BMW forscht an direktem Batterierecycling
Das „direkte“ Batterierecycling verzichtet auf die chemische oder thermische Aufbereitung der Materialien. Stattdessen werden die Materialien mechanisch voneinander getrennt – zumindest grob. Denn beim direkten Batterierecycling werden zum Beispiel bei der Kathode die Aktivmaterialien der Beschichtung von der Trägerfolie getrennt. Die Aktivmaterialien an sich werden aber nicht (chemisch oder thermisch) weiter aufgespalten, sondern können direkt in der Produktion neuer Zellen verwendet werden.
Im Falle von BMW arbeitet das neue CRCC in Kirchroth eng mit der Pilotfertigung von BMW in Parsdorf zusammen – dort können im Kompetenzzentrum Batteriezelle die in Kirchroth gewonnenen Rohstoffe testweise in einer Zellproduktion eingesetzt werden. „Mit dem neuen Kompetenzzentrum für Batteriezellrecycling erweitern wir unser Inhouse-Knowhow um einen weiteren Baustein: Von der Entwicklung über die Pilotproduktion bis zum Recycling schaffen wir einen geschlossenen Kreislauf für Batteriezellen“, sagt Markus Fallböhmer, Leiter Batterieproduktion bei der BMW AG. „Und das alles mit kurzen Wegen zwischen unseren Kompetenzzentren in Bayern.“
Der Autobauer hat in den Aufbau des CRCC nach eigenen Angaben rund zehn Millionen Euro investiert, die Arbeiten sollen 2025 abgeschlossen sein. Das Zentrum wird auf einer Fläche von 2.200 qm in die Erweiterung eines bestehenden Gebäudes integriert. Der Bau und Betrieb wird von der Encory GmbH verantwortet, einem Joint Venture der BMW Group und der Interzero Group. Die Münchner betonen, dass das „geistige Eigentum des Recyclingverfahrens