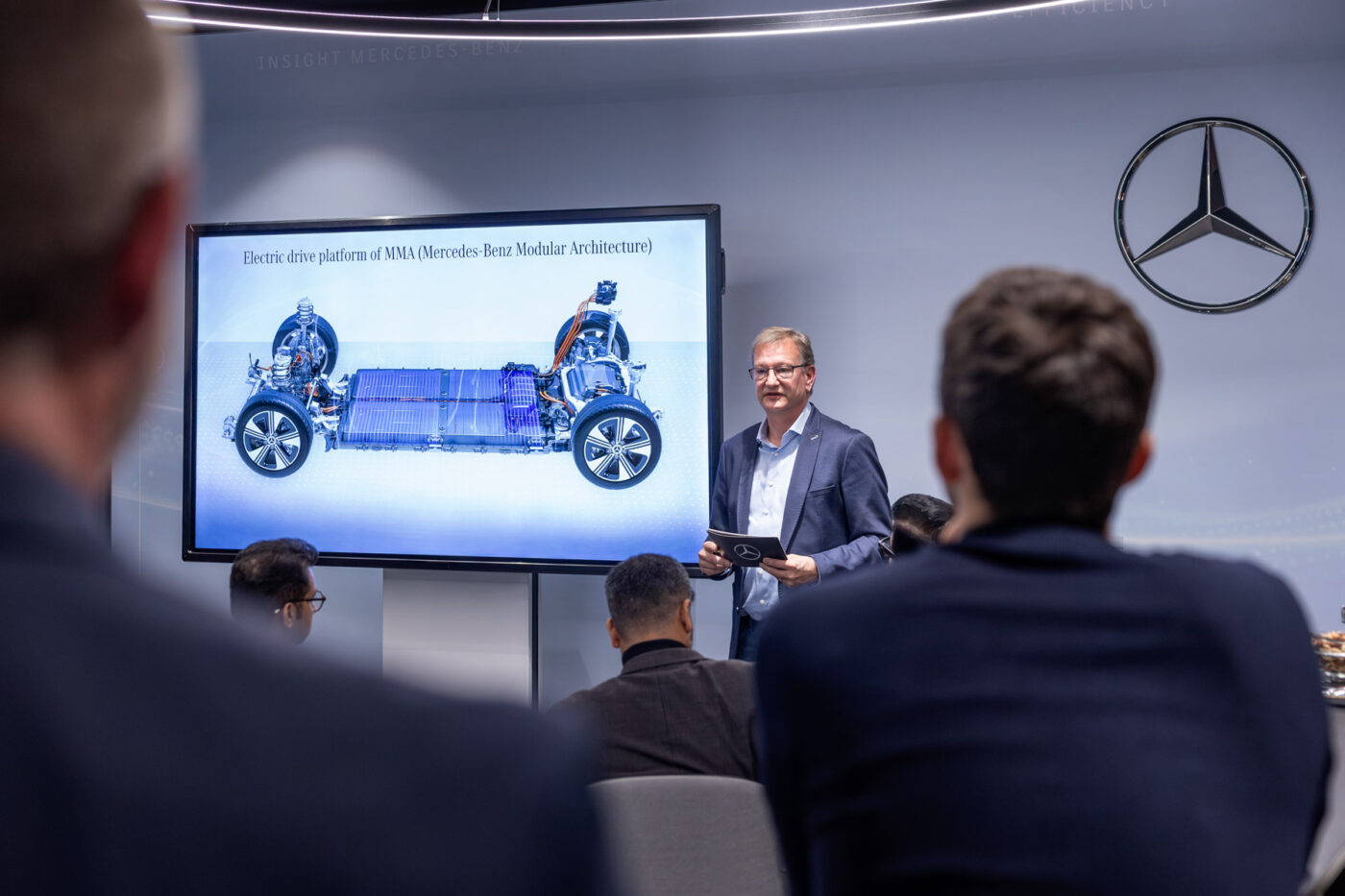
Auch fertige Prototypen können das „ESH“ verlassen, bleiben über die Messtechnik aber mit dem Standort verbunden. „Wenn die Kollegen auf der Straße eine Auffälligkeit feststellen, egal ob auf der Schwäbischen Alb, am Polarkreis oder in der Wüste, können sie im Fahrzeug einen Knopf drücken und der Datensatz wird an dieser Stelle mit einem Flag versehen“ erklärt Werner. „Wir können dann in Echtzeit auf diese Daten zugreifen und genau dieses Szenario so oft auf dem Prüfstand nachfahren, bis wir die Sache gelöst haben.“
Die Ingenieure haben die Prüfstände im ESH auch genutzt, um eine Rekordfahrt vorzubereiten, die die angepeilte „Zeiteffizienz“ demonstrieren sollte: Auf der Teststrecke im süditalienischen Nardò hat ein Vorserienfahrzeug des CLA stolze 3.717 Kilometer in 24 Stunden zurückgelegt. Geplant und überwacht wurde die Fahrt vom ESH aus, doch Simulationen und Prüfstandsläufe sind nur ein Teil der Arbeit – die Hard- und Software muss das auch in der Praxis umsetzen können. Mit 210 km/h Höchstgeschwindigkeit und 40 genau kalkulierten Ladestopps ist der Plan aufgegangen.
Zwar wird wohl kein CLA-Kunde jemals in die Situation kommen, über 3.000 Kilometer am Stück mit 210 km/h zu fahren. Einen Praxisnutzen für den Kunden sieht Test-Ingenieur Werner dennoch: „Ein Beispiel: Wir haben bei jedem Ladestopp die übliche Kommunikation mit der Ladesäule durchlaufen, wie es auch jeder Kunde macht. In diesem Prozess konnten wir einige Sekunden herausholen.“ Oder wie es Torsten Eder, Leiter der E-Antriebsentwicklung mit dem Blick aufs große Ganze ausdrückt: „Der Dauerlauf in Nardò beweist, dass unsere Technologien auch auf der Straße zuverlässig sind.“
24 Kommentare