vollständig bei der BMW Group“ liege. Übrigens: Die elektrische Energie aus den entladenen Zellen soll in Energiespeichern im Gebäude konserviert und für den Betrieb der Recycling-Anlagen genutzt werden.
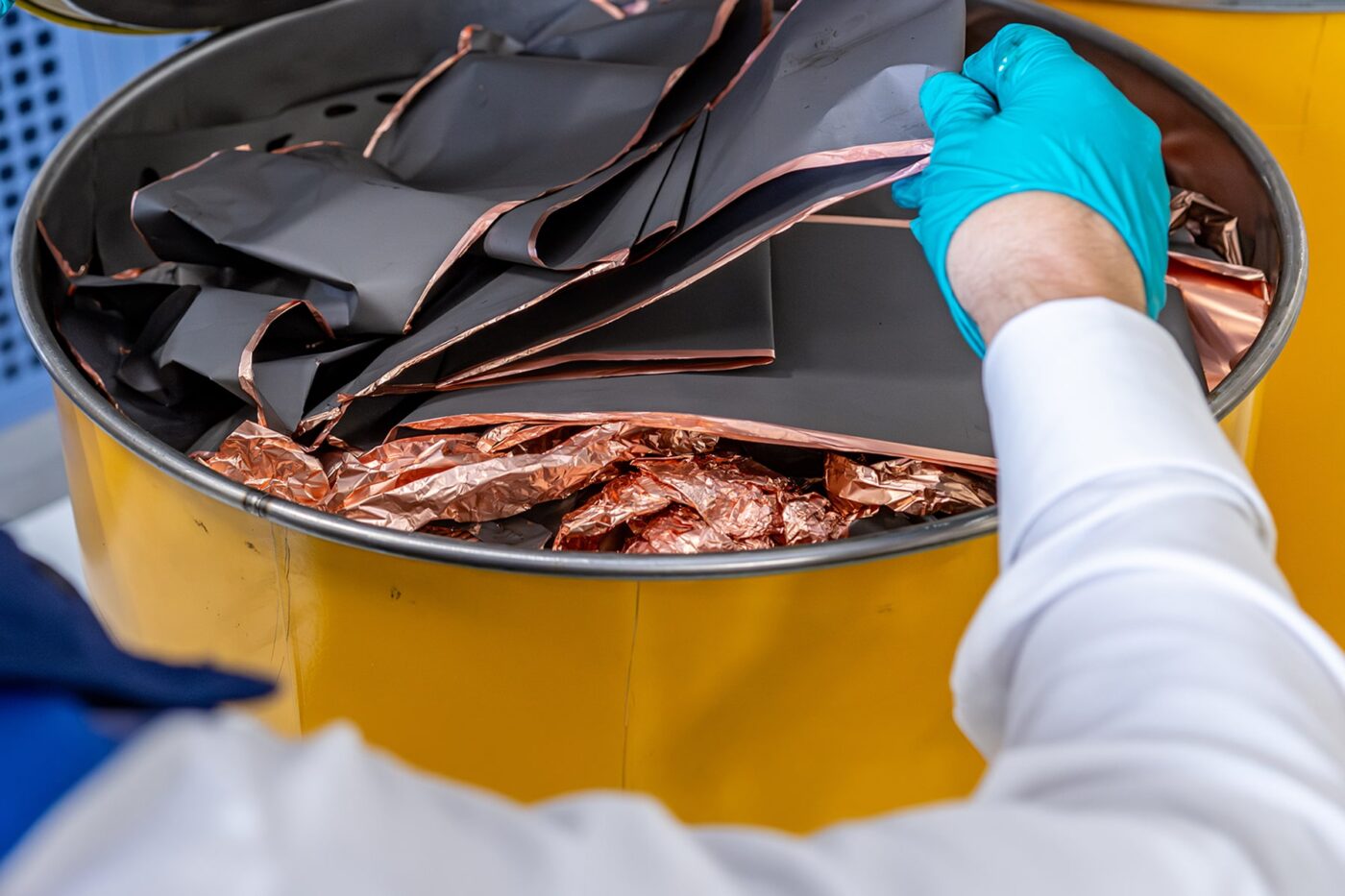
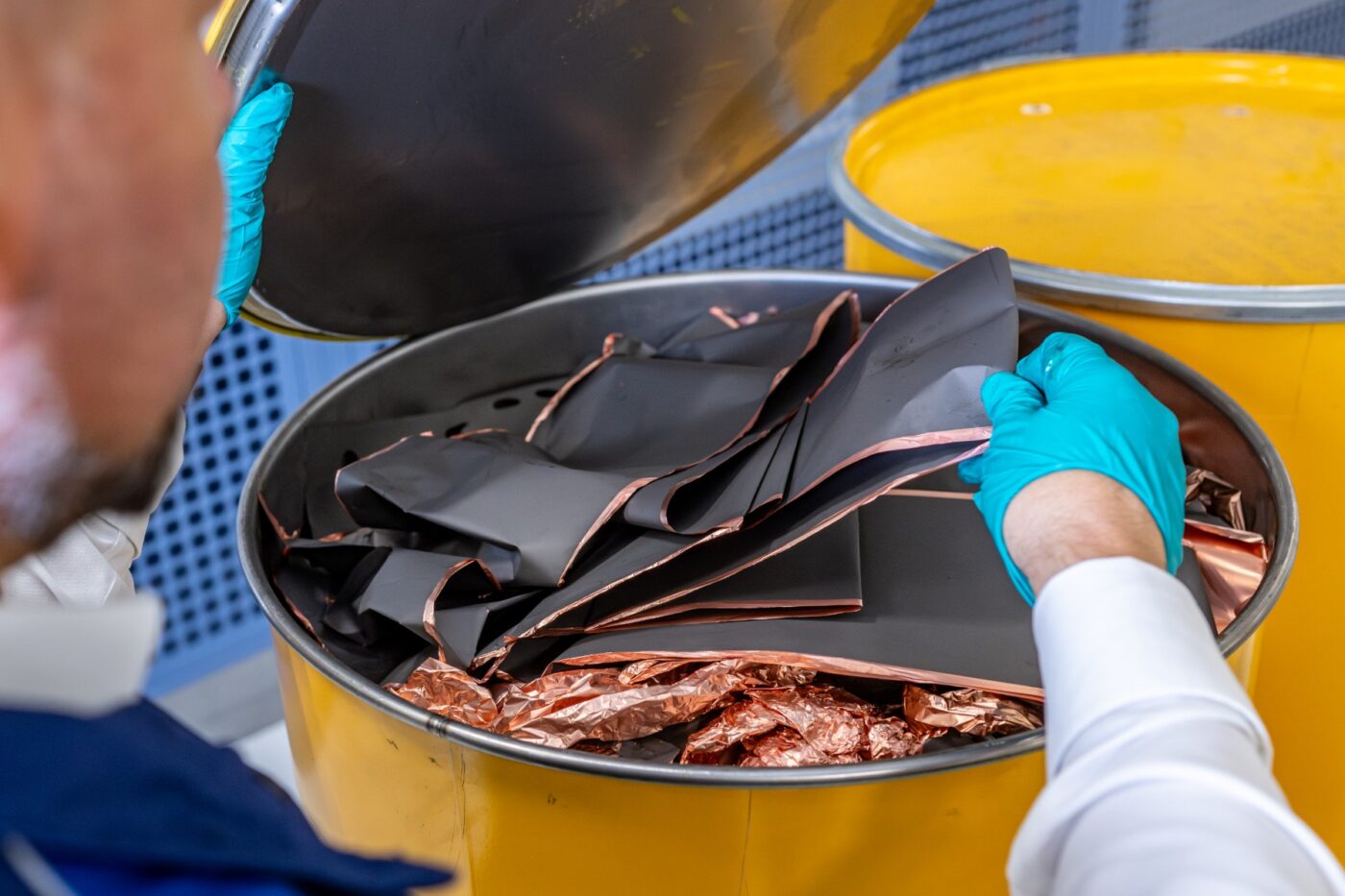
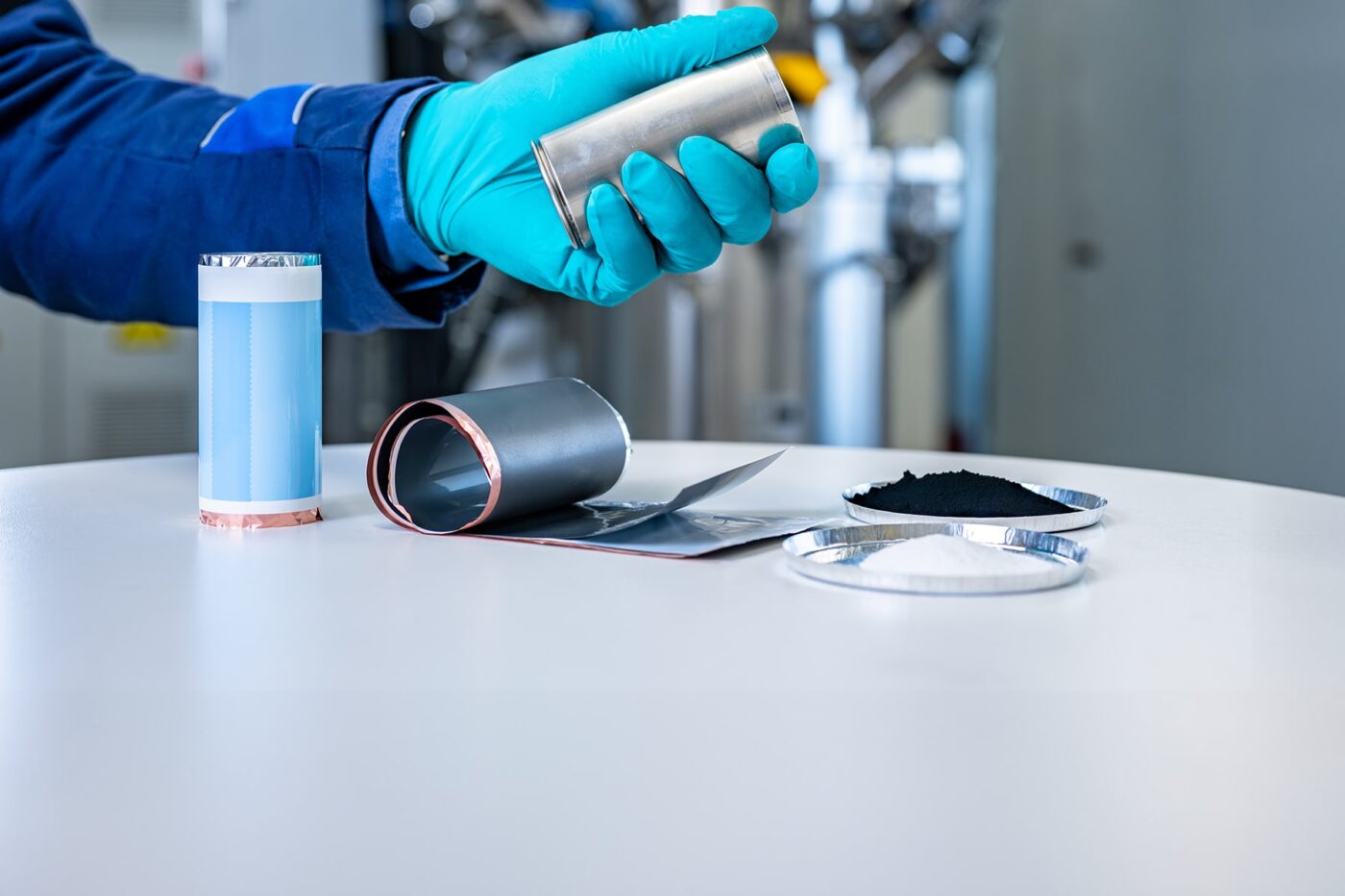
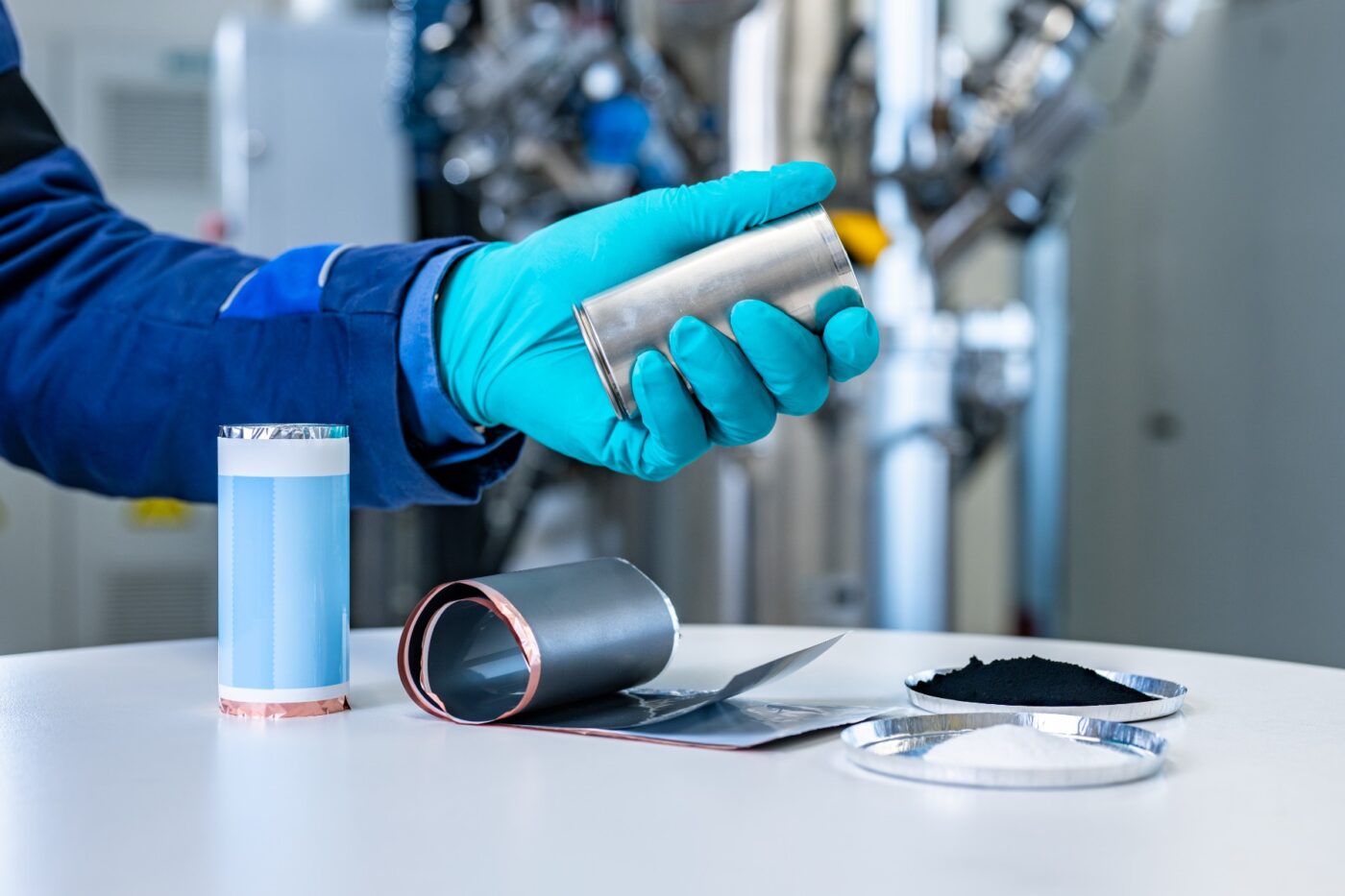
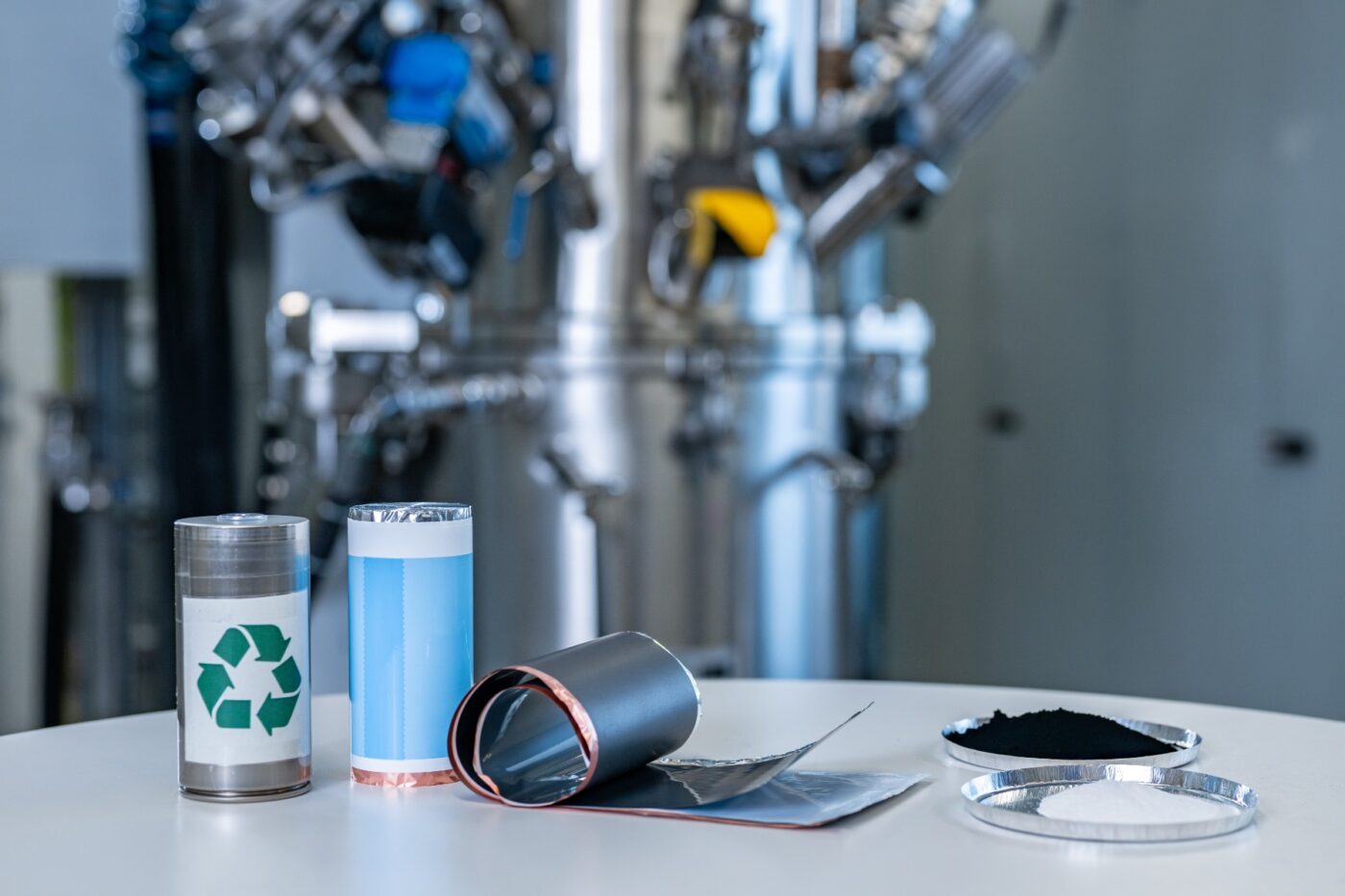
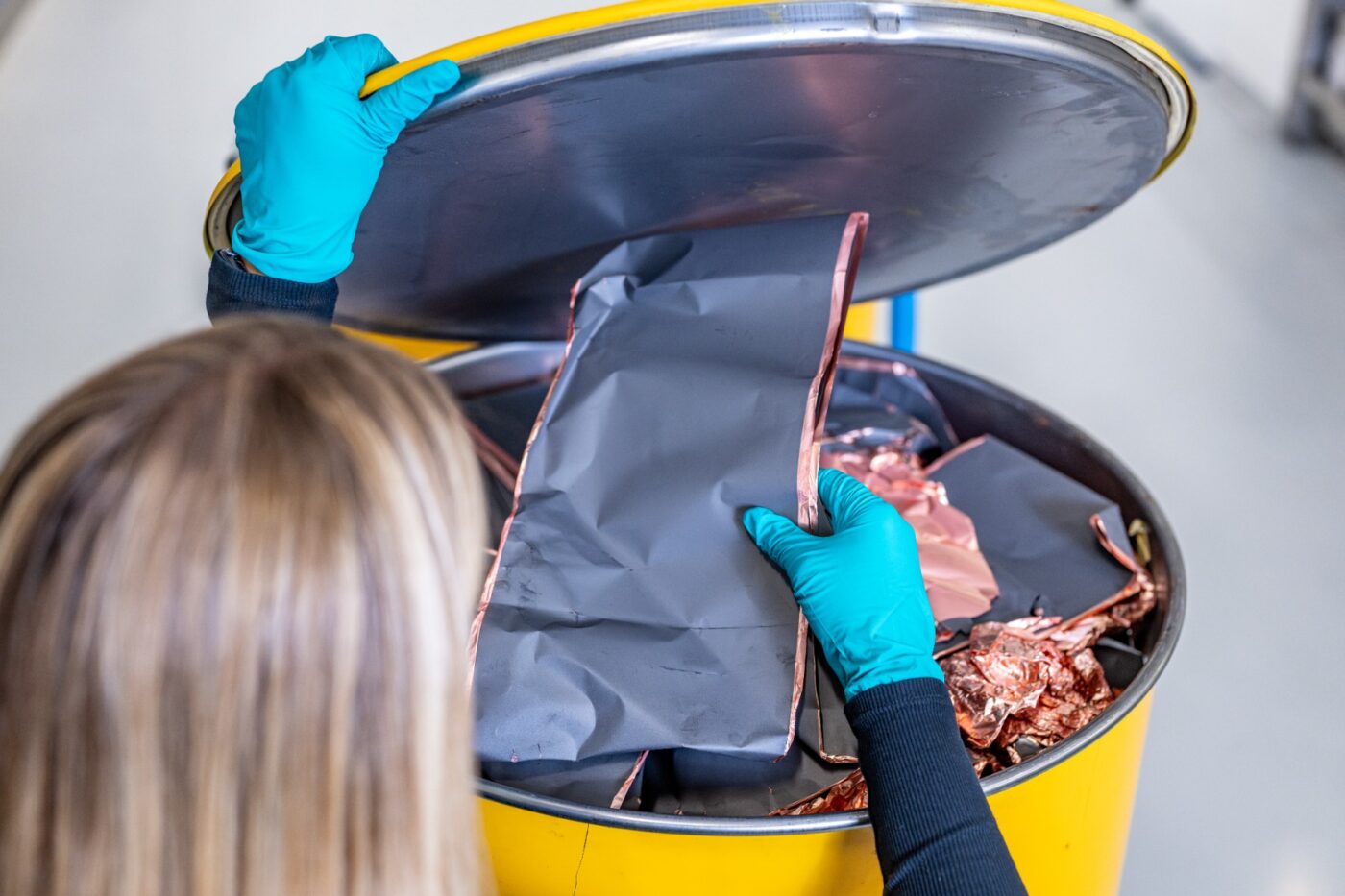

In der zweiten Jahreshälfte soll mit dem Aufbau der Anlagen im Gebäude begonnen werden, so BMW. Sobald dieser abgeschlossen ist, startet die Validierung des Recyclingverfahrens in seriennahen Prozessen. Damit will BMW nicht nur die Batterie nachhaltiger, sondern auch günstiger machen. „Das Direktrecycling wird dazu beitragen, die Kosten unserer Batteriezellpilotlinie zu reduzieren“, erklärt Fallböhmer.
Die Methode wurde BMW-intern in den Kompetenzzentren in München (Battery Cell Competence Center, BCCC) und Parsdorf (Cell Manufacturing Competence Center, CMCC) entwickelt. Im neuen CRCC wird es dann in einem größeren Maßstab angewendet, sodass nach seiner Inbetriebnahme jährlich Batteriezellmaterial im mittleren zweistelligen Tonnenbereich recycelt werden kann. „Das Recycling der Überschüsse aus der Parsdorfer Pilotfertigung erfolgt nach seiner Fertigstellung im neuen Kompetenzzentrum in Kirchroth. Die dort gewonnenen Rohstoffe werden dann wieder in der Zellproduktion in Parsdorf eingesetzt. So bleiben die Wege zwischen allen Kompetenzzentren kurz und wertvolle Rohstoffe gehen nicht verloren“, so BMW.
BMW ist mit dem Ansatz des direkten Batterierecyclings nicht alleine, auch andere Forschungsinstitute und Zellhersteller wie Farasis arbeiten daran. Der Vorteil ist, dass die aufwändigen und teuren Prozessschritte ausgelassen werden. Der Nachteil ist aber, dass die chemische Zusammensetzung der Aktivmaterialien gleich bleibt – eine NMC811-Kathode bleibt auch nach dem Recycling eine NMC811-Chemie. Werden die einzelnen Materialien im Recycling jedoch aufgetrennt, können sie bei der Produktion neuer Kathoden beliebig gemischt werden, was gerade Stand der Technik ist.
0 Kommentare